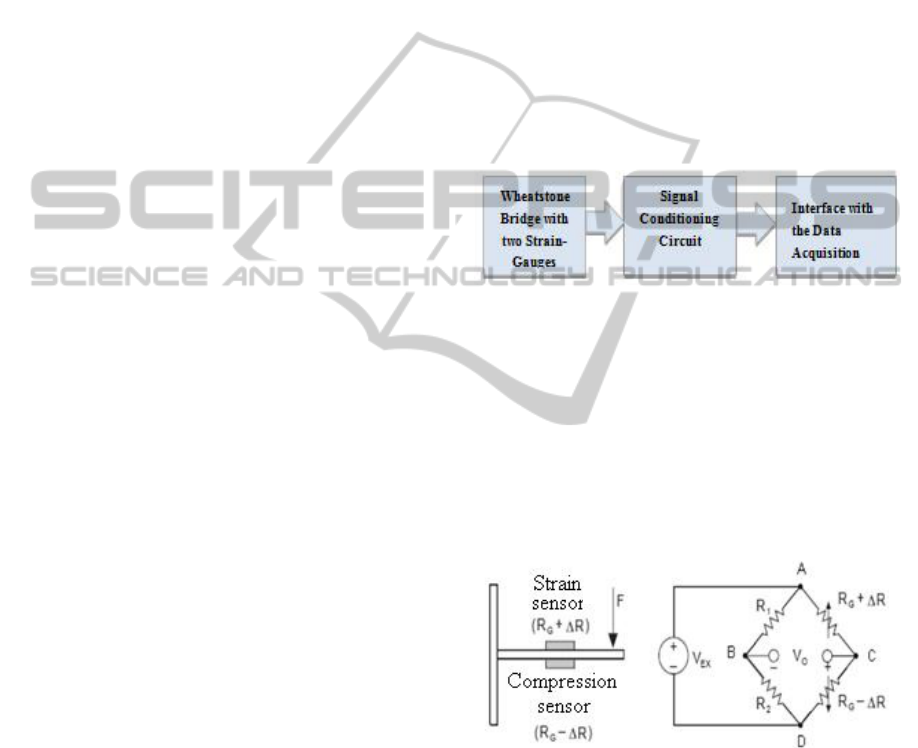
the sending of data to DAQ (Data Acquisition)
devices. The main task of a DAQ system is
to
measure and to generate real physical signals, it
means that the data acquisition system finality is to
gather information from the real world in order to
generate data that can be manipulated in a computer
or micro-processed system. So, the platform of
experiments is composed of several sensors and
actuators to convert the physical signal into an
electric signal, such as voltage or electric current,
which can be monitored and controlled via the data
acquisition board.
Besides all these advantages, to facilitate the
study of experiments, increase the iteration of
the student with the teacher and the learning,
LabVIEW allows experiments to be accessed
remotely. Thus, a site was created, and to have
access to the experiments, LabVIEW must be
configured as a server, and the student must have
the software installed on the machine, thus
performing the monitoring.
For the proposed work, we utilized the National
Instruments data acquisition system, the NI-USB
6210 (National Instruments, 2007), which is
connected with the computer via USB (Universal
Serial Bus) inputs. The NI-USB 6210 possesses 16
analogical inputs, 4 digital inputs, 4 digital outputs,
two 32-bits controllers/temporizers and a frequency
generator.
3 EXPERIMENTS
The experiments are presented in this section
describing the greatness of each one, as regards the
sensor and the actuator being employed; to describe
the experiment itself; to show the electronic circuit
used; to expose the block diagram and the interface
created in the LabVIEW.
3.1 Experiment 1: Strain Gauge
Use the Strain-Gauge to measure the deformation of
an aluminum bar, caused by the placing of weights
on its edge.
3.1.1 Strain-Gauge
The electric resistance extension-meter, also known
as strain gauge, is a small frame made of thin
metallic blades that can be glued to the surface of a
component or structure to measure its deformations.
The thin layer of sticking-plaster used serves to
transmit the structure deformations to the strain
gauge, also serving as isolation between the two.
This instrument changes little structure dimension
variations into equivalent variations of its electric
resistance, so being considered like a transducer
(Fraden, 1993).
Extension-meters are used in the experimental
analyses of deformations in machines, bridges,
locomotives, vessels and in the construction of
transducers of strength, tension, pressure, flux,
acceleration, among others.
The representation of the Strain-Gauge Platform
of Experiments, in block diagram, is shown in
Figure 1.
This platform contains an aluminum bar,
horizontally fixed by a support. Two identical
extension-meters are stick-plastered to the bar, with
one on the upper part and the other on the lower one.
Figure 1: Blocks Diagram of Strain-Gauge Platform.
To measure the deformation caused by a force on
the bar, the extension-meters are connected to a
Wheatstone bridge, as shown in Figure 2. The bridge
is completed with two pressure resistors with equal
resistance. This configuration is called “½ bridge”
because there are two active elements (extension-
meters). Other configurations used are the “¼
bridge” and the “full bridge”, with one and four
active elements, respectively.
Figure 2: Electric diagram of Wheatstone bridge with two
extension-meters.
The way how the extension-meters are
positioned on the bar allow them to undergo
opposite deformations. Therefore, the resistances
will suffer the same alterations, further to
minimizing the effects of temperature, as the
temperature variations will be made sensitive by the
resistive frames of the extension-meters. Thus, are
presented the equations (1 - 4):
CSEDU2012-4thInternationalConferenceonComputerSupportedEducation
424