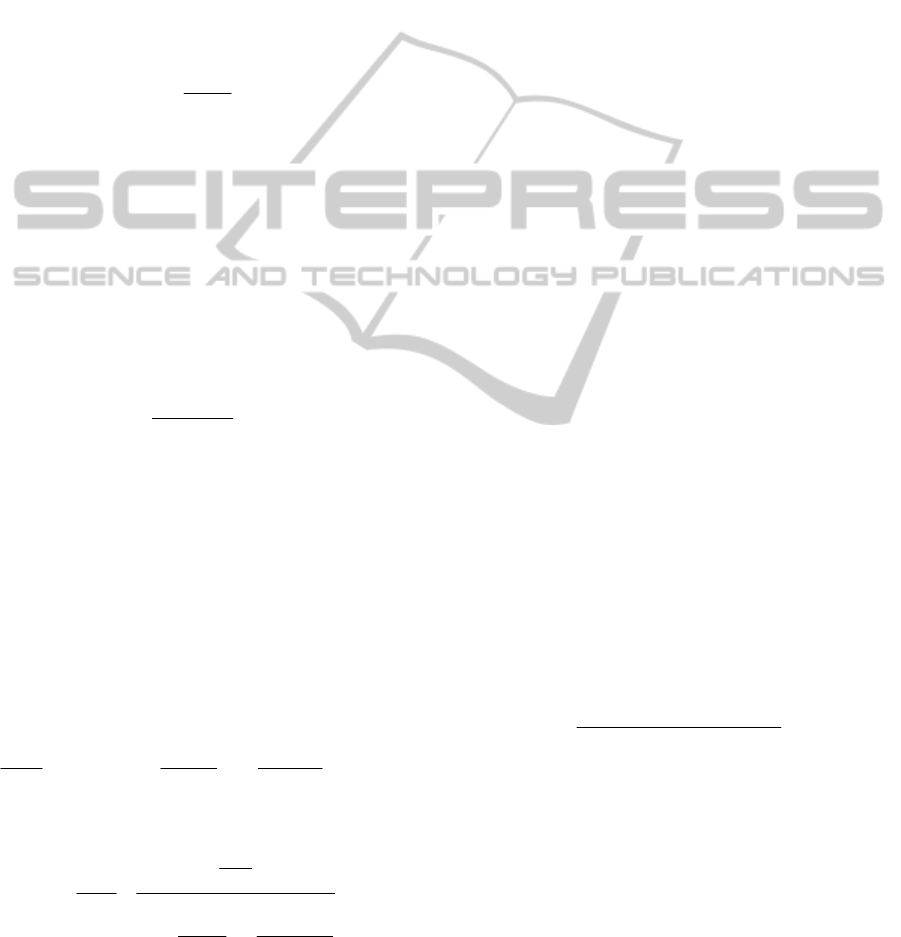
volume a small fraction of chamber volume.
However the flow considered here is liquid causing
a simplification because the spring effect that exists
due to the gas flow is negligible in liquid flow case.
Analysis consists of applying Newton’s law by
balancing the forces along the tube in the
longitudinal axis y. Initially is considered that
p
m
=p
i
=p
0
(p
0
an initial arbitrary value) when p
i
changes slightly in some way. Then it is considered
at this point that p
i
and p
m
mean the excess pressures
over and above p
0
. The force f
i
due to the pressure p
i
is given by:
i
t
ii
p
d
Apf
4
2
π
==
(12)
The viscous force f
v
due to the wall shearing stress is
given by the division of Equation (11) by the area of
the pipe wall:
tv
yLVLf
πμπμ
88 ==
(13)
where y
t
is the liquid displacement due to p
i
action.
This displacement causes a volume change
dV
ol
=πd
t
2
y
t
/4 and pressure excess p
m
=πBd
t
2
y
t
/(4V
ol
)
(B is the elastic coefficient). The equivalent force is
given by:
ol
tt
m
V
yBd
f
16
42
π
=
(14)
Applying Newton’s law along the longitudinal axis
implies to balance the forces and equate to the fluid
mass m multiplied by the acceleration a, or:
amfff
mvi
⋅
−−
(15)
Above equation is useful for uniform velocity
distribution. However, the quadratic velocity profile
verified in Equation (7) indicates that a correction
factor must be used in the right side of Equation
(15). In this case the quantity m.a must be multiplied
by 4/3. Then, Equation (15) can be rewritten as:
t
t
t
ol
t
ti
t
y
Ld
y
V
Bd
yLp
d
316
8
4
2
42
2
ρπ
π
πμ
π
=−−
(16)
Applying Laplace transform in Equation (16) yields:
()
()
()
ol
VL
t
Bd
S
t
d
S
L
sP
sY
sG
i
t
yp
ρ
π
ρ
μ
ρ
16
2
3
2
24
2
4
3
++
==
(17)
Last equation relates the displacement of the
meniscus due to the pressure applied at the tip of the
capillary. Moreover, it permits an evaluation of the
dynamical behaviour by the variation of its physical
parameters.
3 EXPERIMENTAL SET UP AND
COMPARISON
The meniscus was observed with a video camera
coupled to a microscope. The video signal was
sampled at 70 ms and digitalized with a video board
installed in the personal computer. It was developed
a software based on Imaq Vision for LabView for the
meniscus detection. This software is based on
pattern recognition and gives as result the number of
pixels (Npixel) concerning to the previously chosen
initial position. It was coupled a “T” connection at
the tip of the capillary. The capillary was previously
filled with silicone oil. It was linked at one of the
inputs of the T connection an air duct supplied by an
air compressor. At the other input was coupled a
pressure sensor with reading rate equal to 10mV/psi.
After the air compressor to be switched on, the
readings of both meniscus position, and voltage
signal due to the sensor were collected and stored in
the computer. In the Figure 2 is shown the curve due
to the meniscus displacement (in Npixel) and the
curve due to the voltage signal in the pressure
sensor. It can be seen in Equation (17) that the final
value is L/B. This means that if the length L is
increased then the meniscus displacement is also
increased. It was used the following values for each
physical parameter in the Equation (17), with B, µ,
and ρ being attributed to the silicone oil, and L
chosen according to the optical resolution: L=0.15m;
d
t
=270 10
-6
m; ρ=900 Kg/m
3
;
B=2.18 10
9
N/m
2
;
μ=10
-3
Kg/m s. Substituting the above values results
in:
72
6
10.074.88.365
10556.5
)(
+⋅+
⋅
=
−
ss
sG
yp
(18)
To compare the mathematical model to the
experimental response it is necessary to transform
the pressure sensor signal measured in volt in
pressure dimension. Then, the voltage signal must be
multiplied by (1/0.6mV) x psi, with 1psi=6894.6
N/m
2
. The relation between the meniscus
displacement in meter and Npixel was previously
measured with a rule adapted in the microscope lens.
It was found 1 pixel=1/6.36x10
5
m. Applying the
transformed input pressure signal to the Equation
VALIDATED MODEL OF A PRESSURE MICROPROBE FOR WATER RELATIONS OF PLANT CELLS
435