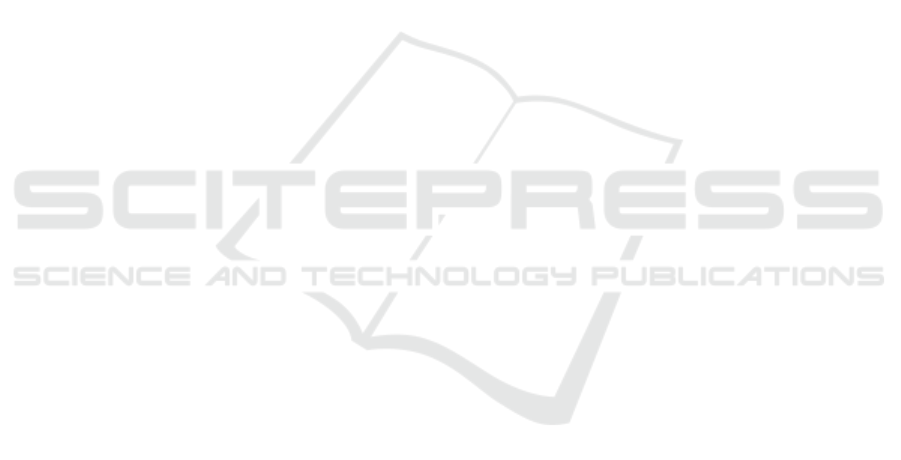
ECONOMIC DESIGN OF MEWMA VSSI CONTROL CHARTS
FOR MULTIATTRIBUTE PROCESSES
Seyed Taghi Akhavan Niaki
1
and Paravaneh Jahani
2
1
Sharif University of Technology, P.O. Box 11155-9414 Azadi Ave., Tehran 1458889694, Iran
2
Department of Industrial Engineering, Sharif University of Technology, Tehran, Iran
Keywords: Multiattribute processes, Economic design, Multivariate exponentially weighted moving average chart,
Variable Sample Size, Variable Sampling Interval, Genetic Algorithm.
Abstract: In this research, a new methodology is developed to economically design a multivariate exponentially
weighted moving average (MEWMA) control chart for multiattribute processes. The optimum design
parameters of the chart, i.e., the sample size, the sampling interval, and the warning/action limit coefficients,
are obtained using a genetic algorithm to minimize the expected total cost per hour. A sensitivity analysis
has also been carried out to investigate the effects of the cost and model parameters on the solutions
obtained.
1 INTRODUCTION
In many real-world manufacturing environments the
quality of products are of multiattribute type, where
multiattribute control charting methods are
recommended to deal with the existing correlations
between the attributes. Although there are many
applications for multiattribute control charts in
industries and service sectors, there exists only a
little research on this type of control chart in the
literature. To name a few, Jolayemi (2000) proposed
a multiattribute control chart based on both the J-
approximation and the Gibra’s model to monitor
processes following multivariate binomial
distribution in which there were multiple assignable
causes. In a more recent research in this area, Niaki
and Abbasi (2008) introduced a new method to
monitor multiattribute processes and developed a
multi-attribute C control chart, where a
transformation was first proposed to eliminate the
correlation between the attributes, and then the
symmetric control limits were found.
In the designing process of a control chart, three
parameters are involved; the sample size, the
sampling interval, and the control limit coefficient.
Economic and/or statistical designs are the two
common practices in this regards. In a statistical
design, the design parameters are determined based
on the statistical performances of the chart. These
performances are measured either in terms of type-I
and II errors or in terms of average run lengths
(ARL) or average time to signal (ATS). Meanwhile,
in an economic design, the design parameters are
selected based on minimizing a cost model or a loss
function.
Duncan (1956) proposed the first economic
design of the X-bar chart to show how cost factors
affect the optimality. Moreover, the Lorenzen-Vance
(1986) cost model is a widely used function in
determining the costs of implementing a control
chart.
Following the investigation of the variable
sampling interval (VSI) EWMA chart by Saccucci et
al. (1992), Reynold and Arnold (2001) developed
the variable sample size EWMA (VSSI EWMA)
control chart to improve the performance of the
fixed sample size charts on the speed of detecting
small changes in the mean vector.
For the first time a methodology based on the
skewness reduction approach (Niaki and Abbasi,
2008) and Lorenzen and Vance (1986) cost function
is developed in this paper to economically design a
multiattribute VSSI MEWMA control chart.
2 THE VSSI MEWMA CHART
Assuming vector
i
uur
follows a p-variate normal
distribution with mean vector
0
and covariance
93
Taghi Akhavan Niaki S. and Jahani P..
ECONOMIC DESIGN OF MEWMA VSSI CONTROL CHARTS FOR MULTIATTRIBUTE PROCESSES.
DOI: 10.5220/0003695400930099
In Proceedings of the 1st International Conference on Operations Research and Enterprise Systems (ICORES-2012), pages 93-99
ISBN: 978-989-8425-97-3
Copyright
c
2012 SCITEPRESS (Science and Technology Publications, Lda.)