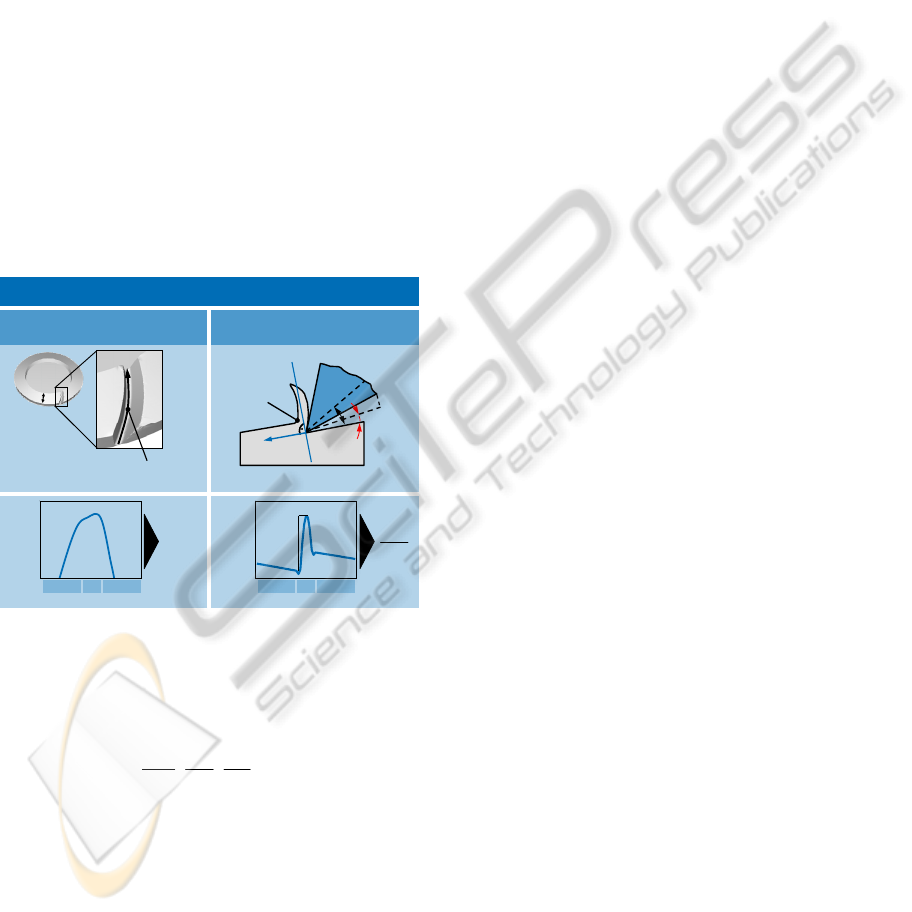
wear behaviour. Hence, the gradient should have a
minimum value.
Besides the aspect of chip compression and the
so caused tool load further characteristic values for
analysing the cutting process can be used. The entire
working length l
e
describes the contact length, which
the cutter is in contact with the workpiece under
consideration of the working direction, see figure 10.
So the working length is an approach for the
description of the thermal and mechanical load on
the cutting edge. A higher working length results in
a higher temperature respectively friction and thus in
higher loads on the cutting edge.
Additionally the working relief angle α
e
can be
used for the analysis of the tool load. The working
relief angle influences the thermal stress on the
cutting edge. Thus the gradient Δα
e
/Δl
s
is a useful
characteristic value for the alternating thermal stress
along the cutting edge. The higher the gradient the
higher the alternating thermal stresses on the relief
face of the cutter. Hence, a minimum value of the
gradient is desirable.
Characteristic Values
Working Length l
e
Gradient Working Relief Angle
Δα
e
/Δl
s
tool
-α
e
entire
workinglengthl
e
+α
e
workpiece
chip
Δα
e
working relief angle
Δα
e
s
e
l
Δ
Δ
b
Δl
s
el
OB IBTOB IBT OB OBTOB OBT
cutting edge length l
s
cuttin edge length l
s
el
Figure 10: Working length and gradient of relief angle.
In order to integrate the presented characteristic
values in only one value the new characteristic value
K
G
is introduced:
cu e e
Ge
sss
h Δα Δγ
Kl
lll
Δ
=⋅ ⋅ ⋅
ΔΔΔ
(3)
A high K
G
value results in a higher tool load and
thus in higher tool wear. With the new characteristic
value K
G
a first qualitative comparison of different
processes and so of the tool wear is possible. From
this an optimization of the process is feasible and a
first approach for a qualitative tool wear prediction
model is realised.
In the future the characteristic value with the tool
wear model has to be modified by weighting in order
to enable a quantitative evaluation and prediction of
the tool wear.
4 TOOL WEAR ANALYSIS
Bevel gear drives consists of a pinion and a ring
gear. The pinion is positioned at the input driving
side and the ring gear at the output side of the rear
axle drive train. In general both parts are
manufactured in a process using cutter heads which
are equipped with stick-type blades. Here the face-
milling process, as described by Klingelnberg
(2008), is used for manufacturing. The plunging
process is mostly used for the manufacturing of the
ring gear whereas the generating process is used for
pinion manufacturing.
Following different case-studies regarding tool
wear of stick type blades in industrial application
will be presented. Here the tool wear behaviour in
plunging and generating process with different tool
concepts is compared to the new characteristic value
K
G
. In this report the focus is on the discontinuous
face milling process with tungsten carbide tools in
dry cutting.
4.1 Tool Wear Analysis of Plunging
Process
In figure 11 the tool wear of two full profile blades
are presented. They are used for plunging process 1
and 2 for ring gear manufacturing. In process 1 a
cutting velocity of v
c
= 200 m/min and a feed ramp
of f
BG
= 0.15 – 0.06 mm per blade group was used.
The cutter head with an outer diameter
D
a
= 231 mm. was equipped with 7 carbide tools.
The characteristic value K
G
was displayed in the
diagram over the unrolled cutting edge length l
s
which is separated into the outside blade (OB), the
tip area (T) and the inside blade (IB). The maximum
tool wear occures at the corner radius of the outside
blade (OB) to the tip area (T). In the simulation the
characteristic value K
G
has its maximum at the same
tool area. Additional tool wear occurs at the corner
radius of the inside blade (IB) and the tip area (T). In
this area the tool wear is less than at the other corner
radius. The same tendencies are calculated in the
simulation. Thus, the correlation of the calculated
value K
G
and the real tool wear is good. On the one
hand the maximum tool wear can be located by K
G
,
on the other hand the lower tool wear at the inside
blade can also be calculated.
In process 2, see figure 11 right, a cutting
velocity of v
c
= 150 m/min and a feed ramp of
f
BG
= 0.16 – 0.10 mm per blade group was chosen.
MANUFACTURING SIMULATION OF BEVEL GEAR CUTTING - Simulation based Approach for Tool Wear Analysis
517