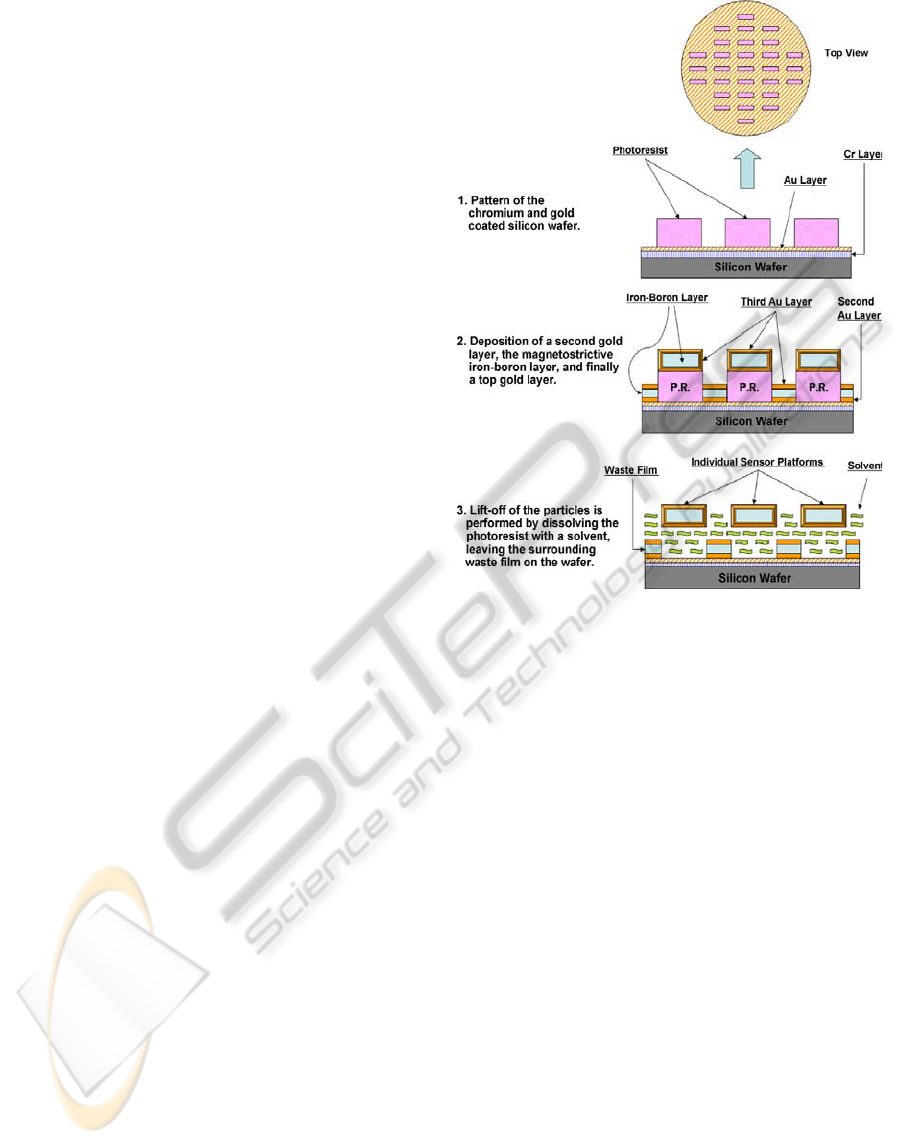
chromium merely serves to act as a bond between
the silicon and the gold. Next, a layer of photoresist
is applied to the gold surface of the wafer by spin
coating such that the resultant thickness is at least
twice that of the desired magnetoelastic film to be
deposited later. This photoresist is then UV exposed
using a positive mask comprised of evenly-spaced
rectangles, which are the desired length and width of
the magnetoelastic sentinels. The wafer is then
developed in a 2:1 solution of de-ionized water and
AZ-400K developer, rinsed, dried, and then
inspected for pattern integrity and thickness.
The magnetoelastic film is then deposited onto
the patterned wafer using the same sputtering system
as before. First, the wafer is loaded into the
deposition chamber, along with a gold, iron, and
boron target for each of the three cathodes, and then
the chamber is pumped down to 7×10
-7
Torr in order
to minimize residual oxygen in the film. Next, a gold
layer is deposited onto the patterned wafer to a
thickness of about 30–40 nm. The magnetoelastic
layer is formed by co-depositing iron (DC) and
boron (RF) simultaneously using a dual-cathode
method. This method differs somewhat from the
usual procedure for co-sputtering iron and boron,
which typically involves using a specially made
composite target. The advantage here is that the
power of each cathode can be tuned separately such
that the film has the desired composition at a
reasonable deposition rate. Thickness of this film
depends on process conditions, and is generally
limited by the thickness of the photoresist layer, but
highly magnetostrictive films of up to about 7 µm
have been obtained using this dual-cathode method.
Finally, another gold layer, using the same
processing conditions as before, is applied on top of
the iron-boron film, such that the magnetostrictive
particles will be completely enclosed in gold. From
an 8" wafer, approximately 40,000 sentinels can be
fabricated. The cost of fabrication of a single 8"
silicon wafer of sentinels is approximately $28.00.
Hence the cost of a single ME sensor is less than
1/1000 of a cent.
2.3 Immobilization of the
Bio-molecular Recognition Layer
To form functional sentinels, a bio-molecular
recognition element must be immobilized onto a
transducing platform to bind the specific target
pathogenic species. Other investigators typically use
traditional antibodies as the biorecognition element.
The strengths and weaknesses of antibody binding
are well known. An antibody is a relatively fragile
Figure 6: The ME resonator fabrication process.
species and subject to denaturation with
consequential loss of sensitivity and other binding
characteristics when exposed to unfavorable
environments. Moreover, the quality of antibodies
can vary with different animals and production
variables. To be used in sentinels, antibodies require
affinity purification and stabilization, which
dramatically increases their cost. Monoclonal
antibodies are more standard and selective, but their
application in the field is hindered by their stability.
The use of phage as substitute antibodies offers a
stable, reproducible and inexpensive alternative
(Petrenko, 2008, Petrenko and Smith, 2000). In
contrast to antibodies, the phage structure is
extraordinarily robust, being resistant to: heat (up to
80 °C) (Brigati and Petrenko, 2005); organic
solvents (e.g., acetonitrile) (Olofsson et al., 2001),
urea (up to 6 M), acid, alkali and other chemicals.
Purified phage can be stored indefinitely at moderate
temperatures without losing infectivity and probe-
binding activity. Three major factors contribute to
the high affinity binding of landscape phage to their
targets: a) constrained conformation of foreign
peptides; b) their multivalent display—thousands of
binding sites per phage filament; and c) extremely
high local concentration of binding sites. The
BIODEVICES 2012 - International Conference on Biomedical Electronics and Devices
50