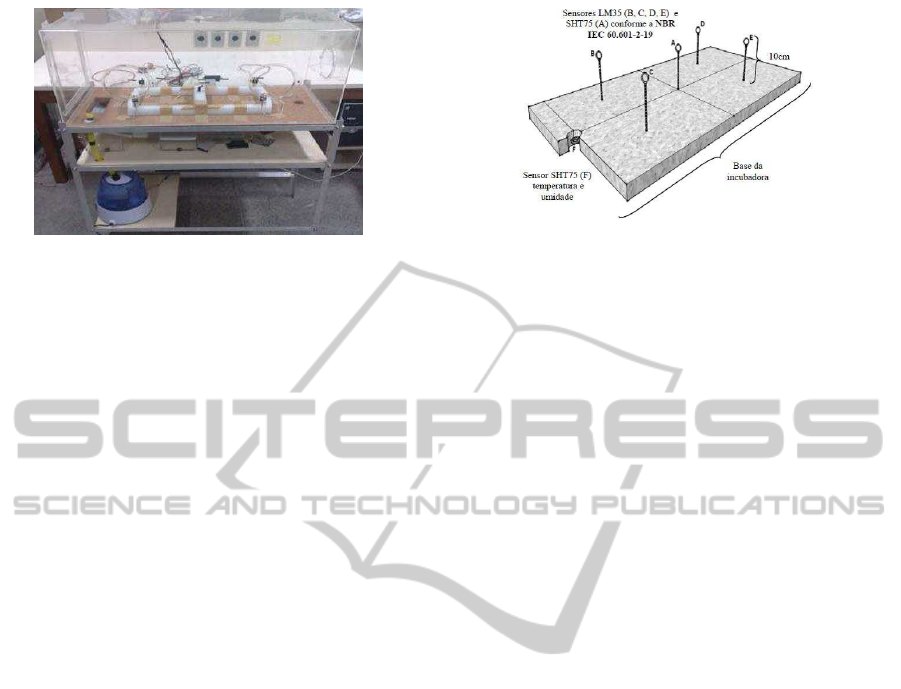
Figure 1: Prototype of the incubator.
uses artificial neural networks (Haykin, 2008) as a
technique for the identification of nonlinear systems,
to the identification of signals of temperature and hu-
midity in the positions defined by the standard, as
only a single temperature and humidity sensor in-
stalled in the exhaust air of the incubator. The model
is intended to found its future use in a predictive con-
troller, acting as the controller model and also insert-
ing the restrictions provided by the standard output.
This work is organized in the following topics: sec-
tion 2 describes the prototype of the incubator used
in the experiments. The section 3 discusses a review
about artificial neural networks, in particular the mul-
tilayer perceptron architecture. The 5th section are
shown the tests and the results obtained and the sec-
tion 6 tells about the conclusions and final comments.
2 THE INCUBATOR PROTOTYPE
The incubator prototype built in the GPAR/DEE/UFC
(Research Group in Robotics and Automation) re-
search laboratory is shown in Figure 1.
The prototype is divided into two basic parts: the
supporting structure with aluminum rods and wood
planks and the acrylic dome with porthole windows
similar to commercial models of incubators. In
the supporting structure, just below the dome, is an
acrylic duct forming an air circulation system of the
incubator, where are installed a resistive heater and a
cooler on opposite ends of the circuit. Below the air
circulation system are the boards of control systems
of heating, ventilation and relative humidity. Also be-
low the ventilation system is located a commercial hu-
midifier adapted in moisture control. The control sys-
tem of the incubator can be divided into 3 subsystems
of control: temperature control system, control sys-
tem of moisture and ventilation system. The systems
of control of temperature and humidity are connected
to an acquisition board of National Instruments
TM
(NI) to connect these two systems with Matlab
TM
Figure 2: Spatial distribution of sensors inside the incuba-
tor.
software. The ventilation system operates indepen-
dent of the acquisition card, being that this was ad-
justed to maintain a constant ventilation speed of ap-
proximately 0.35 m/s, in accordance with the stan-
dard NBR IEC 601-2-19. The interior of the dome
is thermally isolated through a cork board of 24mm
thickness. Temperature and humidity sensors were in-
stalled in the interior of the dome following the provi-
sions in standard NBR IEC 601-2-19 and in the air of
the dome. Figure 2 shows the arrangement of sensors
on the board of cork. The sensors at positions B, C,
D, E, are temperature sensors LM35 (Semicondutors,
2000), while the sensors A and F are temperature and
humidity of type SHT75 (Sensirion, 2010).
The sensors A, B, C, D and E remain inside the in-
cubator during the tests, only being removed from the
dome to the normal operation of incubator because
sensors occupy the positions where the newborn is
placed. The sensor F, which is not specified by the
standard (ABNT, 2000), remains during the tests and
the normal operation of the incubator. From measure-
ments of the sensor F, performed during calibration, it
is estimated a dynamic model of temperature and hu-
midity in the interior of the dome. Through the model
we intend to evaluate, during normal operation of the
incubator, if there was deterioration in the calibration
of the incubator. In the next section describes neu-
ral network used to perform the construction of the
model of the signals of temperature and humidity.
3 MULTILAYER PERCEPTRON
NEURAL NETWORK
In this paper, it is used a neural network MLP (Multi-
layer Perceptron) (Haykin, 2008) to estimate the sig-
nals of temperature and humidity in the interior of the
dome’s incubator. The MLP is formed by neurons
distributed on layers that have high connectivity with
layer neurons following in a feed forward configura-
tion (Figure 3). The propagation of the signals takes
ARTIFICIAL NEURAL NETWORKS IN THE ESTIMATION OF MEASURES OF TEMPERATURE AND HUMIDITY
INSIDE A NEONATAL INCUBATOR
277