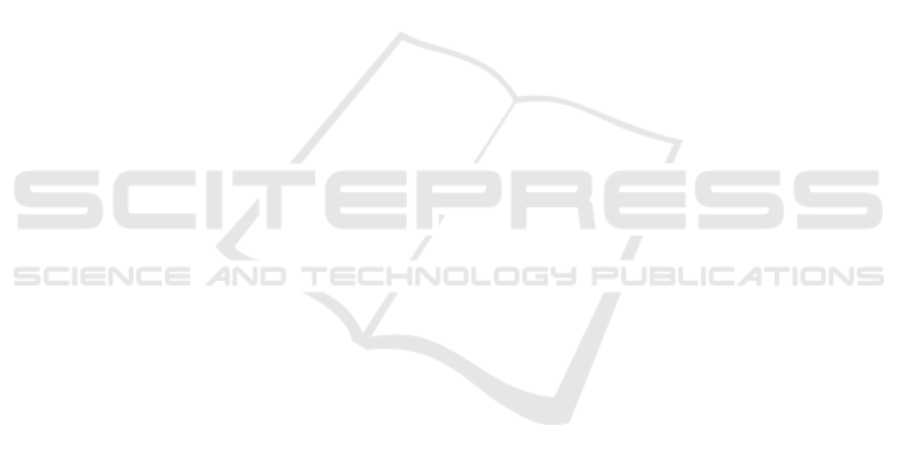
SCENE TRANSITION NETS SIMULATOR FOR MULTI-ASPECT
MODELING OF DISCRETE-CONTINUOUS HYBRID SYSTEMS
Takeshi Tateyama
1
, Seiichi Kawata
2
, Yoshiki Shimomura
1
, Kentaro Watanabe
1
and Ryosuke Chiba
1
1
Graduate School of System Design, Tokyo Metropolitan University, Asahigaoka 6-6, Hino-shi, Tokyo, Japan
2
Advanced Institute of Industrial Technology, Higashi-Ohi 1-10-40, Shinagawa-ku, Tokyo, Japan
Keywords:
Discrete-continuous hybrid systems, Simulation, scene transition nets (STNs), Manufacturing systems,
Multi-aspect modeling.
Abstract:
Scene Transition Nets (STN) are graphical modeling tools and simulators for discrete-continuous hybrid sys-
tems. Designers have previously built complex STN models of large-scale systems on the basis of a single
aspect. However, many large-scale systems consist of several sub-systems designed for different purposes and
based on different aspects. In addition, these subsystems are complexly intertwined with each one another.
For verifying the behavior of such complex systems in simulations, it is necessary to construct multiple STN
models of the subsystems, integrate them by taking into account the relationships among the subsystems, and
simulate them in parallel. Kawata has proposed ”multi-aspect modelingh using STNs in order to realize above-
mentioned modeling concepts. However, the interaction of the sub-STN models with other models is difficult
according to the basic STN concepts. This shortcoming interferes with the practical implementation of multi-
aspect modeling. The authors overcome this shortcoming by enabling the sharing of the state variables of the
actors (actors correspond to tokens in Petri nets). Called ”actor-link”, the simple concept enables to construct
complex layered and parallel structures of STNs and perform multi-aspect modeling. The experimental results
for the modeling and simulation of certain complex industrial systems demonstrate the effectiveness of the
proposed method and simulation tool.
1 INTRODUCTION
Simulation is an effective technique for verifying the
behavior of complex systems such as manufacturing
systems and chemical plant systems. However, many
complex industrial systems are actually combinations
of both continuous systems and discrete-event sys-
tems and are called ghybrid systems.h Hence, it is
difficult to model and simulate such systems by us-
ing only the modeling methods applicable to contin-
uous systems (e.g., differential equations) or those
used discrete-event systems (e.g., Petri nets(Murata,
1989)). Kawata et al. have proposed scene transi-
tion nets (STNs)(Kawata et al., 1994a)(Kawata et al.,
1994b) as graphical modeling and simulation tools for
discrete-continuous hybrid systems. Although STNs
are based on the concept of Petri nets, in STNs, de-
signers construct models of continuous systems us-
ing differential equations and then embed them into
discrete-event system models. By using STNs, de-
signers can easily construct models of hybrid sys-
tems and conduct simulations. STN programming re-
quires STN designers to possess considerable object-
oriented programming skills and excellent knowl-
edge. In our study, we aim to develop an gSTN graph-
ical user interface (GUI) simulator(Tateyama et al.,
)(Tateyama et al., 2010)h that will enable designers to
easily and graphically edit and simulate STN models.
System designers have previously built complex
STN models of large-scale systems on the basis of
a single aspect. However, many large-scale systems
consist of several subsystems designed for different
purposes and based on different aspects. In addition,
these subsystems are complexly intertwined with one
another. For verifying the behavior of such complex
systems in simulations, it is necessary to construct
multiple models of the subsystems, integrate them
by taking into account the relationships among the
subsystems, and simulate them in parallel. Kawata
et al. have proposed ”multi-aspect modelingh using
STNs(Kawada et al., 1996) in order to realize the
abovementioned modeling concepts. In this model-
ing method, it is necessary to create models of inter-
actions among submodels. However, an actor can be
467
Tateyama T., Kawata S., Shimomura Y., Watanabe K. and Chiba R..
SCENE TRANSITION NETS SIMULATOR FOR MULTI-ASPECT MODELING OF DISCRETE-CONTINUOUS HYBRID SYSTEMS.
DOI: 10.5220/0003650104670475
In Proceedings of the 8th International Conference on Informatics in Control, Automation and Robotics (MSIE-2011), pages 467-475
ISBN: 978-989-8425-75-1
Copyright
c
2011 SCITEPRESS (Science and Technology Publications, Lda.)