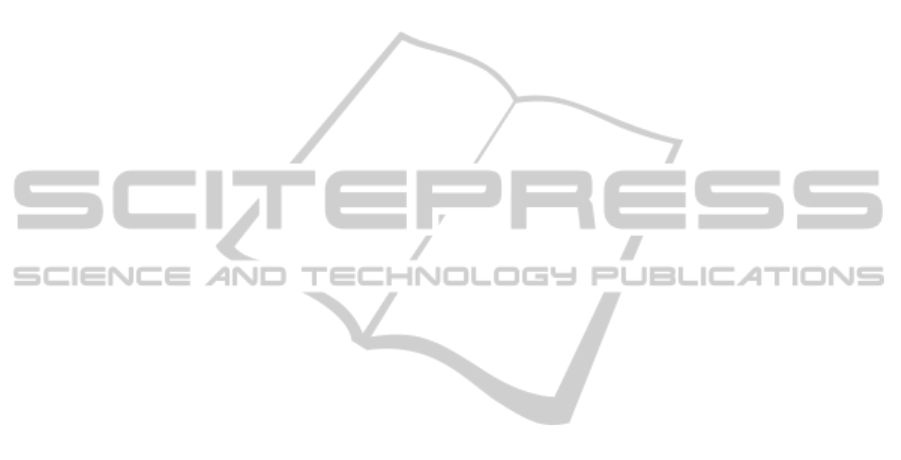
problem has been receiving attention of researchers
since it has been first identified by Capacho &
Pastor (2005), However, all of the researchers
considered only single model with serial lines such
as Capacho & Pastor (2006, 2008), and Scholl et al.
(2009). In this study, we considered U-shaped
assembly line balancing models with alternative
subassembly graphs (uALB/sb). The problem under
consideration contains two kinds of special issues,
i.e. the selection of a suitable subassembly graph
among alternatives and the balancing according to
the operational precedence constrained among the
tasks in the selected subassembly graph.
Traditionally to solve these kinds of u-ALB/sb
problems, researchers first tries to identify the best
alternative in the form of one precedence diagram
and finally balance this problem using only this
precedence diagram. However, most of the time,
researchers are giving the utmost importance to the
balancing rather than the selection of alternatives.
Particularly, the disjunctive relationship between
these two problems is often neglected and they are
solved separately in a hierarchical manner.
Nevertheless, by using the traditional hierarchical
approach, the u-ALB/sb problem can lose its
integrity since the researchers are eliminating some
features of the whole problem before balancing
procedure.
To maintain the integrity of the u-ALB/sb
problem, in this study, an integrated monolithic
approach, which considers selection together with
balancing, is proposed. Particularly, a multi-stage
decision based genetic algorithm (mdGA) approach
is constructed in order to consider it as an exclusive
problem while using a specific decoding procedure.
The rest of the paper is organized as follows; In
Section 2, the background information on the main
features of u-ALB/sb are introduced. In Section 3,
overall methodology of the proposed mdGA
approach and its general features are discussed in
detail. In Section 4, in order to evaluate the
performance, the proposed mdGA approach is
demonstrated on some problem instances, and the
experimental results are analyzed. Finally, the
concluding remarks and future research directions
are given in the last section.
2 BALANCING U-SHAPED
ASSEMBLY LINES WITH
ALTERNATIVE SUBASSEMBLY
GRAPHS
The assembly line balancing problems are usually
represented with precedence relations, which can be
transformed into a more visual form as precedence
diagrams. Precedence diagrams only model
conjunctions (AND relations), not disjunctions (OR
relations). However, in real-life, we usually come
across assembly line balancing problems with
alternative subassembly graphs. In this section, we
considered uALB models with alternative
subassembly graphs (uALB/sb). The uALB is a
generalization of assembly line balancing problems
and hence belongs to the class of NP-hard problems.
Hence its decision version uALB/sb is NP-complete.
As a disjunctive network optimization problem, in
uALB, each subassembly graph represents
subassembly, which is the alternative way for
performing a subset of task or tasks and each node
represents the tasks of a subassembly. The uALB/sb
model consists of i=0,1,…, I+1 subassemblies and
the precedence relations between each subassembly
are taken into consideration according to the
network structure. In each subassembly i, there are
k=0,1,…, K+1 alternative ways to perform that
subassembly. Fig.1 illustrates the conceptual
network for assembly line balancing problem with
alternative subassembly graphs.
In each alternative subassembly k, there are
j=0,1,…, J+1 tasks with precedence relations, where
p
ikj
denotes the variable processing time of task j in
alternative k of subassembly i. Particularly, the
detailed concepts of subassembly graphs and task
are given in Fig.2. In this model, the activities are
interrelated by two kinds of constraints; the
precedence constraints which are known from
traditional uALB, force a task no to be started before
all its predecessors have been finished and the new
constraints force a subassembly no to be started
before all its predecessors have been finished.
Specifically, the uALB/sb model considered in
this study can be defined by the following
assumptions:
A1. The problem consists of multiple
subassemblies.
A2. There exists alternative ways to perform
each subassembly.
A3. Each subassembly alternative contains
number of tasks with known processing
time
A4. The assembly line is used to assemble
one homogeneous product in mass
quantities.
A5. The line is U-shaped, paced line with
fixed cycle time and there are no feeder
lines.
MULTI-STAGE DECISION BASED APPROACH FOR BALANCING BI-OBJECTIVE U-SHAPED ASSEMBLY
LINES WITH ALTERNATIVE SUBASSEMBLY GRAPHS
335