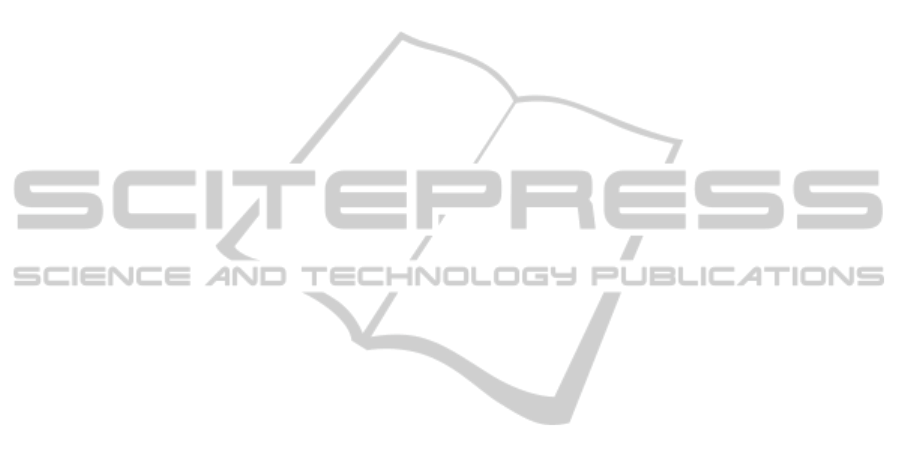
REFERENCES
Abawi, D. F., Luis, J., Arcos, L., Haller, M., Hartmann, W.,
Huhtala, K., and Trskbck, M. (2004). A mixed reality
museum guide: The challenges and its realization. In
Proceedings of the 10th International Conference on
Virtual Systems and Multimedia (VSMM 2004).
Azuma, R. (1997). A survey of augmented reality.
Presence: Teleoperators and Virtual Environments,
6(4):355–385.
Baird, K. and Barfield, W. (1999). Evaluating the effec-
tiveness of augmented reality displays for a manual
assembly task. Virtual Reality, 4:250–259.
Blanchette, J. and Summerfield, M. (2008). C++ GUI Pro-
gramming with Qt 4. Open Source Software Develop-
ment Series. Prentice Hall.
Breen, D. E., Whitaker, R. T., Rose, E., and Tuceryan, M.
(1996). Interactive occlusion and automatic object
placement for augmented reality. Computer Graph-
ics Forum, 15(3):11–22.
Burns, D. and Osfield, R. (2004). Open scene graph a: In-
troduction, b: Examples and applications. In Proceed-
ings of the IEEE Virtual Reality Conference 2004 (VR
2004), page 265.
Campbell, D. J. (1988). Task complexity: A review and
analysis. Academy of Management Review, 13(1):40.
Cawood, S. and Fiala, M. (2008). Augmented Reality: A
Practical Guide. Pragmatic Bookshelf.
Friedrich, W. (2002). Arvika-augmented reality for devel-
opment, production and service. In In Proceedings
of the IEEE/ACM International Symposium on Mixed
and Augmented Reality (ISMAR02),, pages 3–4.
Hampshire, A., Seichter, H., Grasset, R., and Billinghurst,
M. (2006). Augmented reality authoring: generic con-
text from programmer to designer. In In Proceed-
ings of the Australasian Computer-Human Interaction
Conference (OZCHI’06), pages 409–412.
Haringer, M. and Regenbrecht, H. T. (2002). A pragmatic
approach to augmented reality authoring. In Proceed-
ings of the 1st International Symposium on Mixed and
Augmented Reality, ISMAR ’02, pages 237–, Wash-
ington, DC, USA. IEEE Computer Society.
Henderson, S. J. and Feiner, S. (2009). Evaluating the bene-
fits of augmented reality for task localization in main-
tenance of an armored personnel carrier turret. In Pro-
ceedings of the 2009 8th IEEE International Sympo-
sium on Mixed and Augmented Reality, pages 135–
144. IEEE Computer Society.
Kato, H. and Billinghurst, M. (1999). Marker tracking
and hmd calibration for a video-based augmented re-
ality conferencing system. In Proceedings of Inter-
national Workshop on Augmented Reality (IWAR’99),
pages 85–94.
