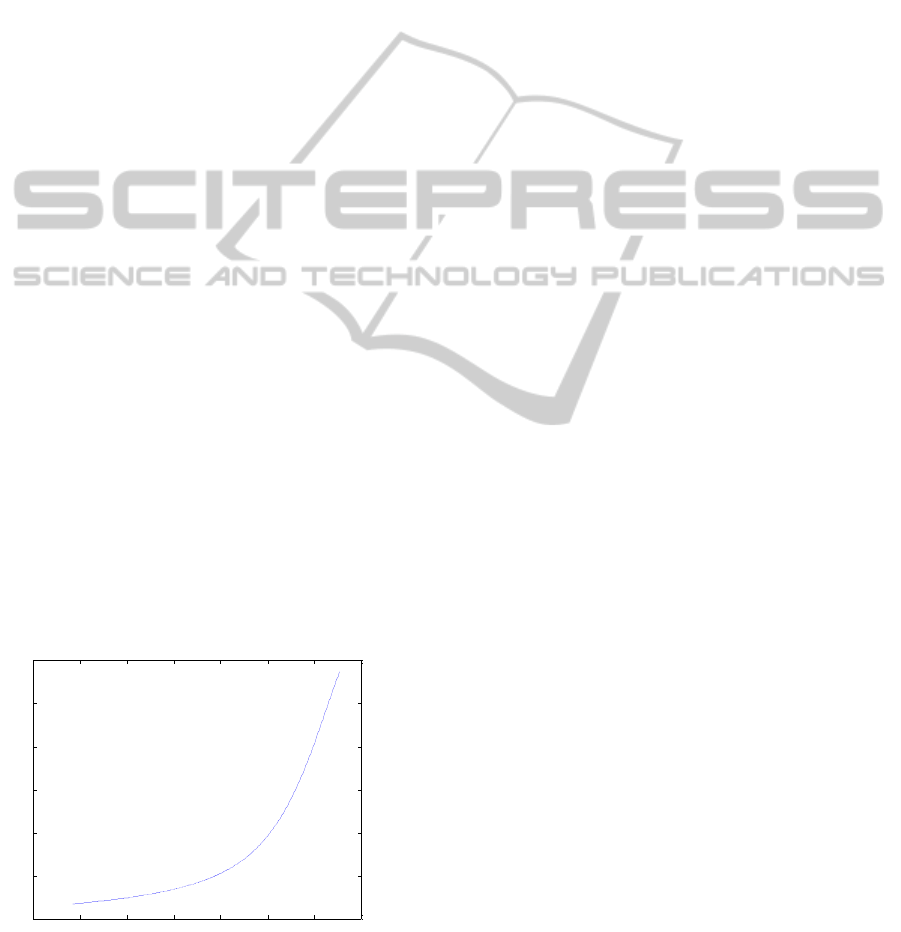
The sensitivity changes, due to the non-linearity.
If it changes considerably with only small changes
in the component, then this suggests that the
component significantly affects the viscosity.
Figure 4 shows the sensitivity curve when a
variables is perturbed. Above 0.035Moles, there is
an increase in viscosity, highlighting that variable
has a big effect on viscosity.
5 CONCLUSIONS
This paper has used a well proven technique,
multilayer feed forward neural networks, to predict
the viscosity over a range of temperatures and
different glass compositions. The prediction error
(MSE) of the model for this range of feed was found
to be 1.84x10
-4
for the scaled validation data set
which highlights the model’s accuracy at predicting
viscosity.
The model is only valid over a certain range for
each variable, but in future work the model will be
adapted for further different compositions and feeds.
The work carried out so far has provided
encouraging predictions for a larger range of
compositions. This will be developed into a user tool
for a greater understanding of how the composition
will affect the viscosity.
ACKNOWLEDGEMENTS
The author would like to thank Northern way and
Technology Strategy Board for part funding the
Knowledge Transfer Partnership. The author would
also like to thank Barbara Dunnett, National Nuclear
Laboratory for the initial guidance on this study.
0.01 0.015 0.02 0.025 0.03 0.035 0.04 0.045
0
1
2
3
4
5
6
Figure 4: Sensitivity graph for variable 25.
REFERENCES
Bhat, N. V. and T. J. McAvoy (1990) “Use of neural nets
for dynamical modelling and control of chemical
process systems”, Computers & Chemical
Engineering, 14, 573-583.
Bishop, C. (1995) Neural Networks for Pattern
Recognition. Oxford University Press: Oxford.
Bulsari, A. B., (Ed), (1995) Computer-Aided Chemical
Engineering, Vol.6, Neural Networks for Chemical
Engineers, Elsevier: Amsterdam.
Cybenko, G. (1989) “Approximation by superposition of a
sigmoidal function”, Math. Control Signal Systems, 2,
303-314.
Duchesne, M. A., Macchi, A., Lu, D.Y., Hughes, R. W.,
McCalden, D., J. Anthony, E. J., (2010) Artificial
neural network model to predict slag viscosity over a
broad range of temperatures and slag compositions -
Fuel Processing Technology, Volume 91, Issue 8,
Pages 831-836
Girosi, F. and T. Poggio (1990) “Networks and the best
approximation property”, Biological Cybernetics, 63,
169-179.
Lennox, B., Rutherford, P., Montague, G. A., Haughin, C.,
(1998) Case study investigating the application of
neural networks for process modelling and condition
monitoring – Computers & Chemical Enginerring,
Volume 22, Issue 11, Pages 1573-1579
Marquardt, D. (1963) “An algorithm for least squares
estimation of nonlinear parameters”, SIAM J. Appl.
Math., 11, 431-441.
Montgomery, D. C., Peck, E. A., Vining, G. G.,
Introduction to Linear Regression Analysis, Wiley
Series in Probability and Statistics
Narendra, K. S. and K., Parthasarathy (1990)
“Identification and control of dynamical systems using
neural networks”, IEEE Transactions on Neural
Networks, 1, 4-27.
Park, J. and I. W. Sandberg (1991) “Universal
approximation using radial basis function networks”,
Neural Computation, 3, 246-257.
Pham, D. T., Liu, X., (1995) Neural Networks for
Identification, Prediction and Control. Springer-Verlag
London Limited. 4th edition
Rumelhart, D. E., G. E. Hinton, and R. J. Williams,
“Learning internal representations by error
propagation”, in Parallel Distributed Processing,
(Eds) D. E. Rumelhart and J. L. McClelland, MIT
Press, 1986.
Steele, C. J., Dunnet, B., Riley, A. D., Ferguson, K.,
Gribble, N., Short, R., (2011) Viscosity of simulated
nuclear waste vitrified product International
Conference on the Chemistry of Glasses and Glass-
Forming Melts, To be published
Zhang, J., Morris, A. J., Martin, E. B., Kiparissides, C.,
(1998) Prediction of polymer quality in batch
polymerisation reactors using robust neural networks
Chemical Engineering Journal 69, Pages 135-143
MODELLING VITRIFIED GLASS VISCOSITY IN A NUCLEAR FUEL REPROCESSING PLANT USING NEURAL
NETWORKS
325