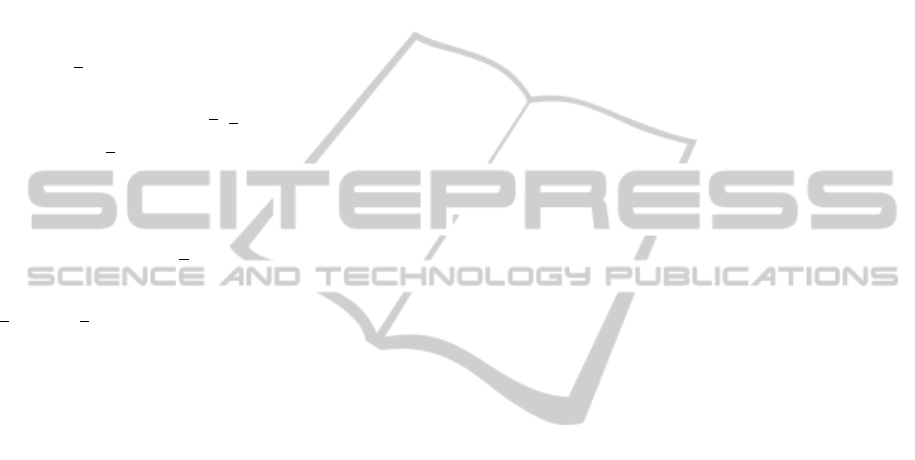
4 MONITORING THE
DETECTOR WITH A MODEL
VALIDITY INDEX
The validity of the test (11) can be violated if GP
model is forced to make predictions at the points x
far from the learning set L . In practice, it might of-
ten happen that process model, originally trained in
certain operating region(s), is employed in a new op-
erating region not included in the learning set.
In this paper we rely on the observation that sensi-
tivity is inherent to the Gaussian process models. We
focus on y i.e. the scaled noise-free mapping of input
regressor x, which is related to y as follows
y(x(t)) =
√
v·y(x(t)) + n(t)
y(t) ∼ N (0,
˜
C(x(t),x(t)))
where
˜
C : R
D×2
→ R is modified covariance function
defined by
˜
C(x(i),x( j)) = exp
−
1
2
(x(i) −x( j))
T
W(x(i) −x( j))
Furthermore, note also that x(i) = x( j) implies
y(x(i)) = y(x( j)). Assume L = {x
i
,i = 1,...,N}. Let
the modified covariance matrix of the learning set
L be
˜
Σ
Σ
Σ(L ,L ) = k
˜
σ
ij
=
˜
C(x
i
,x
j
)k,i, j ∈ {1, ...,N}
Now, we start by adopting the notion of the distance
between a new regressor x and the learning set L .
Intuitively, if x = x
k
,k ∈ {1,...,N} then the distance
should be zero.
Proposition 1. Assume the learning set L =
{x
i
,i = 1,...,N} and x is a regressor. The distance
between x
x
x and L is
δ(x,L ) =
˜
C(x, x) −
˜
Σ
Σ
Σ(x,L )
′
˜
Σ
Σ
Σ(L ,L )
−1
˜
Σ
Σ
Σ(x,L ). (12)
In eq. (12) the meaning of
˜
Σ
Σ
Σ(x,L ) is
˜
Σ
Σ
Σ(x,L ) = [
˜
C(x, x(1))...
˜
C(x,x(N))]
′
In the same manner as in case of a single regressor
x one can associate distance to the covariance matrix
of the predicted y(X) conditioned on L . Actually, the
result (12) is extended as follows
D(X,L ) =
˜
Σ
Σ
Σ(X,X) −
˜
Σ
Σ
Σ(X,L )
′
˜
Σ
Σ
Σ(L ,L )
−1
˜
Σ
Σ
Σ(X,L ).
(13)
Again, if X ⊂ L then by borrowing the derivation
from the Proposition 1 one can see that D
D
D = 0
0
0. If X
X
X is
‘far’ from L , D
D
D →I.
Definition 1. The validity index I of the GP model
is proposed as being equivalent to the distance of a set
of regressors from the learning set as follows
I = trace(D(X,L )). (14)
5 EXPERIMENTAL RESULTS
To demonstrate the performance of the above FD
scheme, a case of a cold rolling mill is addressed.
In this process the output strip thickness belongs to
the key process variables. Its control is not trivial and
several approaches are being used to overcome the re-
lated technical problems (Ettler et al., 2007). One of
them relies on exploiting additional redundancybased
on available measured signals and mathematical mod-
els. Therefore, the on-line detection of faults in in-
strumentation and appropriate accommodation is key
for efficient controller design. The estimated value is
directly usable for the thickness control and for mill
operators. The estimator output is in the form of the
probability distribution thus providing clear informa-
tion about reliability of the estimation (Ettler et al.,
2007).
In order to illustrate the method proposed above,
we will focus just on the relationship between thick-
ness H
2
(k), z(k) and rolling force F(k), where k de-
notes the sampling instance. It reads as follows
H
2
(k) = f(z(k),F(k)) (15)
where f is an unknown function which can be de-
scribed by Gaussian process model.
The set of 450 representative input data samples
is used for training of the model (15).The model is
validated with 110 input data samples different from
those used for training.
The proposed statistical test (14) and the validity
index (18) have been used to detect bias in the H
2
sensor. To illustrate the performance a simulation run
consisting of four parts is presented.
First, in the period 0-430 samples the process op-
erates in a fault-free mode. Moreover, in that period
the operating region belongs to the region encom-
passed in the learning set. The response of the detec-
tor is seen in the figure. The window length is taken
M = 50 samples. The process output is well predicted
by the model so that the detector is indicating no-fault
with low value of the validity index.
In the period 430-950 samples an offset f
y
= 100
in H
2
sensor appears. One can see that the test statistic
almost immediately crosses the threshold value thus
indicating the presence of fault. The validity index
stays around zero, indicating that the process is oper-
ating in validated region.
In the third period 950-1450 the process operates
without fault.
At k = 1450 the operating point changes. The
detector receives data not envisaged in the learning
stage, Both the test statistics and validity index grows
indicating that something unusual is going on in the
FAULT DETECTION BASED ON GAUSSIAN PROCESS MODELS - An Application to the Rolling Mill
439