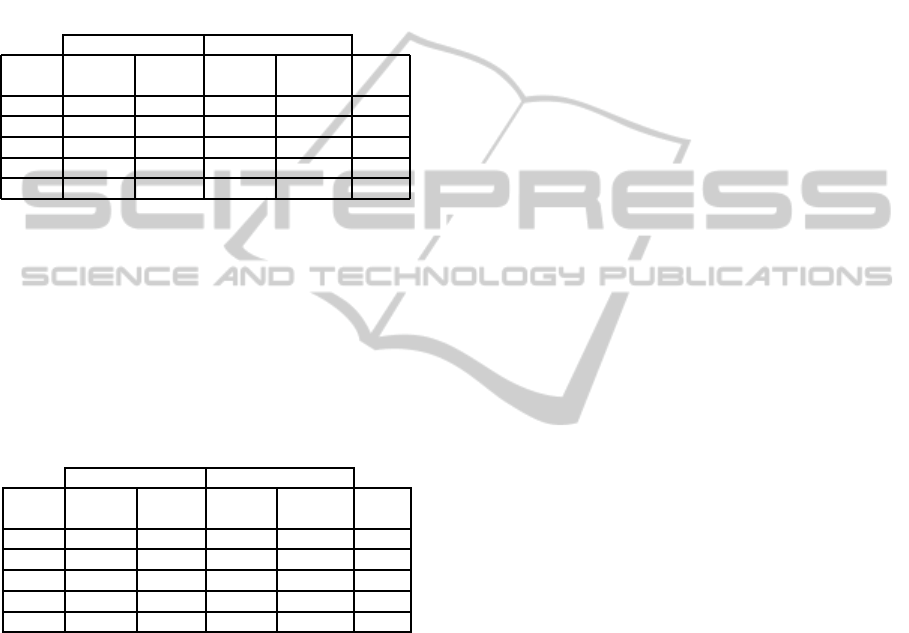
The best results are described by numbers in bold.
The DPA method performed better when the reliabil-
ity constraints were tighter.
After that, we haveincreased the number of equip-
ments, trying to show the robustness of the DPA
method for cases where the optimisation procedure
is more complex. We have created an instance with
300 equipments. The Table 2 illustrates the optimal
results obtained for this instance:
Table 2: Results - Instance with 300 equipments.
DPA DSA
Cost Time Cost Time Profit
SAIFI (x 1000) (s) (x 1000) (s) (%)
2.9757 80.498 11.528 107.627 290.825 25.20
3.2543 53.466 52.244 54.908 250.846 2.61
3.5330 33.562 124.738 35.879 1295.747 6.45
3.8117 24.962 242.035 26.664 1681.954 6.38
4.4068 19.169 398.083 22.214 231.554 13.70
The DPA method performed better in all cases and
the computational time is better in all except one case.
These results show the efficiency of the approach in
cases with a larger number of equipments.
Following this idea, we have created an instance
with 400 equipments. The idea was to show the
growth of computational time. In the Table 3 we can
see the results for this instance.
Table 3: Results - Instance with 400 equipments.
DPA DSA
Cost Time Cost Time Profit
SAIFI (x 1000) (s) (x 1000) (s) (%)
3.9625 106.270 25.755 142.048 7258.345 25.18
4.3336 70.830 111.821 72.987 705.412 2.95
4.7046 44.351 255.748 47.611 2240.451 6.84
5.0757 33.111 446.880 38.455 1290.745 13.89
5.4468 24.437 712.909 28.601 5070.507 14.55
The performance obtained in this case is similar
with the previous results, but the computational time
obtained by DPA method is much lower.
6 DISCUSSION
We have done case studies in order to make a compar-
ison between dynamic programming approach and a
heuristic method.
Three examples of networks were executed using
the radial network mentioned. One of them was cre-
ated with a reduced number of equipments and two of
them with a large number of equipments.
The DPA method got a cost profit in all instance
where the reliability constraints were tighter, taking
up to 25% profit in large instances cases.
In instances with a small number of equipments,
the heuristic method got the best results for compu-
tational time and obtained the same results when the
reliability constraints were looser. However, when the
number of equipments increased the computational
time of the heuristic method was much greater than
the DPA method.
For two-years of planning horizon the results were
promising as well, however the algorithm has in-
creased its computational resources since the bell-
man’s principle leads to a combinatorial explosion of
the problem (Bellman, 2003). For this reason, we
have done some approximations of parameters into
the procedure. In some cases, these approximations
lead the algorithm to produce a non-optimal solution.
However, some alternatives could be studied to
apply this approach, trying to reduce the complexity
and the computational time for this problem. With
these approximations, the dynamic programming still
provide good quality solutions, although it may lose
the optimality guarantee.
7 CONCLUSIONS
We have developed a knapsack problem approach us-
ing dynamic programming for the problem of pre-
ventive maintenance on power distribution networks.
The approach was studied for one and two years of
planning horizon and its optimisation model for knap-
sack problem adapted was presented.
Cases studies were conducted followed by a dis-
cussion about the results obtained for three examples
of radial networks developed.
The results obtainedby dynamic programmingap-
proach were promising in relation to a presented heur-
istic method. In all cases the approach had a better
performance, but the best results of cost and compu-
tational time were obtained when the reliability con-
straints were tighter and the number of equipments
larger.
A discussion was produced from the case stud-
ies. The results were analysed proving the robustness
of the approach. Besides, results for more than one
year of planning horizon were discussed, highlighting
some alternatives for the problem complexity.
ACKNOWLEDGEMENTS
This work has been supporting by CNPq and CAPES.
A KNAPSACK PROBLEM APPROACH FOR OPTIMAL ALLOCATION OF MAINTENANCE RESOURCES ON
ELECTRIC POWER DISTRIBUTION NETWORKS
465