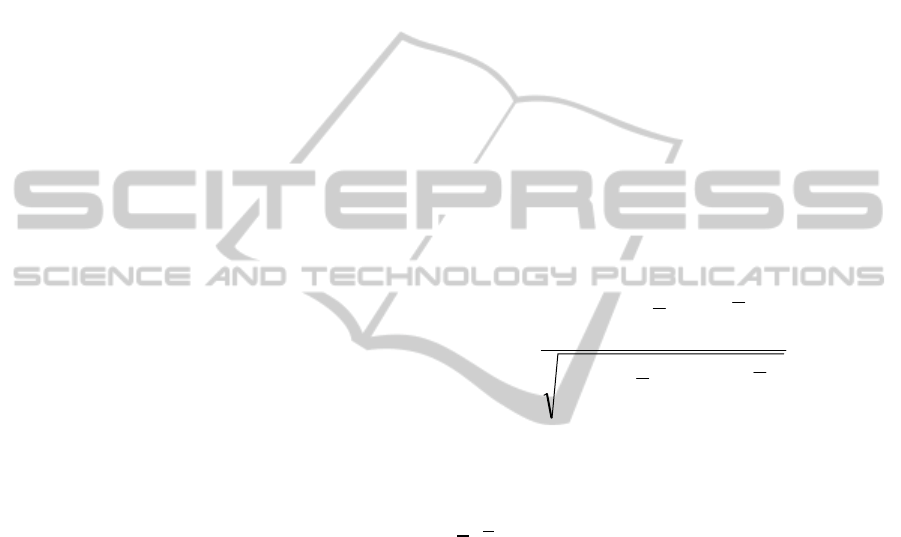
channels red, green and blue) were used for the
calculations. The relative position of both cameras to
each other is assumed to be constant during the
measurement. The movement of the whole camera
head is represented by a 4x4 homogeneous
transformation matrix for each line. A linear model
to calculate the motion of the 4x4 transformation
matrix of each image line is used for the application
of the camera head combined with a linear unit.
This approach allows great flexibility, both in
describing the optical properties of the cameras as
well as in modelling the trajectories of the camera
head. On the other hand it gives rise to two new
problems. The calculation of the projection of a
point in space in the line scan camera system
(function "World2Pix") is complicated. Secondly,
the number of camera parameters is comparatively
high and the determination in the part of a
calibration is possible only under the assumption of
additional boundary conditions. A precise
calculation of each individual camera parameter is
not required in practice, if consistency of all
parameters of the whole system can be achieved.
One possible strategy, for example, is not to
introduce all parameters simultaneously into the
equation system, but gradually, respectively
alternately.
The calibration is done by recording an
optimized calibration body from several directions.
Twenty-eight-coded circuit marks are printed on the
calibration chart. Three of them are positioned on a
raised stamp. The hierarchical search for the circle
marks starts in a lower resolution. After finding the
brand position of the marks, the precise re-
measurement is performing with original resolution.
(0.02 pixels accuracy possible). The search is
performed separately in each color channel, because
in a trilinear line camera, the color channels do not
overlap. Thus a much larger number of observations
can be generated. From those measurements we
determine the parameters of interior and exterior
orientation of the cameras and some parameters of
the movement of the camera head by linearization
(numerical differentials) and compensation
calculation iteratively. Good initial values are
necessary for determining the system parameters,
which can be extracted from the CAD data (Calow
and Ilchev, 2010).
5 CORRELATION METHOD
The three lines of trilinear color line scan cameras
record an object point in time one after the other,
resulting in a misalignment between the three color
channels of the raw images. This offset is visible as
colored edges on light-dark transitions. The size of
the offset depends on the ratio of speed to the line
frequency. Given a known trajectory, the scan offset
is calculable from the calibration data, and can be
directly corrected by re-sampling of the three color
channels. Thus re-sampling ensures that
corresponding points between the left and right
camera are almost in a row (rectification), so that the
search for corresponding points in only one line (one
dimension) must be done. In order to perform
rectification efficiently, the necessary sample points
are calculated using the offline calibration data, and
are then pre-stored in tables. For noise reduction and
a simultaneous reduction of the search effort for the
correlation, only gray-scale images from the average
of all three color channels are used. Due to very
good experience in terms of accuracy, contrast and
illumination invariance, the normalized cross-
correlation coefficient (5.1) was used as similarity
criterion (Calow and Ilchev, 2010).
()
()
[]
()
()
∑∑
∑
==
=
−⋅−
−⋅−
=
N
i
i
N
i
i
N
i
ii
bbaa
bbaa
k
1
2
1
2
1
(5.1)
N – Number of pixels of the image block to be
compared
a
i
, b
i
- Gray values of one and the other camera
image
ܽ
, ܾ – Mean values of one and the other camera
image
For each pixel position of the maximum cross-
correlation quotient the observed disparity on this
position will be saved. The data is stored in a ring
buffer, so that it can be accessed not only on the
maximum correlation, but also on the correlation
values of the previous and successor disparity.
Correlation maximum from his predecessors and
successors can help to achieve sub-pixel accuracy by
fitting a parabola, if the surface gradients (relative to
the receiving direction) are small (Mecke, 1999).
6 EXAMPLES
Some objects scanned with the measurement setup
are shown below. The examples have enough texture
so that the correlation of the stereo image provides a
unique result. Initial investigations of the
A STEREO LINE SENSOR SYSTEM TO HIGH SPEED CAPTURING OF SURFACES IN COLOR AND 3D SHAPE
811