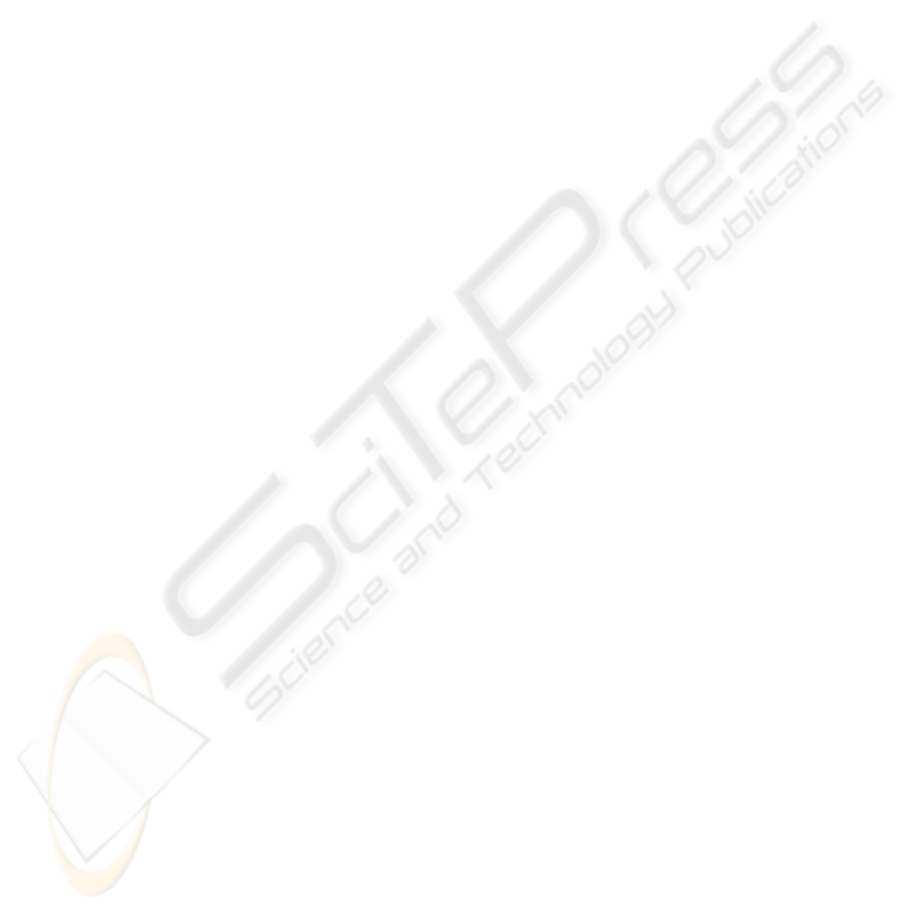
ICOUNTER
Development of an Optical Readout Method for Mechanical Counters
Dirk Benyoucef, Pirmin Held and Thomas Bier
Digital Communications & Signal Processing Lab, Furtwangen University,
Robert-Gerwig-Platz 1, 78120 Furtwangen, Germany
Keywords:
Mechanical counter, Bayes classifier, Nearest neighbors classifier, Pattern recognition, Gray scale recognition,
Cluster analysis.
Abstract:
Mechanical counters are still very common in electricity, water and gas meters. Automatic readout of the
dial count without modifying the mechanics of the counter is only possible using expensive image processing
methods. Therefore the topic of this report is a new method for automatically reading out the counter values
without the need of additional mechanical or parallel electronic parts inside the counter. Instead the different
reflection properties of the different digits are measured and evaluated. This is done using only simple elec-
tronic parts and a microcontroller.
In the first part of the paper the hardware for measuring the reflection values is presented. A model of this
hardware with special emphasis on the influences of the environment is discussed in the next part. Following
this, two classification methods, for distinguishing the digits are analyzed. For showing the properties of the
new readout system measurements and simulations are given in the end.
1 INTRODUCTION
Mechanical counters are used in many different de-
vices, such as for example electricity, water, and
gas counters, cash mashines, and gambling machines.
Most often mechanical counters are used because of
their protection against manipulation. The readout of
the counter values is typically done by a person writ-
ing down the values on paper or computers which in-
volves high costs and makes continuous readout im-
possible. Therefore a possibility for automatically
evaluating the counter value is sought. Most of the
currently known methods for electronic readout use a
parallel electronic counter which is connected to the
mechanics of the counting unit. This does not read
the actual counter value but it reads the value of the
electronic counter. This undoes the advantage of pro-
tection against manipulation of the mechanical coun-
ters.
2 STATE OF ART
The evaluation of optically acquired counter values
is done applying digital signal processing. Pattern
recognition methods are used for the classification of
the digits. Especially the area of image processing
is concerned with finding a pattern in an optically
recorded image of this pattern. One way of achiev-
ing this is based on the gray level recognition. Otsu
has evaluated histograms of gathered images for this
purpose (Otsu, 1979). A second application was de-
scribed by (Martinez-Carballido et al., 2011). An-
other work concerned with the recognition of digits
was carried out in the year 2006 (Qian et al., 2006).
Many different methods can be applied in the area of
the optical recognition of counter values (Shu et al.,
2007). In 2010 Zhang et al. developed a portable
optical system (Zhang et al., 2010). For the pattern
recognition they applied different algorithms com-
prising including morphology, gray scale conversion,
edge detection and the Hough transformation. The
disadvantage of this method is that the readout of the
counter values has to be done manually. Another ap-
proach is based on the optical scanning using a video
camera. In 2007 Shu et al. presented a method for
recording the values of electronic counters (Shu et al.,
2007).
The disadvantages of the methods shown before
are the fact that the data acquisition has to be done
manually and that the presented readout units need ex-
pensive hardware. This is the basis for a new system.
The main advantage of this system is that no modifi-
576
Benyoucef D., Held P. and Bier T. (2012).
ICOUNTER - Development of an Optical Readout Method fot Mechanical Counters.
In Proceedings of the 1st International Conference on Pattern Recognition Applications and Methods, pages 576-580
DOI: 10.5220/0003779605760580
Copyright
c
SciTePress