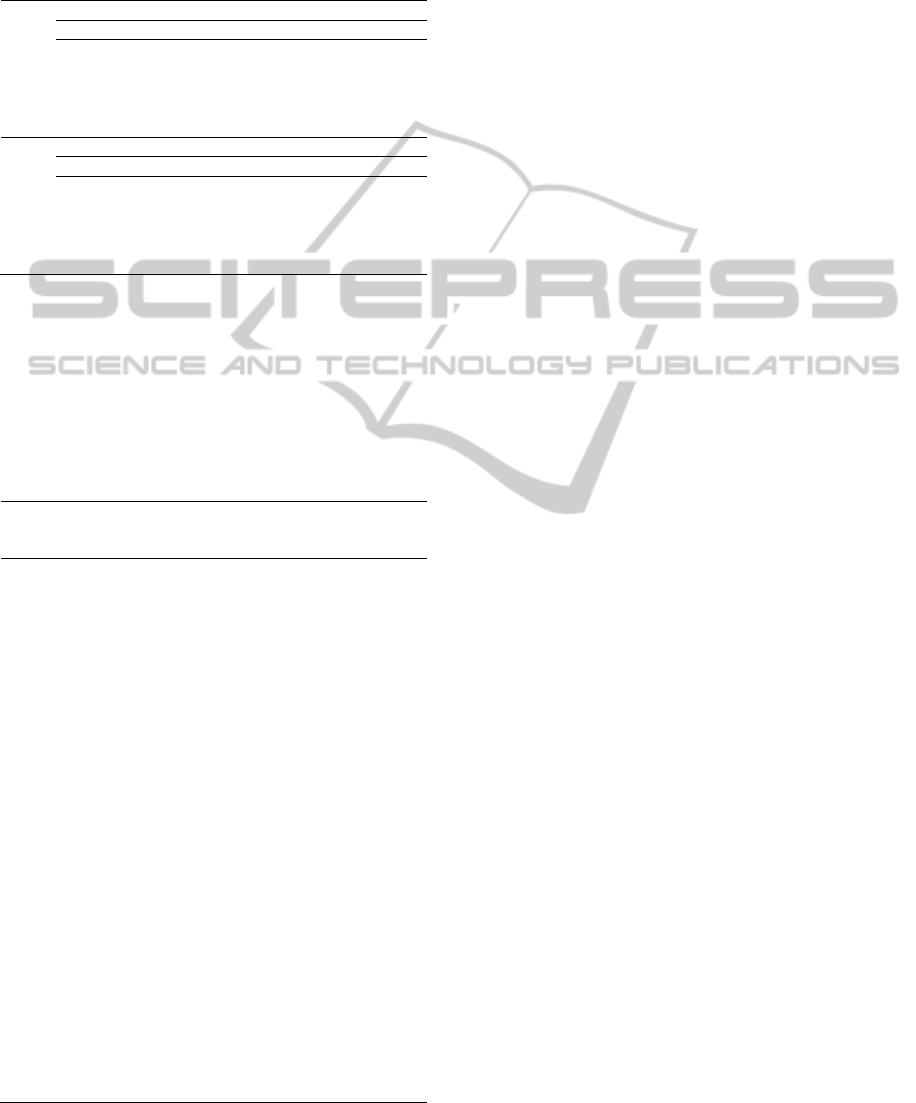
calculation guiding the structure parameter design
and structure design, in return, amending the process
simulation. The operating parameters and the results
of process simulation are listed in Table 3 and 4.
Table 3: The operating data of six columns in simulation.
T1 T2 T3
Top Bottom Top Bottom Top Bottom
N
T
100 100 120
R 28 9 22
Mr 134 152 141 159
T(
℃)
85 266 85 280 110 251
P (kpa) 105 114 105 114 80 115
T4 T5 T6
Top Bottom Top Bottom Top Bottom
N
T
100 100 104
R 18 30 19
Mr 158 166 168 164 169 154
T (
℃)
85 295 85 304 85 320
P (kpa) 105 114 105 114 105 114
As shown, the purity of methylnaphthalene, β-
methylnaphthalene, fluorene, and acenaphthylene all
reach industrial grade. And actually the field date of
this 25Kt/a pilot scale unit indicated that the purity
of the 5 main products all go beyond 95wt%, which
fully accommodated the requirements of fine
chemicals.
