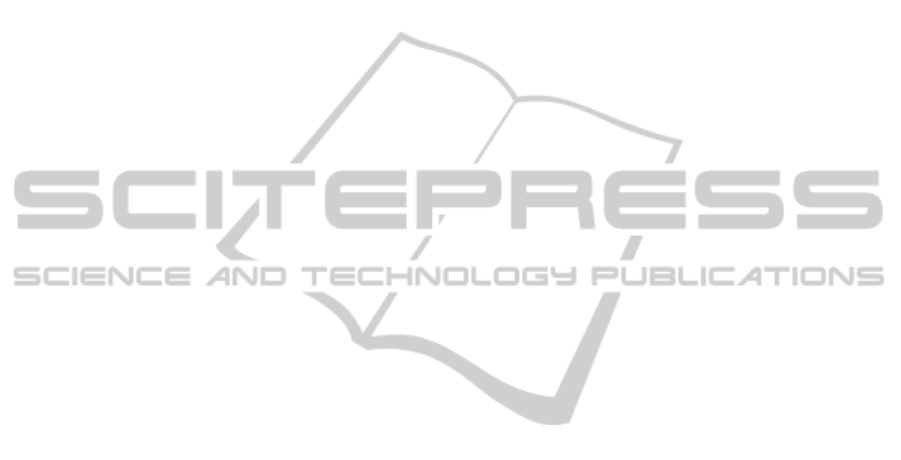
In a delivery project, the deadlines are counted
backwards from the day that the plant should be
operational. The length of work phases are
determined based on time needed for work and
procurement (Cziner, 2006).
The plant engineering process can be divided
into steps e.g. problem analysis, conceptual design,
detailed engineering, and construction (Tuomaala,
2006). More business oriented divisions are also
possible, for example conceptual phase, pre-
feasibility study, feasibility study, investment
decision and implementation (Diesen, 2007).
Although all the phases are equally important for
reaching the goal, the focus in this research is put on
the conceptual design phase, because the
optimization methods researched in this research
project aim to solve problems on conceptual design
level. Other phases of the engineering process are
relevant to our research in that sense that the tools
and methods should be compatible to the proposed
changes.
In the conceptual design phase a very small
amount of information is available and the time and
resources are limited (Seuranen, 2006). Still the
decisions in this phase fix 80% of the total costs of
the project (Douglas, 1988). Decisions in the early
phases of the project are also quality-critical,
because the costs of changes increase tenfold in each
phase (research – process flow – final design –
production) (Bollinger, 1996). In process plant
engineering, the conceptual design phase is led by
process design. All the other engineering disciplines
are more or less in consulting role. For these
reasons, the greatest advantages can be achieved in
early phases of the business process.
Because of the shortened delivery times, the
other engineering disciplines have to begin their
work before the process design is ready. The saving
using concurrent engineering is calculated to be up
to 50% of the calendar time in a delivery project
(Bañares-Alcantara, 2005).
The sub-processes of any process design task are
design task definition, process structure design,
process operation design an design acceptance.
Process structure design and process control design
interact and should therefore be designed
simultaneously (Pajula, 2006). The existing process
design approaches can be divided to heuristic and
engineering experience based methods, optimization
based methods and case-based reasoning methods
(Seuranen, Pajula and Hurme 2001). Case based
reasoning (CBR) has been applied for design of the
pulp process. The main challenge in CBR is the need
of extensive database to provide the required
knowledge (Pajula, 2006). Outsourcing of the design
work is a common practice nowadays. Fathianathan
and Panchal (2009) have proposed a model to
support outsourcing decisions.
2.2 Optimization in Process Design
Current work practices in forest industry process
engineering are almost solely based on engineering
experience. Simulation and optimization is used in
the design of unit processes, but less in the design of
the process as whole. Plant wide simulation enables
the validation of process structure and control
concepts even before selecting suppliers and
therefore it reduces risks (Ylén, et al, 2005) and
gives a deeper understanding of the process
(Pulkkinen, Ihalainen and Ritala, 2003). According
to the interviews, plant wide simulation is more
useful when building a plant with totally new
concepts when the “rules of thumb” are not
available.
For combining the optimization of plant
structure and plant control, there are several options.
Optimization strategy can be sequential, iterative, bi-
level or simultaneous. (Fathy, Reyer, Papalambros
and Ulsoy, 2001).
Bi-level optimization has been under an active
research lately (Dempe, 2002). Still only a few
research is dealing with multi-objective bilevel
problems. Eichfelder (2010) presents an algorithm
for solving bilevel multi-objective problems. The
combination of dynamic simulator model and
dynamic optimization has been researched for
papermaking process (Linnala, et al, 2011).
2.3 Information Systems for Process
Design
The variety of the Computer Aided Engineering
(CAE) tools supporting process systems engineering
(PSE) is enormous. One of the interviewed
engineering enterprises is using over 50 different
engineering tools. A trend, as seen in modern
integrated process engineering tools, is the
transformation from document-centric design to
data-centric design, realized with database
technology (Comos, 2011),(Smart Plant, 2011),
(Bentley, 2011). Major tool vendors have developed,
acquired and integrated engineering tools from other
engineering disciplines under unified product
families. Modern process engineering support
systems combine modeling and information
management features for engineering of many
aspects of plant engineering, e.g. process, piping,
DESIGN PROCESS MODEL FOR OPTIMIZING DESIGN OF CONTINUOUS PRODUCTION PROCESSES
493