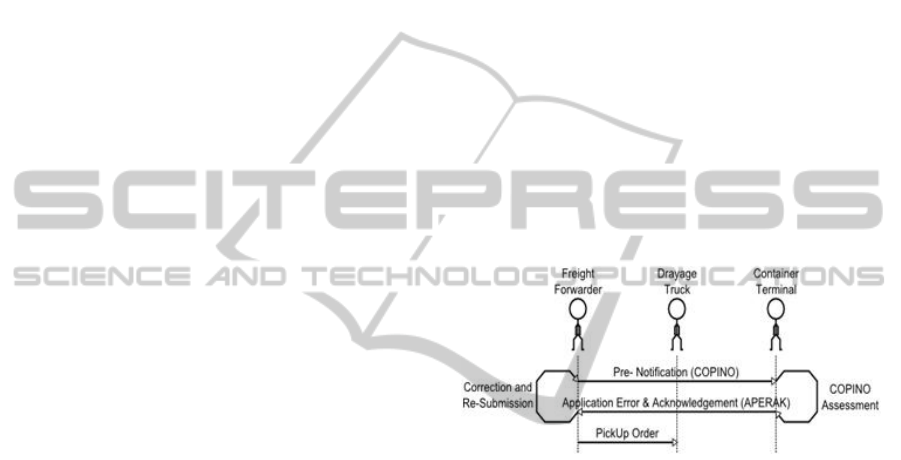
is presented by Thurston and Hu (2002). They put
forward an ABM architecture concept for handling
three different operations: the containers’ retrieval
from the stacking yard, the containers’ transportation
between the yard and the quay area, and the
containers’ transfer from the quay side to the vessel.
More recently, more validated CT-ABM studies
have emerged. These do not only propose ABM
architecture concepts for specific operation
application; validated studies normally also present
simulation works to validate their proposals
(Davidsson et. al., 2005). One good example is the
work of Henesey (2006). In his study, he presents a
thorough overview of the CT operations, proposes a
concept of ABM architecture, and elaborates on
several simulation studies focusing on numerous
operational issues such as: vessel arrival sequencing,
vessel berthing, inter-terminal transportation, etc.
Another recent work is carried out by Winikoff et.
al., (2011). They present an ABM open source
emulation platform (ContMAS) that is intended as a
decision support system for assessing different CT
policies. Moreover, in their study, they present a
negotiation-based module for container moves
allocation to the CT’s internal transporters and they
also propose a genetic-algorithm based solution for
allocating the containers in the yard.
We noted that most studies focus on the CT’s
marine interface operation (Henesey, 2006). The
landside interface operation is largely unexplored.
We have noted (only) one ABM study that analyzed
the interface operations between the CT and the land
carriers (Vidal & Huynh, 2010). Focusing on the
containers’ pick-up operation context, they have
analysed the impact of applying different yard crane
strategies to the drayage trucks’ service time. Instead
of solely focusing on the crane’s operational strategy
as was done in the study by Vidal and Huynh
(2010), we have extended their research by
concentrating more on the information protocol
improvement issue.
3 PROBLEM DESCRIPTION
The CT conducts two services: the marine interface
and the landside interface operations. The marine
interface operations are all activities that correlate
with the vessel service. The landside interface
operations deal with the service of land connecting
carriers (i.e. trains and trucks). In this study, we
focus on the CT’s landside interface operations.
More specifically, we analyze the container pick-up
process carried out by the drayage trucks (DTs).
The container pick-up process consists of two
different procedures: the pre-arrival and the on-
arrival procedures. In the following sections, we will
discuss each procedure in detail and we will discuss
the opportunity to improve operational performance
of the pick-up process by synchronizing both
procedures.
3.1 Container Pickup - Pre-arrival
Procedure
Prior to the container pick-up by the DT, the freight
forwarder has to finalize the pre-arrival formalities.
The pre-arrival procedure, which is actually a
request for pick-up confirmation, consists of several
information exchange formalities. The formalities
are regulated by the United Nations Committee for
Electronic Data Interchange for Administration,
Commerce, and Transport (UN/EDIFACT)’s
regulation. Figure 1 represents the pre-arrival
procedure.
Figure 1: Container pick-up pre-arrival procedure.
As portrayed, firstly, the freight forwarder sends
a container pick-up permission request to the CT in
the pre-notification message format, COPINO. A
COPINO message contains numerous details that
have to be completed by the freight forwarder. In
short, the COPINO confirms three important issues:
the identity of the container, the identity of the DT
that will pick up the container, and the proposed
pick-up date. Note that an incomplete COPINO form
may lead to request rejection.
Once the COPINO is received by the CT, several
checks will be carried out, including the evaluation
of the information details completeness, the presence
of the container in question at the CT, the customs
clearance procedures and some operational issues.
Once all the checks have been finalized, the CT
sends a reply message to the freight forwarder. The
reply is written in an APERAK (Application Error
and Acknowledgement) format. APERAK indicates
the approval/rejection status of the COPINO.
Upon receipt of the APERAK, if the COPINO
request has been approved, the freight forwarder can
IMPROVING THE PRE-NOTIFICATION PROTOCOL OF THE CONTAINERS PICK-UP PROCEDURE - An
Agent-based Approach
191