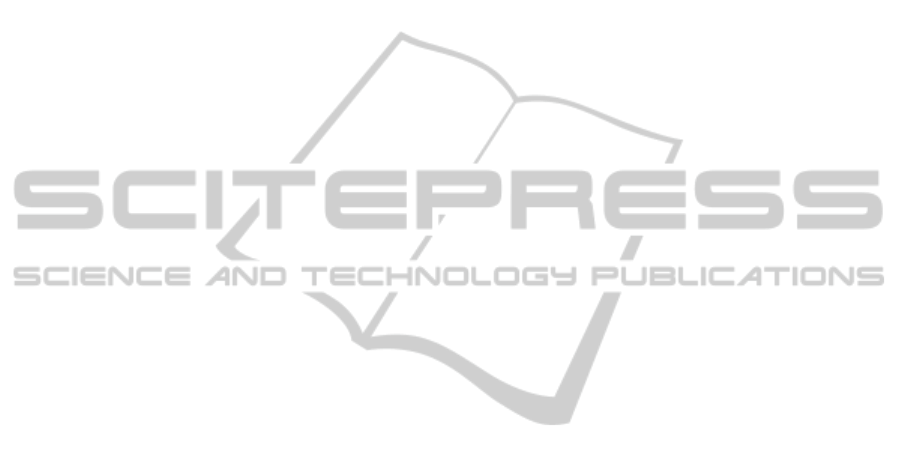
every leg has been found to be more in
compared to the second joint. Moreover, for
controlling of first joint of Leg 1, torque
requirement is observed to be considerably
higher than the other legs. It is also to be noted
that torque requirement for each joint during
swing phase is less in compared to the support
phase. This is because of the presence of
support reaction forces.
6 CONCLUDING REMARKS
This paper presented kinematics, dynamics and
trajectory planning of a three-legged robot. Direct
and inverse kinematics has been analyzed, while the
robot is following a straight line path. Movement of
the robot is ensured considering that at any instant of
time only one leg can be in swing phase while the
other two will provide necessary support. Joint
torques has been computed continuously for the full
locomotion cycle and compared between the legs.
All the developed mathematical models have been
tested through computer simulations on a P-IV PC.
Computational complexity of the code developed for
solving the mathematical expressions is found to be
very low, making it suitable for on-line implementa-
tions. More torque requirement has been observed
for the first joint of each leg and for every joint
during support phase than in swing phase. For the
first joint of each leg, torques varies between
(-0.004N-m to 0.00585N-m) and those for the
second joint vary between (-0.00003N-m to
0.00007N-m). This is a very low torque requirement
and low power servo motors will be sufficient to
control them.
The present study can be extended in a number
of ways, such as, static and dynamic stability
analysis, optimization of joint torques of the robot
while it is following a curvilinear path. Moreover,
presently the performance of the robot has been
tested through computer simulations. Real
experiments will be more interesting in this regard.
The authors are working with some of these issues
presently.
REFERENCES
Barreto J. P., Trigo A., Menezes P., Dias J., 1998.
Almeida A. T. D, FBD-the free body diagram method.
Kinematics and dynamic modeling of a six leg robot,
IEEE Int. Conf. on Robotics and Automation, pp. 423-
428
Bretl T., Rock S., Latombe J. C., 2003. Motion planning
for a three-limbed climbing robot in vertical natural
terrain, in Proc. IEEE Intl. Conf. on Robotics and
Automation, Taipai, Taiwan
Craig J. J., 1986. Introduction to robotics: mechanics and
control, Addison-Wesley, Singapore
Denavit J., Hartenberg R. S., 1955. A kinematic notation
for lower-pair mechanisms based on matrices, ASME
Journal of Applied Mechanics, Vol. 77, pp. 215-221
Erden M. S., Leblebicioglu K., 2007. Torque distribution
in a six-legged robot, IEEE Trans. on Robotics, vol.
23(1), pp. 179-186
Goswami A., 1999. Foot rotation indicator point: a new
gait planning tool to evaluate postural stability of
biped robots, in: Proc. of the IEEE Int. Conf. on
Robotics and Automation, Detroit, USA, vol. 1, pp.
47–52
Jamhour E., Andre P. J., 1996. Planning smooth trajectory
along parametric paths, Mathematics and Computers
in Simulation, vol. 41, pp. 615-626
Koo T. W., Yoon Y. S., 1999. Dynamic instant gait
stability measure for quadruped walking, Robotica,
vol. 17, pp. 59-70
Mi Z., Yang J., Kim J. H., Abdel-Malek K., 2011.
Determining the initial configuration of uninterrupted
redundant manipulator trajectories in a manufacturing
environment, Robotics and Computer-Integrated
Manufacturing, vol. 27, pp. 22-32
Mohri A., Furuno S., Yamamoto M., 2001. Trajectory
planning of mobile manipulator with end–effectors
specified path, in Proc. of the Intl. Conf. on Intelligent
Robots and Systems, Maui, Hawali, USA, pp. 2264-
2269
Song S. M. and Waldron K. J., 1989. Machines that walk:
the adaptive suspension vehicle, The MIT Press,
Cambridge, Massachusetts
Vukobratovic M., Borovac B., Surla D., Stokic D., 1990.
Biped locomotion-dynamics, stability, control and
applications, Springer-Verlag.
ICINCO 2011 - 8th International Conference on Informatics in Control, Automation and Robotics
166