Ledermann, F. and Schmalstieg, D. (2005). April: A high-
level framework for creating augmented reality pre-
sentations. In In Proceedings of the IEEE Virtual Re-
ality Conference 2005 (VR 2005), pages 187–194.
MacIntyre, B., Gandy, M., Dow, S., and Bolter, J. (2005).
Dart: a toolkit for rapid design exploration of aug-
mented reality experiences. ACM Transactions on
Graphics (TOG) - Proceedings of ACM SIGGRAPH
2005, 24(3).
Neumann, U. and Majoros, A. (1998). Cognitive, perfor-
mance, and systems issues for augmented reality ap-
plications in manufacturing and maintenance. In In
Proceedings of the IEEE Virtual Reality Annual Inter-
national Symposium (VR ’98), pages 4–11.
Nilsson, S., Johansson, B., and Jnsson, A.(2010). The Engi-
neering of Mixed Reality Systems, chapter A Holistic
Approach to Design and Evaluation of Mixed Reality
Systems, pages 33–55. Human-Computer Interaction
Series. Springer.
Ong, S. K., Yuan, M. L., and Nee, A. Y. C. (2008). Aug-
mented reality applications in manufacturing: a sur-
vey. International Journal of Production Research,
46(10):2707–2742.
Poupyrev, I., Tan, D., Billinghurst, M., Kato, H., Regen-
brecht, H., and Tetsutani, N. (2001). Tiles: A mixed
reality authoring interface. In Proceedings of Con-
ference on Human-Computer Interaction (INTERACT
’01), pages 334–341.
Sang-Cheol, P., Sung-Hoon, L., Bong-Kee, S., and Seong-
Whan, L. (2005). Tracking non-rigid objects using
probabilistic hausdorff distance matching. Pattern
Recognition, 38(12):2373–2384.
Santos, E. S., Lamounier, E. A., and Cardoso, A. (2011).
Interaction in augmented reality environments using
kinect. In Proceedings of the 2011 XIII Symposium on
Virtual Reality, SVR ’11, pages 112–121, Washing-
ton, DC, USA. IEEE Computer Society.
Schmalstieg, D. (2005). Rapid prototyping of augmented
reality applications with the studierstube framework.
In In Proceedings of the Workshop of Industrial Aug-
mented Reality (IAR), IEEE/ACM International Sym-
posium on Mixed and Augmented Reality (ISMAR05).
Schwald, B., Laval, B. D., Sa, T. O., and Guynemer, R.
(2003). An augmented reality system for training and
assistance to maintenance in the industrial context. In
In Proceedings of 11th International Conference in
Central Europe on Computer Graphics, Visualization
and Computer Vision, pages 425–432.
Seichter, H., Looser, J., and Billinghurst, M. (2008). Com-
posar: An intuitive tool for authoring ar applica-
tions. In In Proceedings of the IEEE/ACM Interna-
tional Symposium on Mixed and Augmented Reality
(ISMAR08), pages 177–178.
Seo, J. and OhM, S. (2007). Pvot: An interactive author-
ing tool for virtual reality. International Journal of
Computer Science and Network Security (IJCSNS),
7(4):17–26.
Traskback, M., Koskinen, T., and Nieminenl, M. (2003).
User-centred evaluation criteria for a mixed reality au-
thoring application. In Proc. of Tenth International
Conference on Human-Computer Interaction (HCI),
pages 1263–1267.
Wagner, D. and Schmalstieg, D. (2007). Artoolkitplus for
pose tracking on mobile devices. In Proceedings of
12th Computer Vision Winter Workshop (CVWW’07),
pages 139–146.
Wang, M., Tseng, C., and Shen, C. (2010). An easy to
use augmented reality authoring tool for use in ex-
amination purpose. Human-Computer Interaction,
332:285–288.
GRAPP 2012 - International Conference on Computer Graphics Theory and Applications
386