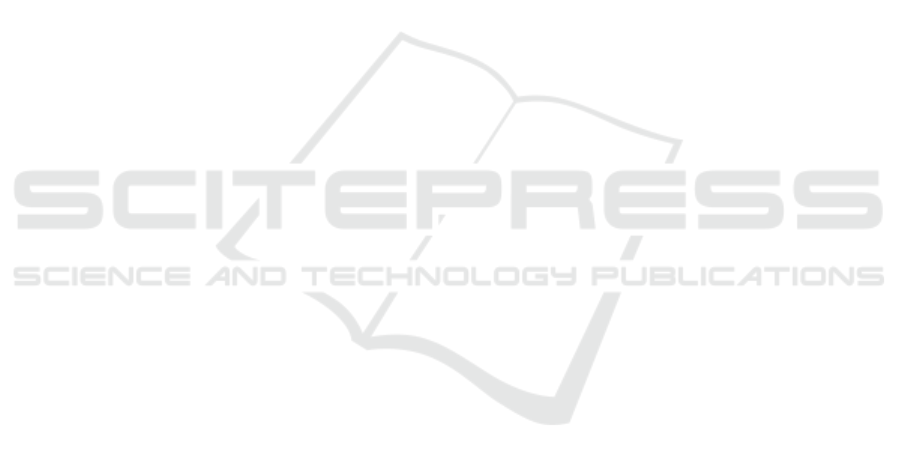
FROM TRIANGULATION TO SIMPLEX MESH AND VICE-VERSA
A Simple and Efficient Conversion
Francisco J. Galdames
1,3
and Fabrice Jaillet
2,3
1
Department of Electrical Engineering, Universidad de Chile, Av. Tupper 2007, Santiago, Chile
2
Universit
´
e de Lyon, IUT Lyon 1, Computer Science Department, F-01000, Lyon, France
3
Universit
´
e de Lyon, CNRS, Universit
´
e Lyon 1, LIRIS, SAARA team, UMR5205, F-69622, Lyon, France
Keywords:
Simplex Mesh, Triangle Mesh, Optimized Surface Interpolation, Surface Mesh Conversion.
Abstract:
We propose an accurate method to convert from a triangular mesh model to a simplex mesh and vice-versa. For
this, we are taking advantage of the fact that they are topologically duals, turning it into a natural swap between
these two models. Unfortunately, they are not geometrically equivalents, leading to loss of information and
to geometry deterioration when performing the conversion. Therefore, optimal positions of the vertices in
the dual mesh have to be found while avoiding shape degradation. An accurate and effective transformation
technique is described in this paper, where we present a direct method to perform an appropriate interpolation
of a simplex mesh to obtain its dual, and/or vice-versa. Our method is based on the distance minimization
between the local tangent planes of the mesh and vertices of each face.
1 INTRODUCTION
Deformable model techniques are widely used in
image segmentation tasks. Among these models,
simplex meshes are valuable candidates (Delingette,
1999), for their favorable characteristics in this type
of modeling, as its convenient way to model inter-
nal forces. With this type of meshes, as with trian-
gulations, any topology can be described. Triangu-
lations are meshes of triangles in which, if they are
manifolds, each triangle has three neighboring trian-
gles, while simplex meshes are meshes of polygons
in which each vertex has three neighboring vertices.
Simplex meshes and triangulations are topologically
duals (Delingette, 1999), and this allows us to natu-
rally obtain a simplex mesh by applying a dual oper-
ation to the triangulation, and vice-versa. Moreover,
there are some tasks for which simplex meshes are
not suitable, and thus triangulated meshes are more
adapted. Examples of these applications are: genera-
tion of volumetric meshes, rendering and calculation
of area.
Currently, the most common way to perform con-
versions between triangulations and simplex meshes
is to determine the set of vertices for the final mesh
as the gravity center of each face of the initial
mesh (e.g. (The Insight Segmentation and Registra-
tion Toolkit (ITK), 2011)). This technique is fast, but
unfortunately in this case, mesh smoothing is gener-
ally high; original shape (curvature) and volume is not
properly respected. In (De Putter et al., 2006), an it-
erative curvature correction algorithm for the dual tri-
angulation of a two-simplex mesh is proposed. Their
solution provides optimal error distribution between
the two dual surfaces while preserving the geometry
of the mesh, but at the price of an iterative global min-
imization over the whole meshes.
In this paper, a new technique is presented, achiev-
ing reasonable computation cost and minimal loss of
geometric information. From a geometric point of
view, the problem can be reduced to finding an in-
terpolation of the center of each face, and to build
the dual mesh accordingly to these points. We pro-
pose to use a geometric interpolation, based on the
distance to the tangent planes of the vertices of each
face. A similar measure has been successfully used
in (Ronfard and Rossignac, 1996) to perform trian-
gular mesh simplifications. Another equivalent mea-
sure has been employed, using this time a summation
to obtain a quadratic error in (Garland and Heckbert,
1997; Heckbert and Garland, 1999). In a more recent
work, a method for refining triangulations has been
developed (Yang, 2005) using a similar measure. It
is worth pointing out that our global objective is to
perform a transformation between meshes, and not to
refine them. However, we mainly got inspiration from
151
J. Galdames F. and Jaillet F..
FROM TRIANGULATION TO SIMPLEX MESH AND VICE-VERSA - A Simple and Efficient Conversion.
DOI: 10.5220/0003851801510156
In Proceedings of the International Conference on Computer Graphics Theory and Applications (GRAPP-2012), pages 151-156
ISBN: 978-989-8565-02-0
Copyright
c
2012 SCITEPRESS (Science and Technology Publications, Lda.)