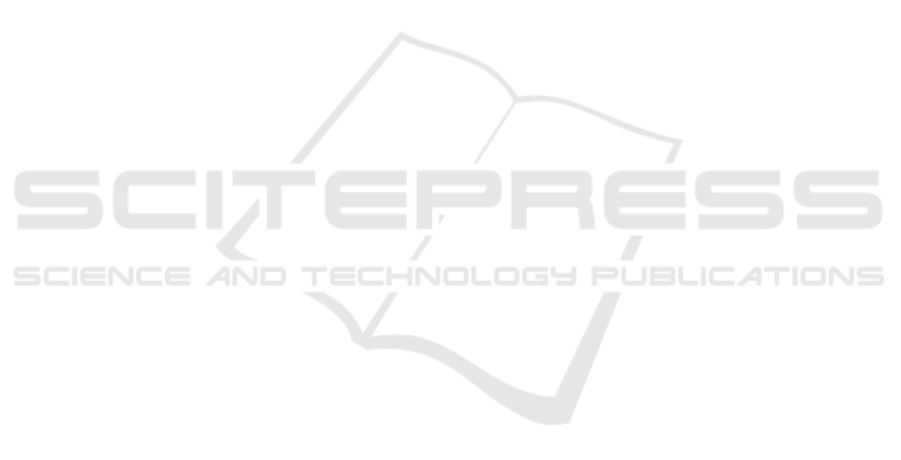
LEADER-FOLLOWER FORMATION CONTROL OF
NON-HOLONOMIC ROBOTS IN A REMOTE LABORATORY
Daniel Neamtu, Bart Wyns, Robin De Keyser and Clara Ionescu
Department of Electrical Energy, Systems and Automation, Ghent University, Technologiepark 913, Zwijnaarde, Belgium
Keywords:
Remote laboratory, Mobile robots, Formation control, Distance education.
Abstract:
This paper presents a remote laboratory for leader-follower formation control. The client-server architecture
of the remote laboratory is based on Matlab and JIM at the server’s side, and a Java applet created using Easy
Java Simulations at the client’s side. The implementation of the remote laboratory is described in detail and
the educational value is outlined by presenting some experimental results for formation control of two mobile
robots.
1 INTRODUCTION
Nowadays technology is evolving at an incredible
pace, providing us with possibilities that a few
decades ago were unimaginable. The development
of communication and information technologies has
completely changed the speed and penetration of in-
formation in today’s society. The teaching activity in
general has a lot to gain from the use of these new
technologies. Remote and virtual laboratories are be-
coming increasingly popular. Remote laboratories, as
compared to the classic on site instruction, present
several advantages (Dormido, 2004): i) continuous
availability of the laboratory for experimentation, ii)
there is no need for the students to travel to the univer-
sity’s site in order to perform the experiments, iii) op-
timal exploitation of the resources, iv) easy access to
different types of experiments. A very broad range of
applications can make the object of remote laborato-
ries, with some notable exceptions for example in the
chemistry field where safety requirements can pro-
hibit the use of a remote laboratory (Dormido, 2004).
In particular, remote laboratories are becoming very
popular in the field of control engineering mainly due
to the interactivity that they provide to the distance
teaching process. A few examples of remote labo-
ratories designed for performing control experiments
are given in (Vargas et al., 2009; Fabregas et al., 2009;
Farias et al., 2010), to mention just a few. These re-
mote laboratories are meant to remotely control a sin-
gle process (water tank, ball and hoop, DC motor etc.)
allowing the remote user to change the parameters of
the controller, visualizing incoming data and enable a
real-life view of the process itself.
The fields of robotics receives very much inter-
est both from the academic and industrial communi-
ties worldwide, which means that proper education in
this field becomes more and more important (Potkon-
jak et al., 2010). Building a remote laboratory for
robotic experiments is a complex task due to the in-
terdisciplinary character of this application. A few
examples of remote laboratories with the purpose to
experiment with robotic applications are presented in
(
ˇ
Safari
ˇ
c et al., 2005; Casini et al., 2009; Sayouti et al.,
2010).
In the remote laboratory presented in this paper
the final aim is to remotely control a group of mobile
robots so that they move in a leader-follower forma-
tion on a predefined trajectory.
The proposed implementation is based on Matlab
and Easy Java Simulations (EJS) (Esquembre, 2004).
EJS is a free open-source tool for easily creating sim-
ulations in Java, and targets students, teachers and re-
searchers who want to quickly create a graphical sim-
ulation. EJS was originally designed to be used by
students for interactive learning under the supervision
of educators with little programming experience. In
this implementation of a remote lab, the graphical in-
terface and the computational engine are separated.
The graphical interface was created using EJS and is
an applet that runs in the user’s browser.
Matlab is the most commonly used program in
teaching control engineering. In our remote labora-
tory implementation, the computational engine is rep-
485
Neamtu D., Wyns B., De Keyser R. and Ionescu C..
LEADER-FOLLOWER FORMATION CONTROL OF NON-HOLONOMIC ROBOTS IN A REMOTE LABORATORY.
DOI: 10.5220/0003476904850490
In Proceedings of the 3rd International Conference on Computer Supported Education (UeL-2011), pages 485-490
ISBN: 978-989-8425-50-8
Copyright
c
2011 SCITEPRESS (Science and Technology Publications, Lda.)