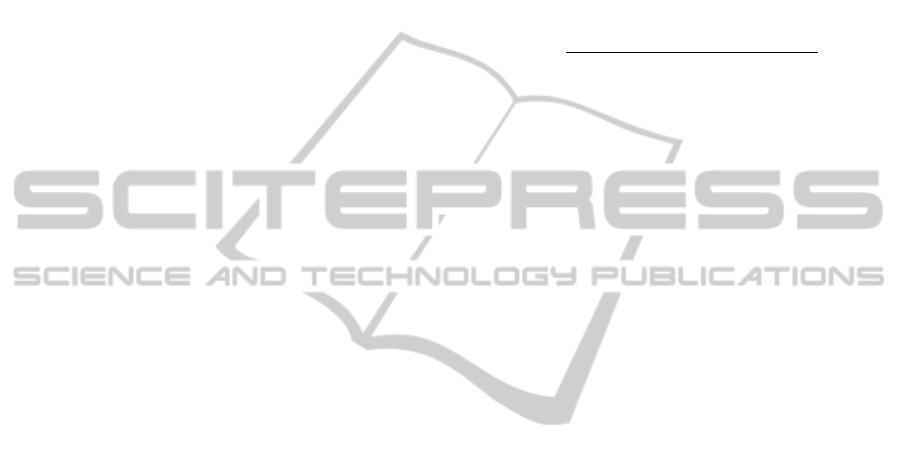
limit of control input respectively. Once the required
control input is beyond the upper or lower thresholds,
the AW compensator gets engaged. The
compensation command can be joined to the
feedback signal (
1aw
y
) or to the output of controller
directly (
2aw
y
). Such an approach is attractive in
practice because no restriction is imposed upon the
controller design.
3 EMBEDDED
CYLINDRICAL-ARRAY
MAGNETIC ACTUATOR
(ECAMA)
ECAMA is a type of Active Magnetic Bearing
(AMB) and designed for high-speed milling
applications. The proposed ECAMA and the spindle
are depicted in Fig. 2. In addition, a high-speed
motor (>20000 RPM) and a self-sensing module for
spindle position deviation measurement are
equipped at the two ends of spindle. The
configuration of the ECAMA is shown in Fig. 3. It is
mainly composed by the modified concave-type
yokes (Tsai and Hsu, 2007) and the I-shape
electromagnets. The prototype of the I-shape
electromagnets are shown in Fig. 4. Totally 1200
turns of coils are wound around each individual I-
shape silicon steel core.
4 CONTROL STRATEGY FOR
ACTUATOR WINDUP
The unconstrained controller employed in this work
is the PID controller. Owing to the integral action,
the output of controller tends to exceed the upper
limit of power amplifier once a large error exists.
The block diagram of spindle position control
system is shown in Fig. 5. The output of controller is
applied to the coils at ECAMA via power amplifiers.
By tuning the supplied coil current, the spindle
position can be regulated by the induced magnetic
forces. In fact, the AW compensator in Fig. 5 is a
gain. By compensating the input of integral term, the
controller output can be suppressed to be within
unsaturated region. Since the magnetic saturation
against ECAMA is determined by both the supplied
coil current and the area of I-shape silicon steel core,
the actual upper limit of the supplied coil current for
the AW compensator design in this work is
evaluated by experiments. According to the
experimental results (Tsai and Lee, 2010), the upper
and lower ampere-turns limits of coil are found to be
2000 and 0 ampere-turns respectively. Since the coil
wound on each I-shape electromagnet is 1200 turns,
the upper and lower limits of supplied coil current
are 1.67 A and 0 A respectively.
5 EXPERIMENTAL RESULTS
The test rig in our work, including the milling
machine (by How-mau Mchinery CO., LTD, Model
CNC-K3), is depicted in Fig. 6. The original milling
spindle of CNC-K3 is replaced by the proposed
ECAMA. Prior to the experiments, a set of PID
gains which can operate stably under low rotating
speed, i.e., 1000RPM is given. The follow-up
experiments are performed under spindle speed of
6000 RPM. The experimental results in X-axis are
shown in Fig. 7~Fig. 10. Fig. 7 and Fig. 8 are the
outputs of the controller without and with AW
compensation respectively. It is obvious that the
windup phenomenon induces large control outputs,
no matter in positive or negative side. On the
contrary, all the controller outputs are within
,200
which is referred to the supplied coil voltage of
V,20
under AW compensation. The spindle
position deviations in X-axis without and with AW
compensation are shown in Fig. 9 and Fig. 10. The
dotted lines in Fig. 9 and Fig. 10 are referred to the
maximum spindle position deviation which is
limited by the Auxiliary Bearing (AB) (Tsai, Shih
and Lee, 2010) to avoid collision in case
malfunction of ECAMA occurs. The spindle
position deviation under actuator saturation is shown
in Fig. 9. Drastic tremble of spindle and collision is
observed. However, the spindle position deviation,
shown in Fig. 10, is much improved under AW
compensation and no collision between spindle and
ECAMA/AB bearing takes place. In other words, the
efficacy of the AW compensator for actuator
saturation is verified.
6 CONCLUSIONS
The AW (Anti-Windup) compensator is proposed
and applied to ECAMA (Embedded Cylindrical-
Array Magnetic Actuator) to retain the performance
of spindle position regulation under actuator windup.
According to the experimental results, without any
modification of the PID controller, the controller by
aid of AW compensator can still operate well under
ICINCO 2011 - 8th International Conference on Informatics in Control, Automation and Robotics
196