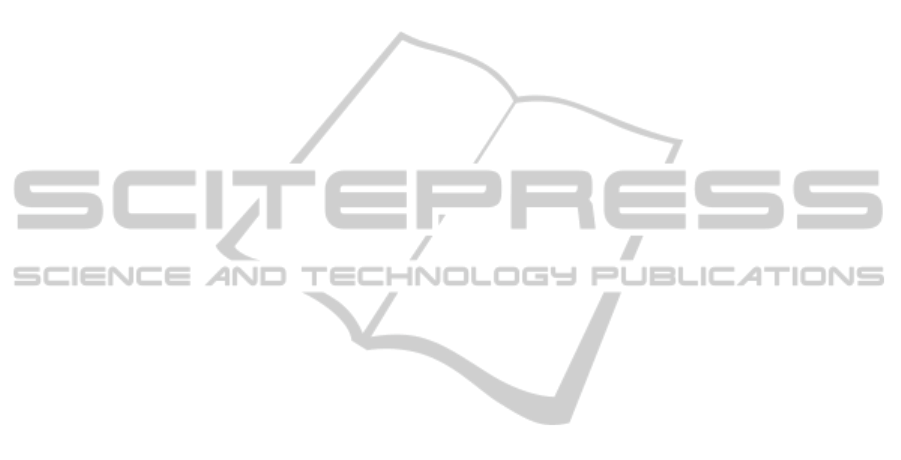
to start developing application on a comfortably sized
development environment. At same time, as soon
as application is specified, it is possible to develop
a shrunk application platform, which uses previously
designed and tested software. This work flow ensures
highest level of flexibility and saves a lot of precious
development time.
6 FUTURE WORK
The interoperability of modules is tightly coupled
with a careful assignment of GPIOs. For example a
multiple use of GPIO lines must be avoided as any
SPI slave needs a dedicated chip select or interrupt
line. Our current set of TandemStack modules is still
surveyable. To keep an overview becomes more and
more difficult with future extensions. A tool support
will significantly simplify such a planning process.
Such a tool can help to find a suitable combination of
modules or selection of lines for upcoming modules.
Driven by active projects a broad set of stack mod-
ules is already implemented. Nonetheless, some mod-
ules, which are very useful in research and typically
WSN scenarios, are still missing. Next steps will in-
clude the design of a storage or an FPGA module.
In a lot of application scenarios a low power stor-
age module with a capacity in the megabytes range
will be needed. Flash memories with SPI or I
2
C are
available and fit perfectly to our TandemStack. Fur-
thermore, an FPGA as a high performance, reconfig-
urable processing core is therefore very useful for de-
velopment or required for massive data processing,
e.g. video stream encoding. It can be implemented as
an MCU replacement as well as a high performance
co-processing unit.
7 CONCLUSIONS
This paper described the TandemStack platform and
its Mote Component Interconnect (MCI). The
TandemStack follows the objective to assemble as
few components as possible needed for one functional
unit on a single Printed Circuit Board (PCB). We
assume that modules should only include one mote
component such as MCU, transceiver, power supply,
storage or sensor. Later the modules are connected
by a uniform MCI. We have explained how such
an interconnect can be defined for building a flexi-
ble mote platform where modules can be freely com-
bined. We compared our design with commercially
available motes and demonstrated that a stack archi-
tecture will provide the highest component density.
We illustrated that in contrast to the inflexible motes
our design can be used in various application scenar-
ios with minimal development effort. We have al-
ready implemented more than nine different modules
and could gather experimental results in real world
scenarios as well as in research activities. We are cer-
tain that a flexible, standardized mote platform can
significantly push development activities and mote
deployments.
REFERENCES
Bellis, S. J., Delaney, K., O’Flynn, B., Barton, J., Razeeb,
K. M., and O’Mathuna, C. (2005). Development of
field programmable modular wireless sensor network
nodes for ambient systems. Comput. Commun., 28.
Benbasat, A. Y. and Paradiso, J. A. (2005). A compact
modular wireless sensor platform. In Proceedings of
the 4th international symposium on Information pro-
cessing in sensor networks, IPSN ’05, Piscataway, NJ,
USA. IEEE Press.
Coalesenses (2011). iSense Wireless Sensor Network Hard-
ware Modules.
Crossbow (2011). Moog Crossbow Technologies.
Dutta, P., Taneja, J., Jeong, J., Jiang, X., and Culler, D.
(2008). A building block approach to sensornet sys-
tems. In Proceedings of the 6th ACM conference on
Embedded network sensor systems, SenSys ’08, pages
267–280, New York, NY, USA. ACM.
Evidence (2010). Technical datasheet - Flex mini kit.
Horton, M., Culler, D., Pister, K., Hill, J., Szewczyk, R.,
and Woo, A. (2002). MICA, the commercialization of
microsensor motes. Sensors, 19(4):40–48.
Labs, S. (2010). Sun SPOT Main Board Technical
Datasheet.
Lymberopoulos, D., Priyantha, N. B., and Zhao, F. (2007).
mPlatform: a reconfigurable architecture and efficient
data sharing mechanism for modular sensor nodes. In
Proceedings of the 6th international conference on In-
formation processing in sensor networks, IPSN ’07,
pages 128–137, New York, NY, USA. ACM.
Moteiv (2006). Tmote Sky Datasheet
http://www.sentilla.com/pdf/eol/tmote-sky-datasheet.
pdf.
Piotrowski, K., Sojka, A., and Langend¨orfer, P. (2010).
Body Area Network for First Responders - a Case
Study. In Proceedings of the 5th International Con-
ference on Body Area Networks.
Polastre, J., Szewczyk, R., and Culler, D. (2005). Telos:
enabling ultra-low power wireless research. In Infor-
mation Processing in Sensor Networks, 2005. IPSN
2005. Fourth International Symposium on, pages 364
– 369.
Schott, B., Bajura, M., Czarnaski, J., Flidr, J., Tho, T., and
Wang, L. (2005). A modular power-aware microsen-
sor with 1000x dynamic power range. In Proceed-
ings of the 4th international symposium on Informa-
tion processing in sensor networks, IPSN ’05, Piscat-
away, NJ, USA. IEEE Press.
SENSORNETS 2012 - International Conference on Sensor Networks
72