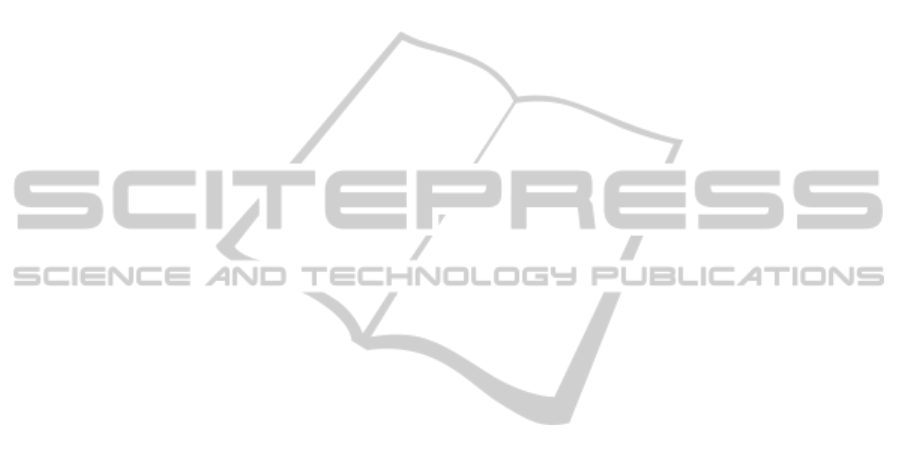
application, the part of the controller supplying
the control algorithm with input signals is highly
dependent on the nature and quality of input
signals and usually has to be changed
substantially.
Computing power of controller's hardware unit
may not be sufficient for execution of both the
complex control algorithm (Ettler, 1992) and
application of sophisticated signal processing
methods on low-quality input signals.
Because of an effort to minimize time delay
imposed by some signal processing methods on
the signals, the scan frequencies of signal
acquisition must be much higher than the actual
frequency of control loop, and this brings further
demands on computing power of the hardware
unit.
Last but not least, the all-in-one hardware unit
solution does not allow to position the input
signal data acquisition and digitization as near as
possible to the sensor which is desirable to avoid
long distance wiring and to reduce noise
influence.
3 SOLUTION
Possible solution of the above mentioned drawbacks
includes decomposition and functional and
topological distribution of the controller's hardware
unit. This approach is widely spread and is
commonly used in many control applications. Main
contribution of our solution consists in complex
approach to the processing of input signals with the
aim to find a base for a more or less universal
solution of input signal quality improvement in a set
of similar control applications.
3.1 Decomposition and Distribution
The original all-in-one solution of the controller is to
be decomposed first. The input signal acquisition is
detached from the controller's hardware unit and
realized by a separate hardware unit called signal
pre-processing subsystem (SPS). Generally, there
can be a set of SPSs in the framework of a particular
control application. The control algorithm and
output signal distribution is executed within the
original hardware unit.
The SPS is located as near as possible to the
sources of the acquired input signals.
The SPS processes the inputs and resulting
enhanced signals are transferred to the controller via
a dedicated high speed computer network.
3.2 Signal Pre-processing Subsystem
The signal pre-processing subsystem (SPS) is the
new key component of the controller.
3.2.1 Concept of Signal Processing in SPS
Processing of controller's input signals in the SPS
has the following key ideas:
Scan frequencies of input signal acquisition are
an order higher than the frequency of control
algorithm loop.
Acquired signal data is buffered before further
processing.
One input signal is processed by several signal
processing methods in parallel.
The currently best result of the particular signal
processing methods or a weighted combination
of several ones is chosen as final input to the
controller with the help of a probabilistic
algorithm of continuous decision making.
The latest values of processed signals are
transmitted via the network to the controller
upon request.
Real-time operating system is the base for the
application software structure. Structure and code of
the application tasks are kept as simple as possible to
spare the computing power and enable to increase
the scan frequencies of the SPS.
The increase of the signal acquisition scan
frequencies brings obviously better starting
conditions for subsequent signal processing
methods. Contribution of the increased scan
frequency of the SPS in comparison to the input
signal acquisition frequency of the original all-in-
one controller is illustrated by Figure 3.
Sufficient computing power of the SPS dedicated
to signal processing enables to process one signal by
several signal processing methods in parallel.
The selection and combination of the outputs
from the particular signal processing methods is the
matter of a specialized probabilistic algorithm of
continuous decision making. Outputs from this
algorithm are buffered in the SPS and prepared for
transmission to the controller.
3.2.2 Transmission of Pre-processed Input
Signals from the SPS to the Controller
As mentioned above, the pre-processed input signals
are ready and continuously updated in the SPS's
memory. For the transmission of the processed
signals to the controller, a local area network (LAN)
is used. It can bring difficulties together with
ICINCO 2011 - 8th International Conference on Informatics in Control, Automation and Robotics
416