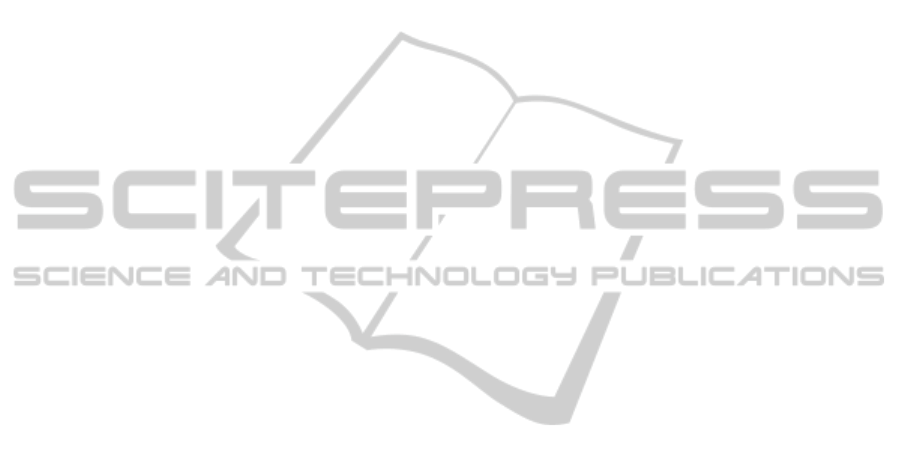
The Agre model does not take into account the
randomness of the parameters under uncertainty.
The impact of this randomness must be captured by
the safety stock that must be guaranteed at each sto-
rage point along the planning horizon. This
minimum stock should be sufficient to deal with
uncertainty. The model which estimates the
minimum stock level is described in the next section.
4.2 Minimum Stock (Mist) Model
The empty container minimum stock (Mist) model
should estimate a minimum inventory at each
storage point, to meet the randomnes of the problem.
Based on certain demand for initial stock at the
first time period, we must make a decision on the
inventory to stock. In each period, when making a
decision, the history of previous decisions and
realizations of random variables is known, ignoring
the future demand and supply.
The cost function of the Mist model considers
only the stock costs, specifically, the mean cost
along the planning horizon. Note that, since the
solution of depends on random parameters of
demand and supply, then it also is random.
Contrary to the aggregated replenishment model,
the demand and the supply are random variables
with known probability functions. Additionally, the
damage rate and the devolution times are considered
probabilistically.
Solution of the Mist model provides the
minimum container stock, which will be used as a
parameter by the Agre model in order to capture the
randomness of the system and face the uncertainty.
4.3 Solution to the Mist Model based
on the Sample Average
Approximation
In order to solve the Mist stochastic non-linear
model described previously, the sample average
approximation, or SAA, method is used. This
method generates an approximation of the
probability distribution of the random variables by
Montecarlo simulation. On each period of the time
horizon, realizations of the random variables are
generated, about which decisions should be made.
The motivation for using this method lies in the
following reasons: a) Multiple randomness sources
exist, with heterogeneous probability distributions;
b) The planning horizon considers multi-periods; c)
The probability distributions of the random variables
can be expressed through discrete functions; e)
Based on the previously established assumption of
independence and no self-correlation for the random
variables, random scenarios can be easily generated;
f) Since the Mist model does not include binary or
integer variables, the problem can be solved by a
polynomial size linear program.
5 IMPLEMENTATION AND
RESULTS
We code the models in GMPL to test the
performance robustness of the model. It is important
to note that the computational complexity of the
solution is determined by the complexity of the Mist
problem, given the large number of scenarios that
have to be generated in order to simulate the
randomness of the system. For an instance of one
yard, one container type, a fourweek planning
horizon, and a tree with 1,000 random scenarios, the
matrix of the associated program has a size of
62,000 columns and 5,000 constraints before pre-
processing.
We construct four data sets with four different
demand probability distributions, empirical, normal,
lognormal and uniform, for fourty experiments
corresponding to fourty probability trees. To test the
robustness of the model, the variation of the optimal
solution for expected cost and average minimum
stock over the four periods was recorded, using the
sample variability coefficient as the estimator. To
measure the performance of the model, solution
times and memory usage were recorded; note that it
is expected that the running frequency of the
application is not grater than one run per week.
5.1 Conclusions and Perspectives
Inspired by the work of Shen and Khoong (1995),
the model presented in this paper proposes a
hierarchical solution approach to the Dynamic
Empty Container Allocation Problem that divides
the problem into two models: Mist, the estimation of
the minimum stock necessary to deal with
uncertainty at every storage point over a planning
horizon, and Agre, the estimation of the flow of
container replenishment to ensure compliance with
those minimum stocks levels and business demand
budgets. These models are also inspired by several
of the works mentioned before and operating
conditions of the specific problem described.
However, unlike the works mentioned, the proposed
models also consider the possibilities of observing
damage to containers and repairs’ random times.
ICORES 2012 - 1st International Conference on Operations Research and Enterprise Systems
478