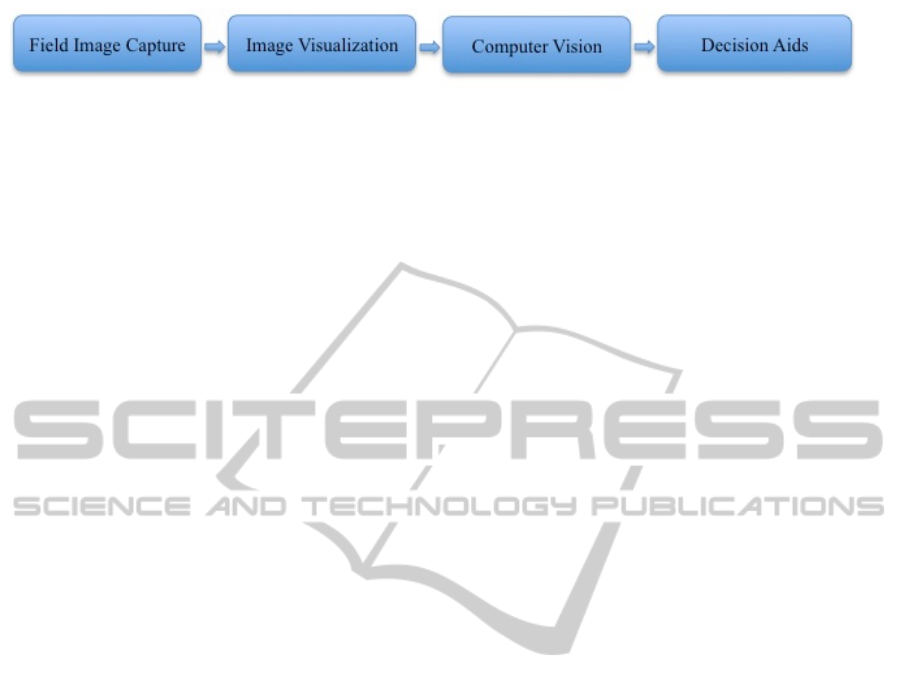
Figure 2: The proposed bridge inspection framework pipeline.
inspection could be requested using alternative sens-
ing modalities (e.g., ultrasound, infrared, etc.), and so
on.
3 METHODOLOGY
Figure 2 shows the key components of the cap-
ture/visualization pipeline that must be developed in
order to realize the proposed inspection framework.
The following subsections describe in further detail
the approaches to be used in addressing the techni-
cal challenges associated with each component of this
pipeline, and the anticipated outcomes.
3.1 Image Capture Methods
Upgrades to traditional methods of in-the-field image
capture (inspection teams with cameras) are being ex-
plored alongside the use of automated, robotics-based
capture. The challenge in the traditional case is to
develop a user input data-logging technique paired
with a combination of computer vision techniques to
extract location and orientation data from the cap-
tured images so they can be properly integrated into
an overall geometric context. For the complex ge-
ometries common in bridges, this is a challenging
task, especially when combined with the variability
in human-driven capture.
Similar geometric challenges arise in the case of
robotics-based image capture, but there are more op-
portunities for precise control and repeatability on the
capture front-end. By design, robotic devices can
track their position, camera orientations, and viewing
angles with high precision, allowing for precise data
logging and repeatable imaging, effectively skirting
the key difficulty of the inspector focused approach.
Furthermore, such mobile systems can quickly and
unobtrusively access structural elements that are diffi-
cult or impossible for human inspectors to view with-
out significant disruption to traffic and risk to the
safety of the inspectors. Combined with the funda-
mental advantages of automation, the robotics-based
approach is particularly compelling, but this raises the
question as to why it is not being used currently.
In looking at prior robotic bridge inspection work,
it can be seen that over the last decade researchers
have developed several chassis designed for bridge in-
spection (Choset, 2000; Huston et al., 2003). A com-
mon focus of this work has been on developing mech-
anisms for traversing arbitrary bridge geometries us-
ing approaches such as magnets, suction, and other
climbing technologies (Mazumdar and Asada, 2009).
These systems have been developed in an attempt to
create a “one size fits all” robot that can inspect al-
most any bridge type currently in service. In all but
one case, these have been proof-of-concept robotics
projects which have at no point actually carried a sen-
sor or vision package in actual field testing.
Our approach is to use a simple and inexpensive
mobile platform, with an emphasis on creating modu-
lar robotic systems designed for use on specific struc-
tural systems. Specializing to specific structure types
and applications yields significant time and cost sav-
ings over general mobile platforms designed to in-
spect any and all structure types. Even in more gen-
eral contexts the mechatronic systems required for a
specific application can be substantially simpler and
cheaper than a machine designed for a more general
set of criteria. This specificity allows for smaller in-
spection devices that can pass through smaller spaces,
inspect portions of structures that would be inaccessi-
ble to larger multi-purpose inspection equipment, and
more easily navigate the details of bridge structures.
Developing an inspection system around a series of
smaller, specific mobile machines could also eventu-
ally lead to a modular platform where various mecha-
tronic, sensing, and data processing packages would
be interchangeable based on the demands of a given
bridge inspection environment. Lastly, the use of sim-
pler robotic systems has a significant and positive im-
pact on manufacturing costs, and may mean the differ-
ence between the ubiquitous use of inspection robots
and their dismissal as impractical.
The robotic test platform enables the investiga-
tion of both visual and other modes of inspection
data not currently available through static sensor net-
works. The prototype robot, designed for use in labo-
ratory testing situations (Figure 3), contains a sensor
array that includes the digital imaging system, ther-
mal sensors, tilt sensors, and accelerometers. All of
these sensors are lightweight, low power, small, and
easily incorporated into the mobile robotics platform.
The combination of sensing paradigms affords an op-
portunity to explore the association between general
sensing and imaging data, and is lending significant
insight into our understanding of how visually ob-
A COMPUTATIONAL FRAMEWORK FOR NEXT-GENERATION BRIDGE IMAGING AND INSPECTION
727