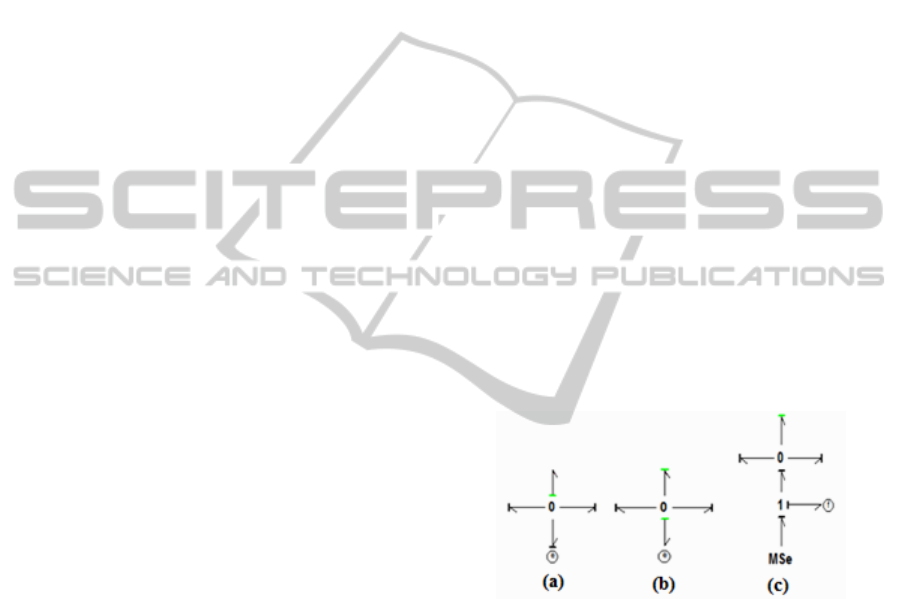
actuators (Tagina, 1995). In (Samantaray et al.,
2006), residuals are directly generated in the
Diagnostic Bond Graph (DBG), and a fault signature
matrix (FSM) is elaborated by covering causal paths
from residuals detectors to the components.
Therefore, the efficiency and robustness of these
methods depend on the model’s accuracy.
In case of uncertain parameters systems, (Djeziri,
2007); (Djeziri et al., 2009) proposed a robust
diagnosis algorithm, from a BG model in Linear
Fractional Transformations (LFT) form. They
derived ARRs in which they separated the quantity
of energy given by the uncertain part from the
residual to be evaluated, this idea allows the
generation of adaptive thresholds for fault detection.
A study of sensitivity was elaborated to deduce
detectability indexes defining the detectable value of
the residual in case of faults and parameters
uncertainties. In (Bouallègue et al., 2010), a method
for robust fixed and adaptive thresholds is proposed.
This method exploits the sensitivity of residuals to
different system parameters in order to determine
their thresholds; the FSM is used for isolation. In
(Bouslama-Bouabdallah et al., 2006), a fuzzy logic
approach applied to residuals deduced from the BG
model is used in detection stage. For isolation, the
FSM is transformed into inference rules allowing the
determination of the fault’s origin.
The main contribution of this paper is to use the
bond graph model directly in the task of robust FDI
in case of uncertain parameters systems. The
detection module is based on a fuzzy logic system.
For isolation, two causal reasoning based methods
were proposed.
This paper is organized as follows: Section 2
details the notion of DBG used to generate directly
the residuals in the BG model. Section 3 describes
the proposed fuzzy detection method. Section 4
presents two isolation methods: signature matrix and
exoneration. Section 5 describes the hydraulic
benchmark composed of three tanks. Finally,
different results and their interpretations are given in
section 6.
2 RESIDUALS GENERATION
FROM DBG
The generation of Analytical Redundancy Relations
(ARRs) from the bond graph model uses the
structural relations given by the conservation law in
all 0 and 1 junctions and aims to express the
unknown variables by those known (inputs and
sensors). This method cannot deal with algebraic
loops, so, unknown variables cannot be eliminated.
So, the structural independence of the different
residuals has to be checked with existing residuals.
In (Samantaray et al., 2006), a direct method for
ARR generation from BG model is proposed. The
causality inversion of detectors (which are
considered as sources) has been proposed as a
unified approach to generate residuals.
When the bond graph model is assigned
preferred differential causality and using inversion
of sensor causalities, if necessary, the following five
compositions are possible (Samantaray et al., 2006):
1. Inverted causality in effort sensor (De),
2. Inverted causality in flow sensor (Df),
3. non-inverted causality in effort sensor (De),
4. non-inverted causality in flow sensor (Df),
5. Inversion of signal sensor, Ds, to signal
source, Ss (for controllers).
Let us consider the case of inverted causality in
the effort sensor, De, (see Figure 1). This sensor will
be equivalent to an effort source (measurements
from real process), so expression of the source
loading flow variable is equated to zero (Samantaray
et al., 2006). This expression is a residual (it does
not involve any states, since all storage elements are
in differential causality) which’s measured by a
virtual flow sensor (Samantaray et al., 2006).
Figure 1: (a) Sensor e in behavioral model, (b) inverted
causality in e and (c) substituted representation for
inverted causality in e.
The bond graph of the system with these
substitutions using preferred derivative causality is
called the Diagnostic Bond Graph (DBG)
(Samantaray et al., 2008).
3 DETECTION USING FUZZY
LOGIC APPROACH
In ideal conditions, residual value is equal to zero in
fault free context. In practice, due to the uncertainty
and the measurement noise, residuals are different
from zero. Thresholds are used to deduce whether
ICINCO 2011 - 8th International Conference on Informatics in Control, Automation and Robotics
60