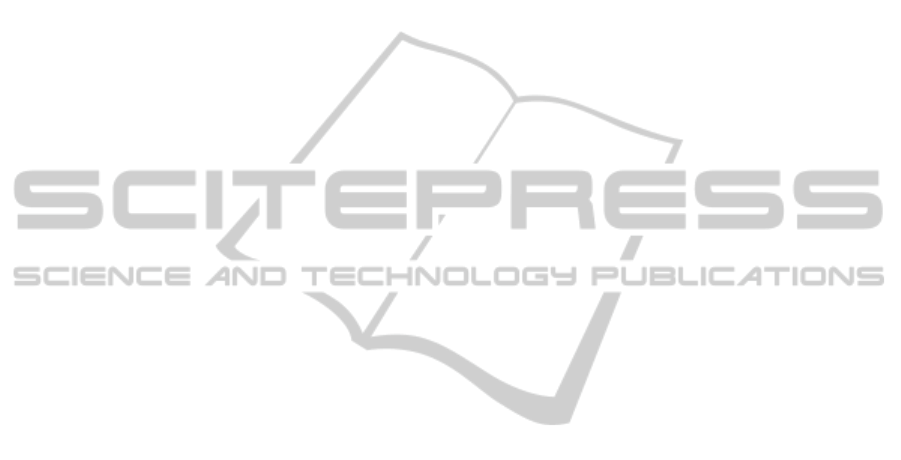
As the embedding and recursive formulations
use relative coordinates, however, these
formulations need additional computation to
calculate the constraint force. Unlike augmented
formulation, moreover, the values that are associated
with relative motion between the bodies are
explicitly calculated using the embedding and
recursive formulations.
In the case of augmented formulation, the
number of equations of motion is 6n+p, which is
proportional to the number of bodies. As the
computational time for the calculation of the inverse
matrix is proportional to (6n+p)
3
, the complexity of
computation is O(n
3
) for solving the equations of
motion.
The number of equations of motion derived
using embedding formulation is 6n-p. As the
computation time for the calculation of the inverse
matrix is proportional to (6n-p)
3
, the complexity of
computation is O(n
3
) for solving the equations of
motion for the multibody system. As the matrix of
embedding formulation is smaller than that of
augmented formulation, the computational
efficiency of embedding formulation is better than
that of augmented formulation.
Unlike the two other formulations, recursive
formulation does not need to assemble a system of
equations of motion for each body as it is a recursive
method. Therefore, although the number of matrices
increases in proportion to the number of bodies n,
the size of the matrix of the equations of motion is
always 6×6. Consequently, the complexity of
computation is O(n) for solving the equations of
motion (Stejskal et al., 1996). In this study, due to
the computational efficiency, recursive formulation
was used to derive the equations of motion.
3.2 External Forces for the Dynamic
Response Analysis
Eq. 1 shows the external forces considered for the
dynamic response analysis. The external forces
consist of the hydrostatic forces with nonlinear
effects considering wave elevation, the linearized
hydrodynamic force, the mooring force, the
aerodynamic force, and the gravitational force, as
follows:
() () () ()
,,, , ,,
()
e
Hydrostatic Hydrodynamic Mooring
Aerodynamic Gravity
tt t=+ +
++
f
f
f
f
fqf
&&& &&&
(1)
The module for calculating the external forces is
developed, and it is used for the dynamics kernel
(Ku et al., 2011).
4 MULTIBODY DYNAMICS
KERNEL IN DISCRETE EVENT
SIMULATION
In the previous section, the development of the
dynamics kernel was presented. However, it is hard
to deal with the discontinuous state variables, event
triggered conditions, and state triggered conditions
using the dynamics kernel. To overcome this
limitation, this study adopts the DEVS (Discrete
Event System Specification) formalism to develop
the simulation program.
4.1 DEVS (Discrete Event System
Specification) Formalism
The DEVS formalism, a set-theoretic formalism,
specifies ‘discrete event systems’ in a hierarchical
and modular form. The DEVS formalism consists of
two kinds of models: an atomic model and a coupled
model. The atomic model is the basic model and has
specifications for the dynamics of the model.
Formally, 7 components, which are state variables,
input events, output events, external transition
function, internal transition function, output function,
and time advance function, specify the atomic model.
The coupled model provides the method of assembly
of several atomic and/or coupled models to build
complex systems hierarchy. Each DEVS model,
either atomic or coupled, has correspondence to an
object in the real-world system to be modeled
(Zeigler, 1990, Zeigler et al., 2000).
However, the simulation progresses by changing
the state variables for not only every event but also
every unit time. Thus, the DTSS (Discrete Time
System Specification) model is combined with
DEVS model. The atomic model of DTSS is
composed of 7 components, which are state
variables, input events, output events, external
transition function, output function, integral function,
and state event function. The simulation model is
called ‘combined DEVS and DTSS simulation
model’. In this paper, for simplicity, the simulation
model will be called ‘DEVS simulation model’.
In this study, each facility shown in Fig. 1 is
modeled as an atomic model based on DEVS
formalism, and the coupled models are defined by
assembly of the several atomic models. In the next
sub-section, it will be explained how to define the
atomic model and the coupled model for the
simulation of the process planning in shipbuilding.
ICORES 2012 - 1st International Conference on Operations Research and Enterprise Systems
450