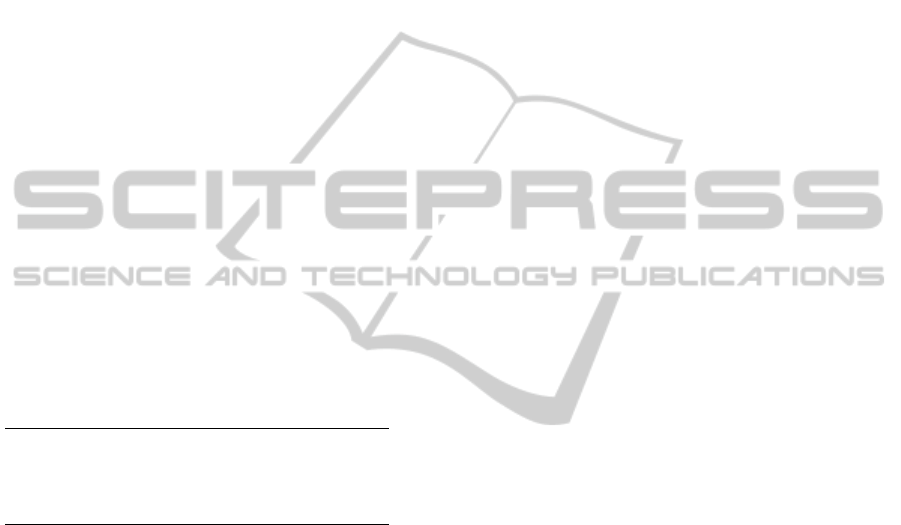
4 RESULTS
The PLES run 20-times for each problem. The exper-
iments were done on 2.2GHz computer, and each run
took approximately 5 minutes for production plan-
ning, and less than 1 minute for cooling appliance
optimization. However, time complexity was not the
subject of this evaluation.
4.1 Production Plan
The PLES algorithm was tested on two different real
order lists from production company. The Task 1 con-
sists of n = 711 orders for 251 products, while the
Task 2 consists of n = 737 orders for 262 products. In
both tasks m = 5 production lines are available. The
number of evaluations was limited to 500, 000.
While the PLES does not need any parameter,
the comparing GA used the following parameters:
the population size N = 100; the number of gener-
ations was 5, 000; the replacement rate r = 0.2; the
crossover probability p
c
= 0.7; the mutation proba-
bility p
m
= 0.005.
In Table 1 best, mean, worst, and standard devia-
tions of solutions are presented for each task.
Table 1: Results of optimization for Task 1 and Task 2
PLES GA
Task 1 Best 1.309×10
8
1.308×10
8
Mean 1.327 ×10
8
1.340×10
8
Worst 1.416×10
8
1.610×10
8
StD 3.230 ×10
6
6.526×10
6
Task 2 Best 1.576×10
8
1.611×10
8
Mean 1.664 ×10
8
1.748×10
8
Worst 1.813×10
8
1.914×10
8
StD 7.390 ×10
6
7.235×10
6
When comparing with the previous approach of
production planning (Koroˇsec et al., 2010), the ex-
pert’s manual plan for those two tasks had about four-
times more delayed orders. This is significantly worse
than results obtained by both of the algorithms. Any-
way, the PLES algorithm shows faster convergence
and proves its search ability to find the solution with-
out the predefined control parameter settings.
4.2 Cooling Appliance
The PLES algorithm was used to speed-up the devel-
opment process of a new type of a cooling appliance.
The PLES was able to find the optimal set of cooling
appliance control parameters setting in all runs.
Optimization based on stochastic search method,
might give several possible solutions. Criteria for
choosing the appropriate one is not only the smallest
energy consumption and the desired temperature, but
it is also necessary to verify the behavior of the com-
ponents. Namely, frequent on/off switching of them
shortens their life cycle.
5 CONCLUSIONS
The paper presented an adaptive parameter-less evo-
lutionary search for combinatorial problems. The ef-
ficiency of the proposed parameter-less algorithm was
evaluated by two real-world industrial optimization
problems. Following the previously presented numer-
ical results, it was shown, that the combinatorial im-
plementation of the algorithm had faster convergence
than comparing algorithm and also it proved its search
ability to find the solution without the predefined con-
trol parameters. Furthermore, it was shown that the
combinatorial implementation of the algorithm is as
effective as the numerical one.
REFERENCES
Angeli, D. and Kountouriotis, P.-A. (2011). A stochastic
approach to ”dynamic-demand” refrigerator control.
Control Systems Technology, IEEE Transactions on,
PP(99):1 –12.
B¨ack, T. (1992). The interaction of mutation rate, selec-
tion, and self-adaptation within a genetic algorithm.
In M¨anner, R. and Manderick, B., editors, Proceed-
ings of the 2nd Conference on Parallel Problem Solv-
ing from Nature. North-Holland, Amsterdam.
Eiben, A., Michalewicz, Z., Schoenauer, M., and Smith, J.
(2007). Parameter control in evolutionary algorithms.
In Lobo, F., Lima, C., and Michalewicz, Z., edi-
tors, Parameter Setting in Evolutionary Algorithms,
volume 54 of Studies in Computational Intelligence,
pages 19–46. Springer Berlin / Heidelberg.
Kang, Q., Wang, L., and di Wu, Q. (2006). Research on
fuzzy adaptive optimization strategy of particle swarm
algorithm. International Journal of Information Tech-
nology, 12(3):65–77.
Koroˇsec, P., Papa, G., and Vukaˇsinovi´c, V. (2010). Appli-
cation of memetic algorithm in production planning.
In Proc. Bioinspired Optimization Methods and their
Applications, BIOMA 2010, pages 163–175.
Papa, G. (2008). Parameter-less evolutionary search. In
GECCO, pages 1133–1134.
Papa, G. and Mrak, P. (2010). Optimization of cooling ap-
pliance control parameters. In Proceedings of the 2nd
International Conference on Engineering Optimiza-
tion, EngOpt2010.
Stephens, C. R., Olmedo, I. G., Vargas, J. M., and Wael-
broeck, H. (1998). Self-adaptation in evolving sys-
tems. Artif. Life, 4:183–201.
ECTA 2011 - International Conference on Evolutionary Computation Theory and Applications
310