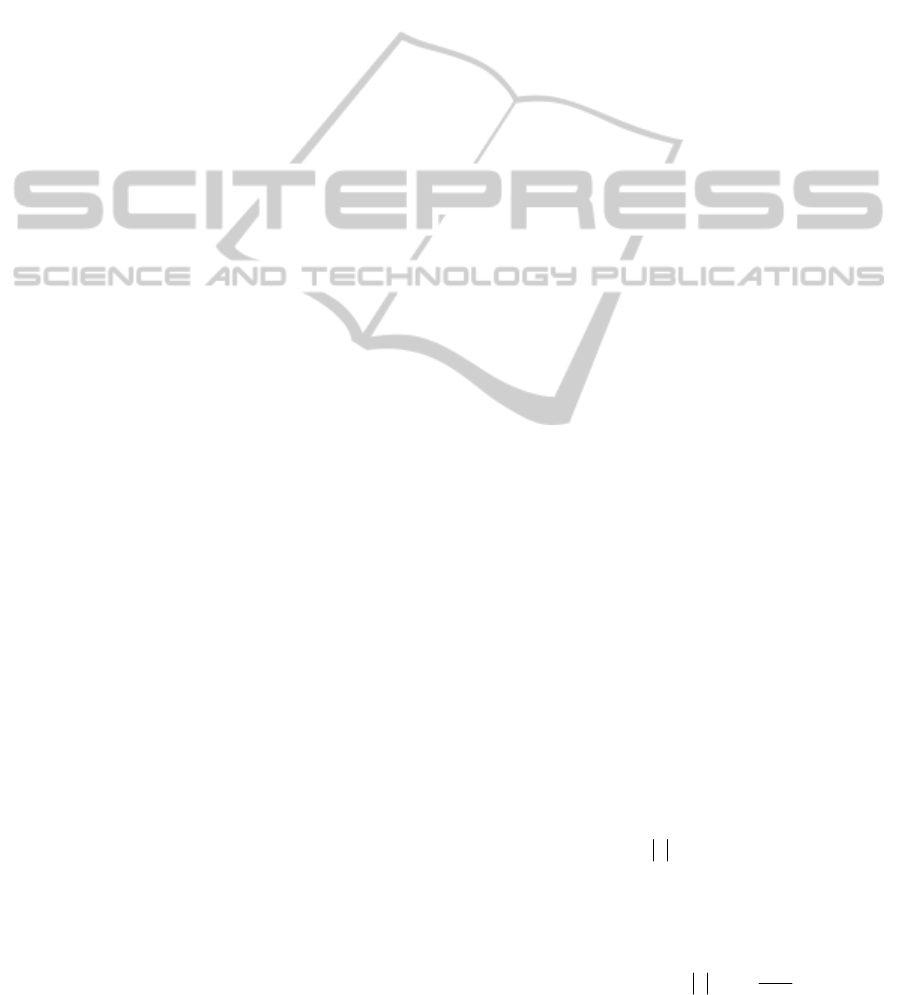
(Altintas, 1992). As a result, for the purpose of
implementation of tool wear monitoring system in
industrial environment, alternative sensing solutions
have to be investigated to strike the balance between
effectiveness and cost. Secondly, feature extraction
plays crucial role in the improvement of accuracy
and robustness of tool wear predictive model since
the original sensory signals usually are interfered
with noise, disturbance and redundant information.
Normally, statistical moments based features, i.e.
mean value, standard deviation, extracted from
sensory signal have been always employed to predict
tool wear. However, this feature extraction
technique is not effective enough to explore the
instinct features associated with tool wear.
Consequently, a more advanced feature extraction
technique is required to filter out the noise
component and reduce the dimensionality of the
original data to improve prediction accuracy.
Finally, neural network has been extensively used to
model the correlation between sensory signals and
tool wear. However, the prediction results were not
satisfied due to some disadvantages, i.e. low
convergence rate, obvious ‘over-fitting’ and
especially poor generalization when few samples are
available. Support Vector Machines (SVM) based on
statistical learning theory is a new achievement in
the field of data-driven modelling and implemented
successfully in classification, regression and
function estimation (Kwok, 1999, Cao and Tay,
2003, Goethals and Pelckmans, 2005). SVM has
been proved less vulnerable to overfitting problem
and higher generalization ability since SVM is
designed to minimize structural risk whereas
previous neural networks techniques, i.e. MLP, are
usually based on minimization of empirical risk
(Kwok, 1999). Consequently, the applicability of
SVM in the tool wear modeling will be explored in
this paper.
The objective of this paper is to develop a new
monitoring approach to predict tool wear using
sensory signals acquired in machining processes.
The organization of the work is as follows. In
Section 2, wavelet transform is explored to extract
features from sensory signals. The SVM is further
introduced to model the correlation between tool
wear and extracted features in Section 3. The
performance of proposed approach is demonstrated
by experimental data acquired from turning
processes in Section 4. The conclusions are given in
last Section.
2 WAVELET TRANSFORM
BASED FEATURE
EXTRACTION
The sensory signals acquired in machining process
are typical non-stationary multi-componential
signals caused by uneven material removing process.
Different tool malfunctions, i.e. tool wear, tool
chipping and tool breakage, may possess different
frequency characteristics in sensory signals. For
instance, the cutting force will increase gradually
with the increase of tool wear and will be obviously
reflected in the lower frequency band or so-called
static component of sensory signals. On the contrary,
tool chipping or breakage will cause cutting force
changed suddenly and may be observed in higher
frequency band or so-called dynamic component of
sensory signals. As a result, the features associated
with different tool malfunctions may be extracted
from either static or dynamic component of sensory
signals. Several techniques, i.e. band-pass filtering,
resample and wavelet transform, may be employed
to decompose sensory signals. From the point of
view of filter design, wavelet transform is a typical
cascade band-pass filter with a varying bandwidth.
The sensory signals can be decomposed into
different frequency bands or scales to capture
localized features i.e. abrupt or gradual changes
within the sensory signals by analysis corresponding
wavelet coefficients. Wavelet transform provides an
efficient way to identify the location and possible
root cause of the malfunction within the machining
processes because of powerful decomposition
ability. Additionally, by implementation wavelet
transform at specified scale, the sensory signal can
be descried as few wavelet coefficients and the
dimensionality of sensory signals can be
dramatically reduced. Hence, in comparison with
other two decomposition techniques, wavelet
transform is more powerful and flexible due to its
multi-resolution capability and hence explored to
obtain static component for feature extractions. The
wavelet transform of signal s(t) is defined as the
inner product in the Hilbert space of L2 norm as
follows (Mallat, 1997):
1/2
*
,
(,) () ()
ab
Cab a st tdt
ψ
+∞
−
−∞
=
∫
(1)
where
)(
*
,
t
ba
is the complex conjugate of
)(
,
t
ba
generated by scaling and shifting from so-called a
‘mother wavelet’ function expressed as
1/ 2
,
() ( )
ab
tb
ta
a
ψψ
−
−
=
(2)
ICINCO 2011 - 8th International Conference on Informatics in Control, Automation and Robotics
480