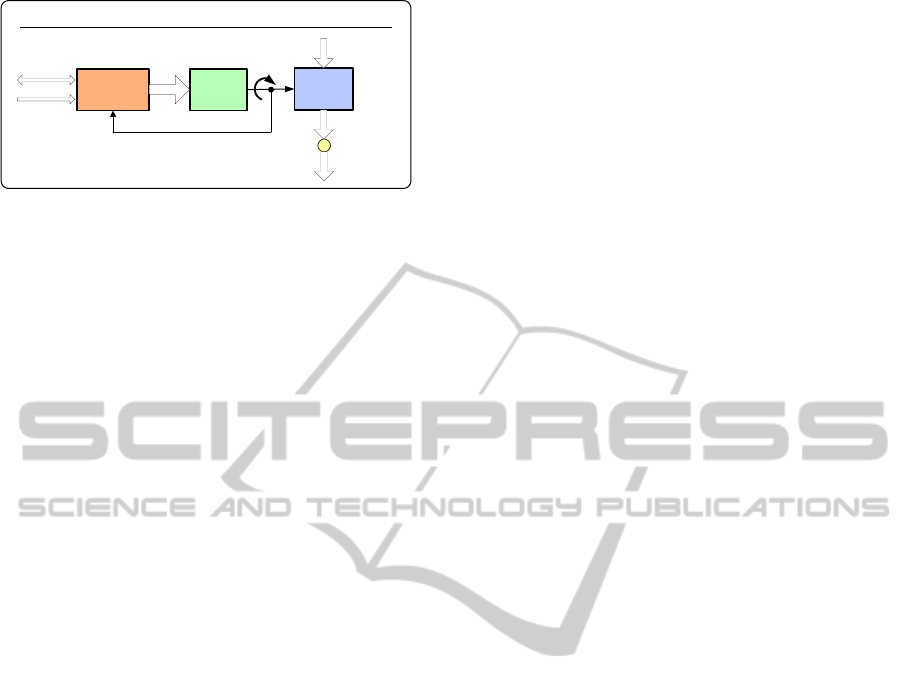
Figure 2: Block diagram of the FMP.
1.2 Control System Requirements
Requirements for the control system were defined
during the early stage of the project in consultation
with external aviation specialists. These
requirements include electrical characteristics,
reaction of the control system to defined incidents,
start-up characteristics, control commands etc.
The FMP’s variable flow rate will be controlled
by the Electronic Control Unit (ECU) to maintain
constant speed of the Auxiliary Power Unit (APU).
In parallel with the pump, a by-pass relief valve will
protect it against overpressure. The FMP shall
provide the fuel inlet temperature to the APU ECU.
The FMP shall control the fuel flow by varying the
pump speed for the following APU operations:
Start the APU (open loop: no closed loop
control on APU speed for the ECU),
Maintain the APU speed at a constant value
(closed loop on APU speed for ECU) and
transfer to the FMP via the digital data bus
and/or the analog setting input.
The most important requirements of the control
system are listed below.
1.2.1 Interface Characteristics
The control system of the FMP should be
controlled via a digital data bus or a single
analog signal,
CS together with the BLDC motor should be
supplied from an AC/DC bus with the option
of supply from a battery,
CS should receive only start/stop and flow
throttle commands,
CS should be able to indicate the flow level,
power bridge current, status word, FMP mode,
built-in-test results and start/stop command
acknowledgement,
The nominal power consumption should be
less than 250W, the peak power consumption
could be up to 500W for a defined period of
time.
1.2.2 Functional Requirements and
Performance Characteristics
CS shall ensure safe and soft start of the
BLDC motor under any conditions.
During operation the CS shall maintain the
fuel flow at required values.
CS shall enable internal parameters setting in
a dedicated maintenance mode.
CS shall be able to precisely meter fuel flow
during a defined interval.
The maximum underflow should be less then
2% at Δω > 40% and the fuel flow should
stabilize in 240 ms.
In case of stop command the FMP shall stop
in less than 100 ms.
Minimum fuel flow is 3 l/h and maximum 117
l/h.
1.2.3 Physical Requirements
CS should be designed for minimum
dimensions and weight.
CS cooling shall be designed with active fuel
cooling to withstand ambient air temperature
over +55°C.
CS shall ensure normal non-degraded function
under the defined circumstances and lifetime.
Nominal operational temperatures shall be -
55°C to +85°C, short-term operating
conditions shall be -55°C to +125°C.
During APU operation, the maximum steady
state flow in worst temperature conditions
(air: +85°C, fuel: +65°C) will be 76 l/h.
The CS shall restart without problem after
having been soaked 4 min at +125°C.
Beyond the above stated requirements, the
control system and the FMP shall be designed in
accordance with many other requirements regarding
atmospheric pressure, temperature variations and
humidity, shocks and vibrations, lightning and
electrostatic discharges. For certification purposes
the development, testing and verification must be
performed in accordance with the aviation standards
”RTCA/DO-178B – Software Considerations in
Airborne Systems and Equipment Certification”
(RTCA, Inc., 1992), ”RTCA/DO- 254 – Design
Assurance Guidance for Airborne Electronic
Hardware” (FAA Advisory Circulars, 2005) and
”RTCA/DO-160F – Environmental Conditions and
Test Procedures for Airborne Equipment” (RTCA,
Inc., 2007). Failure mode analysis (FMEA) of the
designed hardware and testing of the SW code by
means of dedicated tools are mandatory parts of the
FMP ARCHITECTURE
INTERFACE WITH
ECU
MOTOR
BLDC
FUEL
PUMP
CS with power
electronics
U,V,W
FUEL OUTLET
FUEL INLET
n
FUEL SENSOR
28 VDC
ICINCO 2011 - 8th International Conference on Informatics in Control, Automation and Robotics
420