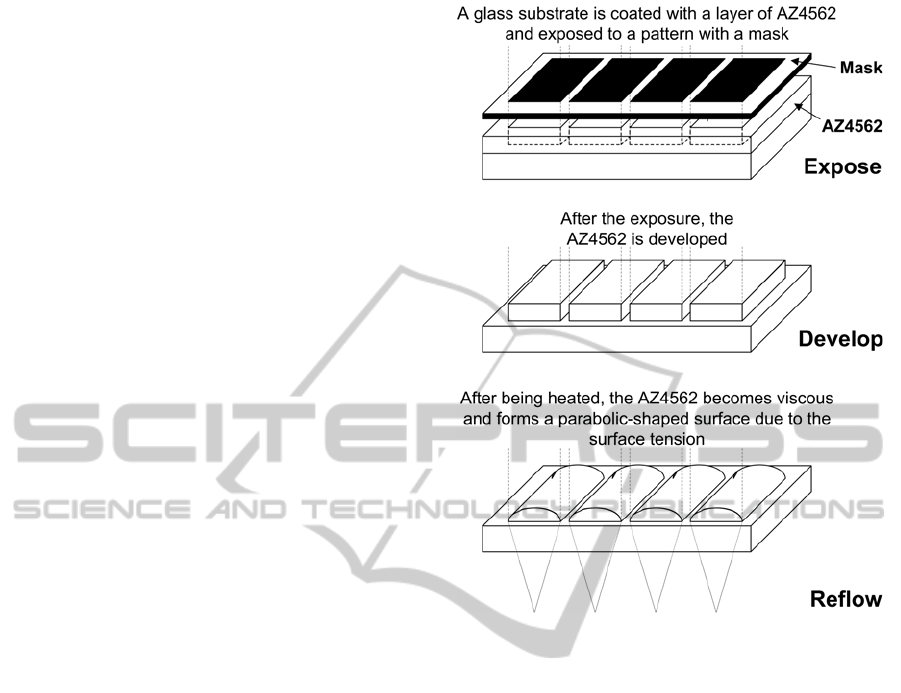
industry. Thus, CMOS microdevices are more
standardized and cost-effective to produce then the
CCDs microdevices. Considering the low-power
consumption of the CMOS microdevices, another
possibility that presents itself for the imaging
sensors is the integration of thin-films batteries with
silicon compatibility (Chan et al., 2008) and low
toxicity (Armand and Tarascon, 2008). The inherent
characteristics of the proposed imaging sensor
presented in this paper make it an interesting
solution for the capsule endoscopy integration
including the thin-films battery as the power source.
The fabrication of such a microdevice can be done
using the 0.7 µm CMOS process in the AMIS
foundry because it allows the production of both the
photodetectors and the read-out electronics within a
reasonable cost. Finally, since the aforementioned
process is very well characterized and known, the
time to manufacture the first working prototype is
expected to be short. This paper addresses on the
design and fabrication technology of the microlenses
for providing stereoscopic vision.
2 IMAGE SENSOR
ARCHITECTURE
The image sensor is composed by two pupils (two
entrance apertures just like the human eyes) from
where the left and right channels (the two POVs that
will originate the tridimensional effect) pass through
before being focused by an objective lens. This lens
focuses the two incident beams in the direction of
the microlens, where the light is concentrated in a
small sensitive area where the photodiodes are
placed. After passing through the optical filters, the
wavelengths coming from both the entrance
apertures are directed towards the respective CMOS
photodiodes. The two viewpoints are separated by
focusing each side onto the appropriate sensor
column under the microlens and optical filters.
3 MICROLENSES FABRICATION
A. Microlens fabrication
There is a huge number of materials available for
fabricating microlenses arrays such as the SU-8/2,
AZ9260 and AZ4562, for example. These polymers
allow the microlens fabrication by thermally
reflowing the raw material, whose processing steps
Figure 2: The reflow process applied to the AZ4562
photoresist for fabricating microlenses arrays.
of the reflow process are presented in the Figure 2.
This permits the production of arrays containing a
million or more microlens of good optical quality in
just a few minutes and with high degree of
reproducibility of their characteristics. There are a
few geometrical parameters to take in account before
fabricating the microlenses. As depicted in Figure 3,
the paraxial focal length, f, of a microlens consisting
of a single spherical surface of radius R in a medium
of refractive index, n, is given by f=R/(n-1) and the
height, h, of the surface undulation of a microlens
with an aperture radius, r, is h=R-(R
2
-r
2
)
1/2
. The
volume of a cylinder of resist is Tπr
2
, where T is the
thickness before melting and the volume of the
microlens is 1/3πh
2
(3R-h). It therefore follows that
the necessary thickness is given by T=h/6×[3+(h/r)
2
].
The reflow process works well for microlenses of a
relatively high-numerical aperture (and low-focal
length, f), where the lens constitutes a significant
fraction of a hemisphere. This process is very tolerant
of the state of resist before melting, thus, acceptable
lenses can be made with aperture ratios between f/1
and f/3.
MICROLENSES FOR STEREOSCOPIC IMAGE FORMATION
115