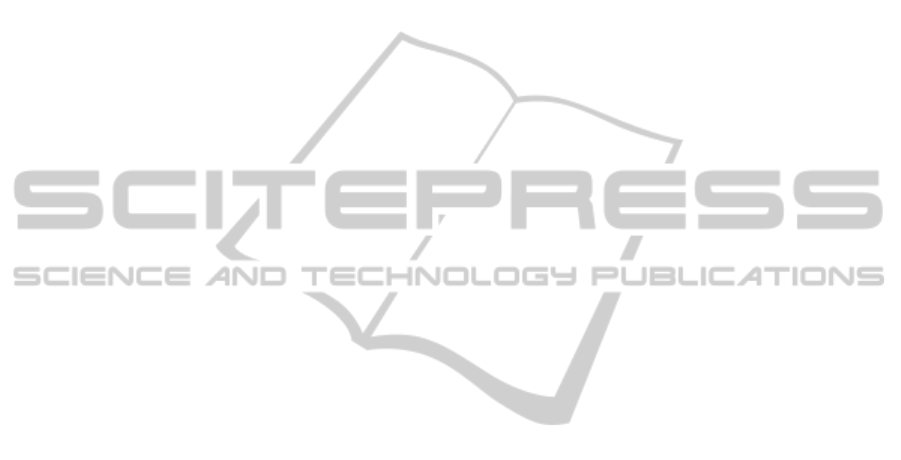
design and traceability between design artefacts.
This is why we are currently working with the
requirement sub-profile of UML AP. With this
work, we aim to support the detailed definition of
requirements but also documentation of information
originating from risk and hazard analysis phases.
The rationale is that the requirements of safety
functions are based on these analyses but the
information is not always visible for, for example,
the software developers, which makes it difficult to
judge the correctness and completeness of design.
REFERENCES
Biehl, M., DeJiu, C. and Törngren, M. 2010 “Integrating
safety analysis into the model-based development
toolchain of automotive embedded systems”. In:
LCTES 2010, pp 125-132, New York, NY, USA,
2010. ACM.
Carrasco, J. and Dormido, S. “Analysis of the use of
industrial control systems in simulators: State of the
art and basic guidelines”. 2006. ISA Transactions, Vol
45, Number 2, April 2006, pp. 295–312
Dougall, J. Applications and benefits of real-time I/0
simulation for PLC and PC control systems. 1998. ISA
Transactions, Vol. 36. No. 4. 1998, pp. 305-311.
Ferrarini, L., Dede, A., Salaun, P., Tuan Dang, Fogliazza,
G. 2009. “Domain specific views in model-driven
embedded systems design in industrial automation”.
INDIN 2009 the 7th IEEE International Conference on
Industrial Informatics, June 23-26, 2009, Cardiff, UK.
Friedenthal, S., Moore, A., Steiner, R. 2008 “A practical
guide to SysML”. Morgan Kaufmann OMG Press, San
Francisco. 2008
Hästbacka, D., Vepsäläinen, T., Kuikka, S. 2011. Model-
driven Development of Industrial Process Control
Applications, The Journal of Systems and Software
(2011), In Press, Accepted Manuscript, doi:10.
1016/j.jss.2011.01.063
IEC 61508: Functional safety of electrical/electronic/
programmable electronic safety-related systems. parts
1-7. 2010
Jones, C. 2008. “Software quality in 2008: A survey of the
state of the art”. Software Productivity Research LLC.
http://www.jasst.jp/archives/jasst08e/pdf/A1.pdf
(achieved 13.2.2011). 59 p.
Karhela, T. 2002. “A software architecture for
configuration and usage of process simulation models:
Software component technology and XML-based
approach” PhD Thesis, VTT Technical Research
Centre, Finland.
Object Management Group. 2003. Technical Guide to
Model Driven Architecture: The MDA Guide. Version
1.0.1 (formal/2008-04-03) Edition.
OpenModelica project website. 2011. http://www.ida.liu.
se/pelab/modelica/OpenModelica.html
Ritala, T., Kuikka, S. 2007. “UML Automation Profile:
Enhancing the Efficiency of Software Development in
the Automation Industry”, The Proceedings of the 5th
IEEE International Conference on Industrial
Informatics (INDIN 2007), Vienna, Austria, July 23-
27, 2007, pp. 885-890.
Schamai, W. 2009. “Modelica Modeling Language
(ModelicaML) – a UML Profile for Modelica”,
Technical Report 2009:5, EADS IW, Germany,
Linköping University, Institute of Technology.
Strasser, T., Rooker, M., Ebenhofer, G. 2009a. “MEDEIA
- Model-Driven Embedded Systems Design
Environment for the Industrial Automation Sector”.
1st Version of the MEDEIA open source modelling
prototype (documentation). Available: http://www.
medeia. eu/26.0.html
Strasser, T., Rooker, M., Hegny, I., Wenger, M., Zoitl, A.,
Ferrarini, L.,Dede, A., Colla, M. 2009b. “A research
roadmap for model-driven design of embedded
systems for automation components”. INDIN 2009 the
7th IEEE International Conference on Industrial
Informatics, June 23-26, 2009, Cardiff, UK.
Tranoris, C., Thramboulidis, C. 2006. “A tool supported
engineering process for developing control
applications”. Computers in Industry, Vol. 57, pp.
462-472, 2006.
Vepsäläinen, T., Hästbacka, D., Kuikka, S. 2008. “Tool
Support for the UML Automation Profile - for
Domain-Specific Software Development in
Manufacturing”, The Proceedings of the 3rd
International Conference on Software Engineering
Advances, Sliema, Malta, October 26-31 2008. pp. 43-
50.
Vepsäläinen, T., Hästbacka D. and Kuikka, S. 2009. ”A
Model-driven Tool Environment for Automation and
Control Application Development - Transformation
Assisted, Extendable Approach”. In Proceedings of
the 7th Nordic Workshop on Model Driven Software
Engineering, Tampere, Finland, August 26-28, 2009.
Vepsäläinen, T., Hästbacka, D., Kuikka S., 2010a.
"Simulation Assisted Model-Based Control
Development - Unifying UML AP and Modelica ML",
in 11th International Middle Eastern Simulation
Multiconference, Alexandria, Egypt, December 1-3,
2010a.
Vepsäläinen, T., Sierla, S., Peltola, J and Kuikka, S.,
2010b. ”Assessing the Industrial Applicability and
Adoption Potential of the AUKOTON Model Driven
Control Application Engineering Approach”,
Proceedings of International Conference on Industrial
Informatics. Osaka, Japan, July 13-16, 2010b.
Zoughbi, G., Briand, L., Labiche, Y. 2007. “A UML
Profile for Developing Airworthiness-Compliant
(RTCA DO-178B), Safety-Critical Software”. In:
MODELS 2007. LNCS, vol. 4735, pp. 574–588.
Springer, Heidelberg (2007)
SIMULATION ASSISTED, MODEL-BASED DEVELOPMENT OF SAFETY RELATED INTERLOCKS
275