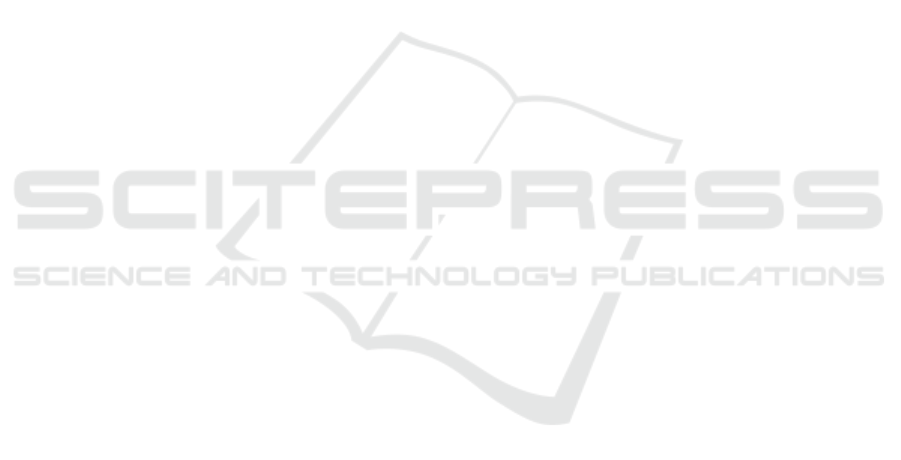
A 130NM ASIC FOR EMG SIGNAL ACQUISITION
TO CONTROL A HAND PROSTHETIC
Lait Abu Saleh, Wjatscheslaw Galjan, Jakob Tomasik,
Dietmar Schroeder and Wolfgang H. Krautschneider
Institute of Nanoelectronics, Hamburg University of Technology, Eissendorfer Strasse 38, 21073, Hamburg, Germany
Keywords: EMG signal acquisition, Hand prosthetic, Bio-signal amplifier, Mixed-signal chip, Medical implant.
Abstract: A mixed-signal chip in 130nm Technology is described. The chip acquires EMG signals from five
differential inputs. The signals are amplified, multiplexed and digitized inside the developed chip. The
ASIC is optimised for low power and low noise and is intended for application in medical implants.
Furthermore, the chip provides a configuration options for several parameters for the analogue part of the
chip. The chip has been tested by recording EMG signals from implanted Myo-Electrodes.
1 INTRODUCTION
The loss of upper extremities puts several limitations
on trivial functions in daily life. The hand is
probably the most important part of the skeletal-
muscular system in the human body. Therefore
providing people with a proper alternative, which
replaces the lost functionality, constitutes an
important task. The purpose of the MyoPlant project
is the development of a bionic hand prosthesis
system with multiple degrees of freedom, based on a
myogenically controlled intelligent implant. The
project partners are the company Otto Bock
Healthcare GmbH, the German Primate Center DPZ
(Goettingen), the Fraunhofer Institut for Biomedical
Engineering (IBMT), the Technical University
Hamburg-Harburg and the Werner-Wicker-Clinic
(Bad Wildungen) and in cooperation with the
Medical University Vienna.
This article describes the development of an
application-specific integrated circuit (ASIC) for
invasive acquisition of muscular activity in order to
deliver an input for the controller of a hand
prosthetic. The ASIC is intended for use in the
implant above mentioned. The main task of the
ASIC is to record multiple EMG signals from
electrodes connected to the implant’s input, to
amplify the recorded signals, and to deliver these
signals digitally at the output. The digitized data
samples are collected by a microcontroller on the
implant, which sends them to a telemetry chip for
wireless transmission to the external system of the
hand prosthesis.
Volume, power consumption, low noise, and
efficiency play an essential role during the
development of an implantable system. A trade-off
between these parameters is often inevitable for the
developer. A transistor technology with small
feature size has many advantages considering area
reduction and power consumption. At the same time,
the same technology may have strong drawbacks in
terms of noise contribution and amplification factor.
2 SYSTEM REQUIREMENTS
AND SPECIFICATION
Muscle cells have a potential difference of ~100 mV
between the intra- and extracellular medium
(Principles of Neural Science, 2000), while
implanted electrodes record amplitudes in the range
of 100 μV – 5 mV. Therefore, a system for
amplifying these small bio-signals is needed. The
impedance of the used electrodes and the strength of
the bio-signal are important values for the
dimensioning of the bio-amplifier. The electrode
interface and the bio-amplifier input constitute two
impedances in series connected to the bio source
signal. This implies a voltage divider for the signal
source. The input impedance of the bio-amplifier
should be much larger than the impedance of the
electrode interface in order to obtain a large voltage
drop on the input of the amplifier.
The bio-amplifier also needs to accommodate the
149
Abu Saleh L., Galjan W., Tomasik J., Schroeder D. and H. Krautschneider W..
A 130NM ASIC FOR EMG SIGNAL ACQUISITION TO CONTROL A HAND PROSTHETIC.
DOI: 10.5220/0003765101490153
In Proceedings of the International Conference on Biomedical Electronics and Devices (BIODEVICES-2012), pages 149-153
ISBN: 978-989-8425-91-1
Copyright
c
2012 SCITEPRESS (Science and Technology Publications, Lda.)