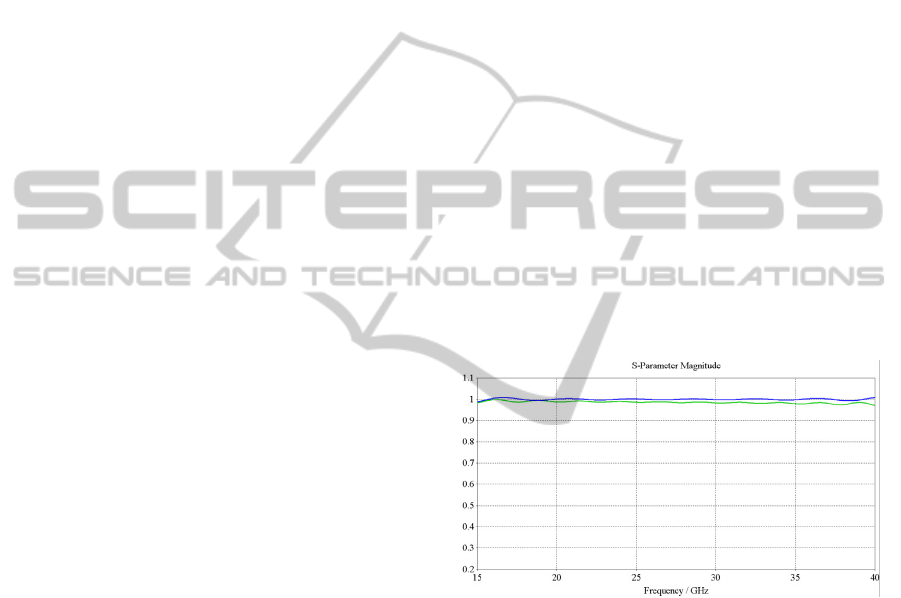
F
2
(x) = [ S
21
ref
– S
21
o
(x)]
-1/2
(2)
Here, S
11,ref
is the computed value of the reflection
coefficient of the realistic model of the composite
material at the frequency range. Then, S
11,opt
(x) is the
reflection coefficient of the equivalent homogeneous
material computed in COMSOL Multiphysics for
the vector of state variables x = [
r
, tan
].
Similarly, S
21,ref
is the computed transmission
coefficient of the realistic model of the composite
material, S
21,opt
(x) is the transmission coefficient of
the equivalent homogeneous material computed in
COMSOLl Multiphysics for the state vector x = [
r
,
tan
]
T
.
The equivalent material was searched for one
particular composite material using two different
optimization approaches – a singleobjective and a
multiobjective. For the single-objective solution, the
fitness functions (1) and (2) are weighted by
weighting coefficients w
1
= 1 and w
2
= 1 and
summed:
F(x) = w
1
F
1
(x) + w
2
F
2
(x) (3)
4.1 Single-objective Optimization
For single-objective optimization a classical global
optimization representative – a genetic algorithm –
was selected. Genetic Algorithms (GA) are members
of stochastic global optimization methods and are
based on the Darwinian Theory of the evolution of
species. The values of the control parameters were
chosen according to recommendations published in
(Rahmat-Samii and Michielssen, 1999).
The population consisted of 50 individuals, the
accuracy of binary coding was set to 0.001. Indivi-
duals for the next population were selected by the
tournament operator. Probability of the multi-point
crossover was set to 70 % and probability of the
multi-point mutation was set to 6 %. The elitist
strategy was applied. The optimization was set to
minimize the optimized problem.
Time needed for a single simulation run and then
calculation of the complex permittivity value using
single-objective genetic algorithm was
approximately 12 hours (see Table 1). Because of
time needed for the calculation of the criteria
function, the entire optimization cycle was repeated
only one hundred times.
The values of complex permittivity obtained
from the optimization run were then set to 3D model
to compare the reflection parameters with the model
of the original composite. The error of calculation
was at maximum 0.45% on the whole frequency
range of 15-40 GHz.
In Table 1 one chosen value of complex
permittivity from the set of the optimization run is
shown. On Figure 4, the scattering parameters for
this value of the complex permittivity of the
homogeneous replacement are shown in comparison
with scattering parameters of the original composite.
As it can be seen on Figure 4 good match was
achieved.
4.2 Multi-objective Optimization
Niched-Pareto Genetic Algorithms, by Horn et al., is
a multi-objective GA based on the non-domination
concept. NPGA uses the binary tournament selection
(Deb, 2001).
The population consisted of 50 individuals,
mutation probability was set to 6%, the crossover
probability was 70% and the selected accuracy of
coding is 0.001.
The result of a single optimization run is formed
by a set of results corresponding to all the criterions
(Pareto front). The calculation needed to evaluate
one Pareto front was about half of the time needed
for single-objective optimization (see Table 1), the
optimization run was repeated hundred times.
Figure 4: Reflection coefficients of replacements achieved
by single-objective genetic algorithms (blue) in
comparison with the detailed 3D composite model (green).
After an inverse implementation of the values of
complex permittivity of replacements from all
simulation runs to the 3D model, all the optimized
results were simulated to do the comparison with the
original composite material results.
In Table 1 it is shown, that maximal error of the
replacement on frequency range 15 – 40 GHz is less
then 0.45 %.
On Figure 5 a single choice value of the complex
permittivity of the replacement compared with
reflection coefficient of the original composite
material is shown.
FINDING THE ELECTROMAGNETIC HOMOGENOUS EQUIVALENT OF THE COMPOSITE MATERIAL USING
GLOBAL OPTIMIZATION TECHNIQUES TO SOLVE THE INVERSE PROBLEM
327