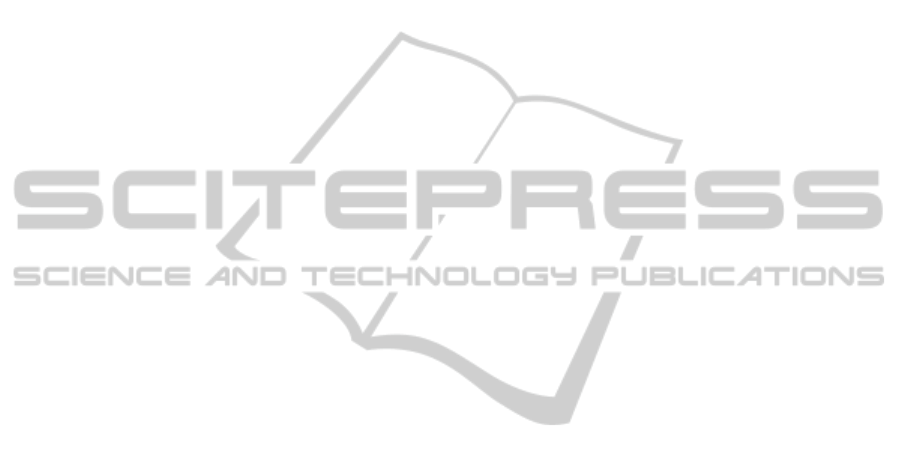
where:
Q(u,x,t) - increase of the quality index value
as a result of decision u, undertaken in
the state s=(x,t);
ˆQ(u,x,t) - estimation of the quality index value
for the final trajectory section after
the decision u has been realized;
i
(u,x,t) - component reflecting additional
limitations or additional requirements in
the space of states, i=1,2,...,n;
a
i
- coefficient, which defines the weight of i-th
component
i
(u,x,t) in the criterion q(u,x,t);
j
(u,x,t) - component responsible for
the preference of certain types of decisions,
j=1,2,...,m;
b
j
- coefficient, which defines the weight of j-th
component responsibles for the preference of
particular decision types.
The significance of particular local criterion
components may vary. The more significant a given
component is, the higher value is of its coefficient. It
is difficult to define optimal weights a priori. They
depend both on the considered optimization problem
as well as the input date for the particular
optimization task (instance). The knowledge
collected in the course of experiments may be used
to verify these coefficients. On the other hand,
coefficient values established for the best trajectory
represent aggregated knowledge obtained in
the course of experiments.
The presented method consists in the
consecutive construction of whole trajectories,
whilst their generation always begins from the initial
state s
0
=(x
0
,t
0
). For each generated trajectory, both
admissible and non-admissible, its final
characteristics is remembered and then used in
further calculations. The method is characterized by
the following features:
A trajectory sequence is generated; each
trajectory is analyzed, which provides
information about the DMP taken control;
Based on the analysis of so far generated
whole trajectories, it is possible to modify
coefficients used in local optimization or
change the form of local optimization
criterion when generating a new trajectory;
In the course of trajectory creation,
the subsequent state of the process is being
analyzed and it is possible to modify the form
or/and parameters used in local optimization.
4 SCHEDULING PROBLEM
WITH STATE DEPENDED
RETOOLING
To illustrate the application of the presented method,
let us consider the following real life scheduling
problem that takes place during scheduling
preparatory works in mines. The set of headings in
the mine must be driven in order to render the
exploitation field accessible. The headings form a
net formally, represented by a nonoriented
multigraph G=(W,C,P) where the set of branches C
and the set of nodes W represent the set of headings
and the set of heading crossings respectively, and
relation P
(W×C×W) determines connections
between the headings (a partial order between the
headings).
There are two kinds of driving machines that
differ in efficiency, cost of driving and necessity of
transport. Machines of the first kind (set M1) are
more effective but the cost of driving by means of
them is much higher than for the second kind (set
M2). Additionally, the first kind of machines must
be transported when driving starts from another
heading crossing than the one in which the machine
is, while the second type of machines need no
transport. Driving a heading cannot be interrupted
before its completion and can be done only by one
machine at a time.
There are given due dates for some of
the headings. They result from the formerly prepared
plan of field exploitation. One must determine
the order of heading driving and the machine by
means of which each heading should be driven so
that the total cost of driving is minimal and each
heading complete before its due date.
There are given: lengths of the headings dl(c),
efficiency of both kinds of machines V
Dr(m)
(driving
length per time unit), cost of a length unit driven for
both kinds of machines, cost of the time unit waiting
for both kinds of machines, speed of machine
transport V
Tr(m)
and transport cost per a length unit.
The problem is NP-hard (Kucharska, 2006).
NP-hardness of the problem justifies the application
of approximate (heuristic) algorithms. A role of
a machine transport corresponds to retooling during
a manufacturing process, but the time needed for
a transport of a machine depends on the process state
while retooling does not.
ICINCO 2011 - 8th International Conference on Informatics in Control, Automation and Robotics
26