Table 4: The components of main production in simulation.
No.
Methylnapht
halene
Acenaphthyle
ne
Fluorene
β-
methylnaphthale
ne
1 6.28E-10 0.0000 0.0000 9.25E-10
2 5.95E-03 9.15E-11 0.0000 8.7E-03
3 1.76E-04 3.14E-13 0.0000 2.59E-04
4 9.67E-03 1.57E-09 0.0000 0.0142
5 1.64E-03 3.52E-10 0.0000 2.42E-03
6 0.637 9.16E-07 0.0000 0.9201
7 0.306 8.18E-06 0.0000 0.0417
8 3.18E-03 1.26E-11 0.000 9.22E-05
9 2.64E-03 6.34E-06 0.0000 3.70E-03
10 5.71E-03 7.16E-06 0.0000 8.18E-03
11 7.77E-09 1.81E-17 0.0000 1.15E-08
12 2.95E-03 3.47E-12 0.0000 5.85E-04
13 3.31E-07 7.33E-04 0.0000 1.00E-16
14 1.27E-09 3.35E-04 0.0000 0.0000
15 4.89E-08 1.16E-03 0.0000 0.0000
16 9.24E-10 1.96E-03 0.0000 0.0000
17 7.21E-07 9.27E-13 0.0000 3.23E-16
18 3.29E-05 4.66E-04 0.0000 6.43E-20
19 0.0000 5.51E-05 0.0000 0.0000
20 0.0260 7.33E-11 0.0000 9.41E-08
21 0.0000 0.9695 4.07E-12 0.0000
22 9.75E-15 0.0182 0.0000 0.0000
23 1.46E-20 1.58E-03 1.68E-07 0.0000
24 2.02E-20 5.71E-03 1.36E-08 0.0000
25 0.0000 3.05E-05 0.0000 0.0000
26 0.0000 9.03E-08 1.15E-03 0.0000
27 0.0000 8.72E-09 1.47E-04 0.0000
28 0.0000 1.22E-04 0.9706 0.0000
29 0.0000 5.23E-06 0.0278 0.0000
30 0.0000 1.19E-07 2.77E-04 0.0000
31 0.0000 4.54E-05 1.44E-18 0.0000
32 0.0000 0.0000 2.44E-20 0.0000
3 CONCLUSIONS
A novel process based on distillation coupled with
crystallization for the separation washing oil to
reclaim high grade fine chemicals is presented in
this work, from first step simulative research to the
successful field fulfillment. It demonstrates that this
process can utilize washing oil more
comprehensively with up to 5 fine chemicals,
namely, α-methyl-naphthalene, β-methyl-
naphthalene, fluorene, dibenzofuran and
acenaphthylene as principal products, and
naphthalene fraction, medium washing oil (dimethyl
naphthalene), as well as heavy washing oil of
improved quality as byproducts. In addition, results
from a converged simulation revealed these main
products were in high purity, suggesting the
feasibility of this hybrid scheme, which was then
verified by field running data.
On this foundation, by the aid of high efficient
packing technology, a 25Kt/a pilot scale unit was
designed, and has already successfully run over 12
months.
REFERENCES
González, A. M. D., Gutierrez, B. C., Casal, B. M. D.,
2008. The use of solvents for purifying industrial
naphthalene from coal tar distilled oils. Fuel
Processing Technology.
Liang, X., Xue, Y., 2008. The abstraction of fluorene and
dibenzofuran from fas absorber oil. Thesis.
Song C., Schobert H. H., 1993. Opportunities for
developing specialty chemicals and advanced
materials from coals. Fuel Processing Technology.
Wang, F., 2004. Extraction of washing oil distillate from
tar and its application in fine chemistry industry. Coal
Chemical Industry.
Yang, R., Duan, R., 2006. Extraction, application and
prospect of the components of wash oil. Coal
Chemical Industry.
Zhang, X., Yan, H., 2002. Brief introduction to wash oil
processing technology of the Chemical Co., Nippon
Steel Corporation. Fuel & Chemical Processes.
SIMULTECH 2011 - 1st International Conference on Simulation and Modeling Methodologies, Technologies and
Applications
428