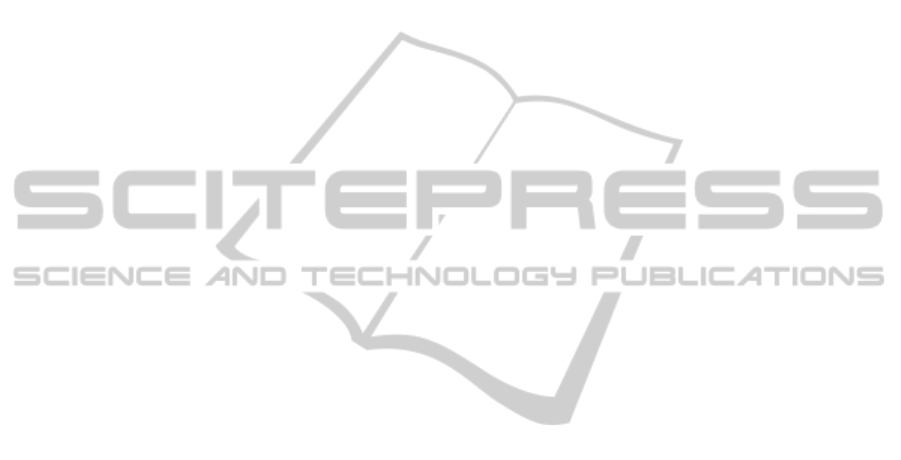
ACKNOWLEDGEMENTS
The work in this paper was performed within the
project “Integrated Control of Robotic Systems in
Complex Environments” that was supported by a
grant from the Croatian Ministry of Science,
Education and Sports.
REFERENCES
Biagiotti, L., Melchiorri, C., 2008. Trajectory Planning for
Automatic Machines and Robots, Springer-Verlag
Berlin Heidelberg.
Kyriakopoulos, K. J., Saridis, G. N., 1988. Minimum jerk
path generation, In Proceedings of the IEEE
International Conference on Robotics and
Automation, 364–369.
Macfarlane, S., Croft, E. A., 2003. Jerk-Bounded
Manipulator Trajectory Planning: Design for Real-
Time Applications, In IEEE Transactions on Robotics
and Automation, Vol.19, No. 1, 42-52.
Li, H., Ceglarek, D., 2002. Optimal Trajectory Planning
for Material Handling of Compliant Sheet Metal Parts,
In ASME Journal of Mechanical Design, Vol. 124,
213-222.
Ho, C. Y., Cook, C.C., 1982. The application of spline
functions to trajectory generation for computer
controlled manipulators, In Digital Systems for
Industrial Automation, 1 (4): 325-333.
Ranky, P.G., Ho, C.Y., 1985. Robot Modelling – Control
and Applications with Software, Springer-Verlag, IFS
(Publications) Ltd, UK.
Kovacic, Z., Bogdan, S., Petrinec, K., Reichenbach, T.,
Puncec, M., 2001. Leonardo - The Off-line
Programming Tool for Robotized Plants, In CD-ROM
Proceedings of the 9th Mediterranean Conference on
Control and Automation, Dubrovnik, Croatia.
Petrinec, K., Kovacic, Z., 2005. The application of spline
functions and Bézier curves to AGV path planning, In
CD-ROM Proceedings of the IEEE International
Symposium on Industrial Electronics ISIE 2005,
Dubrovnik, Croatia.
Petrinec, K., Kovacic, Z., 2007. Trajectory planning
algorithm based on the continuity of jerk, In
Proceedings of the 15th Mediterranean Conference on
Control and Automation, Athens, Greece, T30-041.
Yakimenko, O. A., 2006. Direct Method for Real-Time
Prototyping of Optimal Control, In Proceedings of the
International Control Conference, Glasgow, Scotland.
Bevilacqua, R., Yakimenko, O., Romano, M., 2006. On-
Line Generation of Quasi-Optimal Docking
Trajectories, In Proceedings of the 7th International
Conference on Dynamics and Control of Systems and
Structures in Space (DCSSS), Greenwich, London,
England.
Kaminer, I., Yakimenko, O., Pascoal, A., Ghabcheloo, R.,
2006. Path Generation, Path Following and
Coordinated Control for Time-Critical Missions of
Multiple UAVs, In American Control Conference,
4906–4913.
Taylor, R. H., 1979. Planning and execution of straight
line manipulator trajectories, In IBM J. Research and
Development, Vol. 23, 424-436.
CONTINUOUS JERK TRAJECTORY PLANNING ALGORITHMS
489