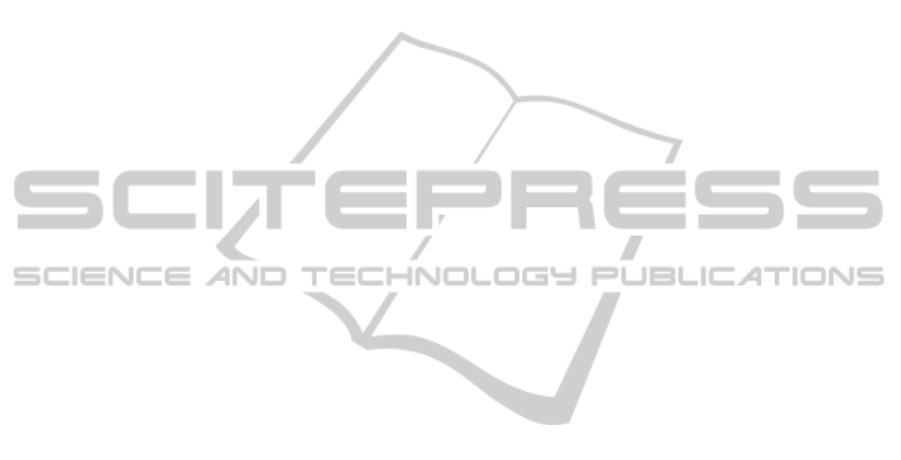
While smartphones provide the platform and tools
for AR (Wagner, 2009), existing mobile AR
approaches are not well suited for a construction
environments due to their lack of accuracy in
spatially locating the user and rendering cyber-
information over the correct physical elements. On a
construction site, discrepancies between physical
elements and the BIM must be detected to within a
few centimetres or less. AR approaches, based on
GPS and compass sensors (Gotow et al., 2010), can
have multiple meters of inaccuracy, making them
unreliable for construction scenarios.
Solution Approach Hybrid 4-Dimensional
Augmented Reality: This paper presents an
augmented reality approach, called Hybrid 4-
Dimensional Augmented Reality (HD
4
AR) that
allows construction field personnel to use mobile
devices, such as a smart phone or tablet, to take
pictures that include a specific construction element,
see BIM elements visually overlaid on top of the
real-world imagery, touch or click on a BIM element
in the image, and be presented with a detailed list of
cyber-information, such as plan information (e.g.,
budget, specifications, architectural/structural
details) or actual information (e.g., cost, safety
provisions, physical progress) related to the physical
element. Screenshots from the Android HD
4
AR
client are shown in Figure 1.
This paper provides the following contributions to
the study of high-precision augmented reality
systems:
1. The paper shows how computer vision
algorithms can eliminate the need for external
sensors to provide reliable location tracking
information for providing context awareness.
2. The paper demonstrates how imagery of physical
elements can be used to access cyber-information.
3. The paper describes an AR technique with high-
precision that does not rely upon marking physical
construction elements with fiducial tags or external
equipment to provide high-precision localization.
The remainder of this paper is organized as follows:
Section 2 presents a motivating example that we use
to illustrate the challenges of associating cyber-
physical information on a construction site; Section
3 discusses HD
4
AR and its approach to high-
precision cyber-physical information association;
and Section 4 presents concluding remarks.
2 MOTIVATING EXAMPLE
As a motivating example, we use a scenario where a
field engineer is concerned about the construction
progress and quality of a concrete foundation wall.
With current approaches, the field engineer would
return to a construction trailer or office and open 2D
construction drawings (at best a 3D BIM), project
specifications, and the schedule to find out when the
construction of this element is expected to be
finished and what is the required quality of the
outcome. Once the drawings and/or 3D building
model is opened, the field engineer must navigate
the model to determine which, of possibly hundreds
or thousands of walls, is the foundation wall of
concern. Moreover, once the information is
obtained, the field engineer may need to return to the
construction site to compare the information that
was retrieved to the actual construction status of the
real foundation wall. Because there is no way to
directly query the cyber information for the wall, the
field engineer may not notice a discrepancy and will
not be able to decide on a corrective action to
minimize the impact of the discrepancy.
Instead, it would be beneficial if the field
engineer can use the foundation wall as the basis for
the query. A picture provides all that is needed to
localize the user with respect to their environment,
and thus reduce the information available down to
what is relevant to the current scene. Given the close
proximity of construction elements, the location and
orientation of the picture needs to be accurately
estimated to return the related information to the
field engineer. This process should not affect the
construction’s workflow by requiring tagging of
elements, which considering the number of elements
on a typical residential building construction site
(~1000-30,000 elements), makes tagging time
consuming and often impractical.
3 HYBRID 4-DIMENSIONAL
AUGMENTED REALITY
Using computer vision, researchers have shown that
a set of overlapping images can be used to extract
the 3D geometry of a stationary object, such as a
building under construction (Golparvar-Fard et al.,
2011); (Cheng and Chen, 2002); (Golparvar-Fard et
al., 2009). As shown in Figure 1 the 3D geometry
extracted using computer vision can then be overlaid
and aligned with manually created BIM models of
the construction project to create a fused cyber-
physical model. Numerous research approaches have
looked at the applications of these techniques
(Golparvar-Fard et al., 2011); (Kiziltas et al., 2008).
HYBRID 4-DIMENSIONAL AUGMENTED REALITY - A High-precision Approach to Mobile Augmented Reality
157