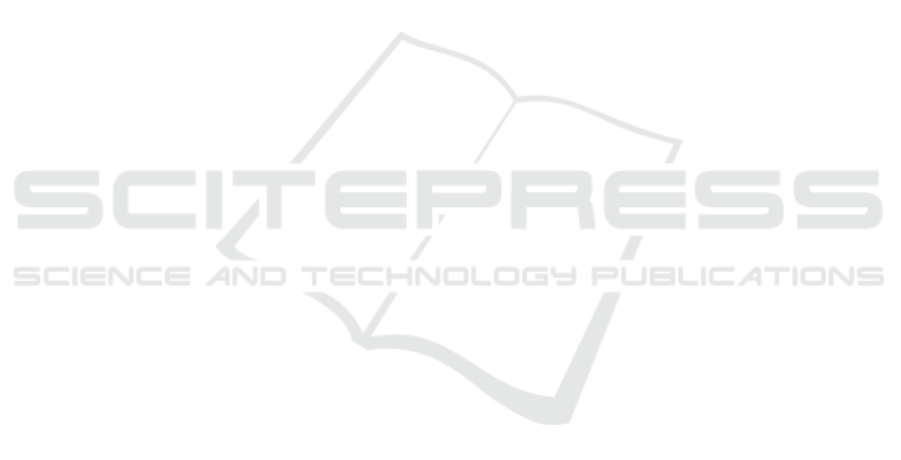
A FUZZY-PI CONTROLLER FOR WIND TURBINE DRIVEN DFIG
OPTIMIZED USING GENETIC ALGORITHMS
Lawrence K. Letting
1
, Josiah L. Munda
1
and Yskandar Hamam
1,2
1
Tshwane University of Technology, Pretoria, South Africa
2
ESIEE-Paris, Paris-Est University, LISV, UVSQ, Paris, France
Keywords:
DFIG, Fuzzy-PI control, Optimization, Genetic algorithms.
Abstract:
This paper presents the design of optimal TSK-fuzzy PI controller for the rotor side converter (RSC) of a
doubly fed induction generator (DFIG) in a grid connected wind generation system. The optimization strategy
is based on binary genetic algorithms. The controller is used to regulate the active and reactive power and hence
extract maximum energy from the system under varying wind speeds. Pitch angle control is used to regulate
the rotor angular speed while the active and reactive power are controlled by the rotor voltage supplied by the
RSC. The stator flux oriented reference frame is adopted. A fuzzy-PI controller with a minimum rule base
of nine rules is realized. The controller is implemented in C code as a dynamic linked library and simulated
using LabVIEW. Simulation results are presented.
1 INTRODUCTION
Wind energy is the fastest growing and the most
promising renewable energy source in the world to-
day. It is non-polluting, free and economically vi-
able. In addition, there has been a rapid technological
development in wind turbine technology (Munteanu
et al., 2008). In the recent past there has been an in-
creased use of DFIG’s in small power plants due to
their unique capabilities (Abedi et al., 2010). The
special features of DFIG are: it can supply power
at constant voltage and frequency; the rotor can op-
erate in both sub-synchronous or super-synchronous
speeds; the rating of the power converter is approxi-
mately 30% of the rated wind turbine power and; the
generated active and reactive power can be indepen-
dently controlled (Abo-Khalil et al., 2007).
To ensure maximum utilization of wind energy
in variable speed power plants, the stator active and
reactive power are controlled separately by varying
the rotor current of the DFIG using a vector control
scheme. A power converteris used to control the rotor
voltage. The control of power converters connected to
the DFIG is traditionally accomplished using propor-
tional and integral (PI) controllers. However, wind
energy conversion systems (WECS) are highly non-
linear with time-varying system parameters such as
wind speed and reference power values. This makes
it difficult to design optimal PI-controller gains using
either modern or classical control theory (Abedi et al.,
2010).
Artificial intelligence based methods using ge-
netic algorithms, particle swarm optimization (PSO),
and fuzzy logic have been introduced in order to im-
prove controller performance in WECS (Elshafei and
Azzouz, 2011), (Lin et al., 2011), (Ren et al., 2009),
(Leite et al., 2009), (Vieira et al., 2008). (Lin et al.,
2011) presents a particle swarm optimized recurrent
fuzzy neural network used to track the maximum
wind energy with reference values obtained from an
adaptive model reference observer. In (Leite et al.,
2009) PI controller gains are tuned using PSO with
aim of improving DFIG performance under network
faults. (Vieira et al., 2008) optimizes the PI-controller
gains using genetic algorithms in order to improve
active power control and dc-link voltage regulation.
(Ren et al., 2009) presents a 49-rule fuzzy controller
used to control the rotor speed and is shown to give
better performance than PI-control. (Elshafei and Az-
zouz, 2011) reports the design of a 9-rule adaptive
fuzzy controller (AFLC) for regulating the dc-link
voltage. The AFLC is shown to give better perfor-
mance compared to a classical PI controller and a 9-
rule non-adaptive FLC. It has therefore been estab-
lished that fuzzy control offers a great potential in
control of WECS.
This paper proposes an automated strategy for
tuning two fuzzy controllers used in regulation of ac-
348
K. Letting L., L. Munda J. and Hamam Y..
A FUZZY-PI CONTROLLER FOR WIND TURBINE DRIVEN DFIG OPTIMIZED USING GENETIC ALGORITHMS.
DOI: 10.5220/0003601403480353
In Proceedings of 1st International Conference on Simulation and Modeling Methodologies, Technologies and Applications (SIMULTECH-2011), pages
348-353
ISBN: 978-989-8425-78-2
Copyright
c
2011 SCITEPRESS (Science and Technology Publications, Lda.)