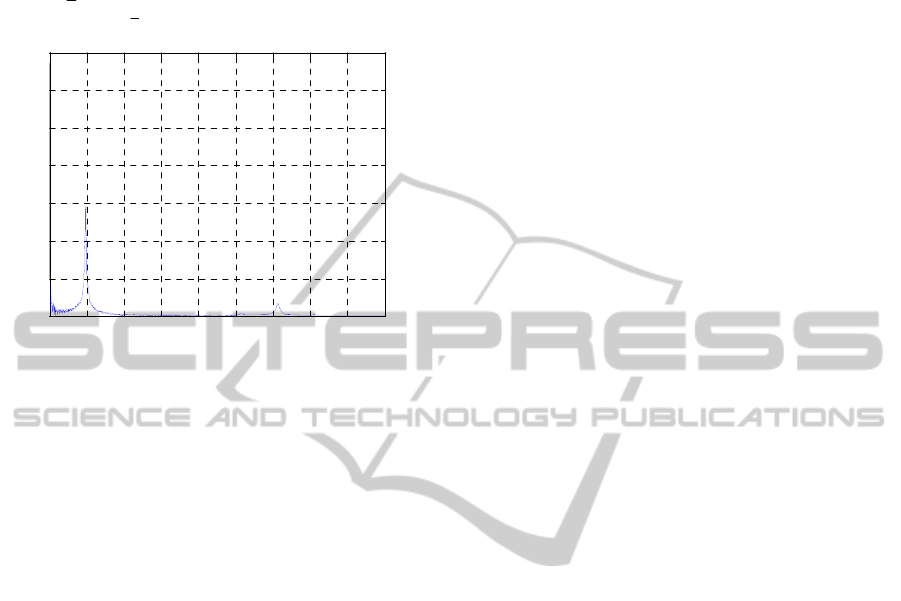
of the LQR design (with open loop matrix
LQR
L
).
Moreover, standard statements similar to those
already enunciated can be added: a) for perturbation
rejection
()σ
LQG
L
is to be designed large and b) for
noise attenuation
()σ
LQG
L
is to be designed small.
0 5 10 15 20 25 30 35 40 45
0
0.01
0.02
0.03
0.04
0.05
0.06
0.07
Frequency (Hz)
|Y(f)|
Figure 5: Results on cantilever plate process identification.
5 EXPERIMENTAL RESULTS ON
AN ELEMENTARY SMART
STRUCTURE
To test the proposed smart structures control
strategies,
a 200×500×1.25 mm cantilever aluminum
plate (Figures 1, 2) is considered. The test rig
contains 1) the cantilever aluminum plate on which
the strain gages (SGD-5/350-LY11, Omega
Engineering) and MFC (M8557P1MFC, Smart
Materials) actuators are bonded, 2) the signal
conditioners (OM5-WBS-3-C, Omega Engineering)
for converting strain gages bridge signals to high
level and for bridge supply, 3) the high voltage
amplifiers (PA05039,-500 V÷ +1500V) for the MFC
actuators supply, 4) a PC on which the control laws
are implemented and 5) an acquisition card (NI
PCIe-6259) used for processing the signals from
conditioners and for applying to the MFC actuator
the control signal, amplified by the high voltage
amplifiers.
The values of the matrices
122
A, B , B ,C
were
obtained by ANSYS analysis combined with
analytic considerations based on the setup of the
measured and regulated outputs. We note here that
only one of the strain gages bonded on specimen
was operational during the tests thus limiting the
experiments to a single-output case. The first five
natural frequencies of the plate identified from the
FE model are 5.66 Hz, 25.23 Hz, 33.95 Hz, 81.03
Hz, 95.05 Hz. Only a small modal damping factor of
1% of the critical damping was applied to the model.
The experimental frequencies identified with the
setup described are 5 Hz, 26 Hz, 31 Hz, 157 Hz.
Figure 5 shows the results of a simple process
identification procedure based on impulse type
perturbation. There is an acceptable match of the
first three frequencies between the model and the
measured ones. However, this does not apply for the
higher modes, with only the mode at 157 Hz being
detected by the strain gages. Consequently, only first
three modes will be taken into account in the matrix
1
C . Figure 6 presents all the system matrices
defined in (12), (13) both with the “static” weights.
The consistency of the first three modes in process is
attested by Figure 7. The frequency responses of the
weighting filters (16) are shown in Figure 8. In
choosing the dynamic weights, it is to mention the
continuity with the static weights
12 3
ηη η
k = 322, k = 39.3, k = 1.0881
−−
1
2
3
ω =35.6091 rad/s
ω =158.5449 rad/s
ω =213.3373 rad/s
123
2kkk===
14
23
aa
aa
ω =18.85 rad/s, ω =1885 rad/s
ω =25.13 rad/s, 0.5, ω =219.9 rad/s
act
k =
The steps of
control synthesis, described in
Sections 3.1 and 3.2, have been validated by
numerical simulations and experiments (see Figures
9, 10). A notable vibration attenuation of 17.4 dB is
experimentally reached (Figure 10). For the sake of
comparison, we cite the result 15.6 dB in (Yaman et
al., 2002). The simulation result predicts a
somewhat better performance, with a value of 26 dB
for the attenuation (Figure 9). The attenuation values
in the case of dynamic weights are similar. The
better attenuation predicted by the model is
explained primarily by the very small value of
damping introduced in the model, very likely
significantly smaller than the true damping value.
This essentially leads to an over-prediction of the
vibration amplitudes in the simulations.
Additionally, the actuator efficiency in the model is
considered to be ideal. A perfect actuator bonding to
the plate base structure was assumed, without any
modeling of the adhesive bond-line effects. Also, the
actuator electro-mechanic behavior was assumed to
be linear, without accounting for any hysteretic or
other nonlinear effects. Finally, we note that the
controller is derived for the numerical model, and
ACTIVE ROBUST CONTROL OF A SMART PLATE
495