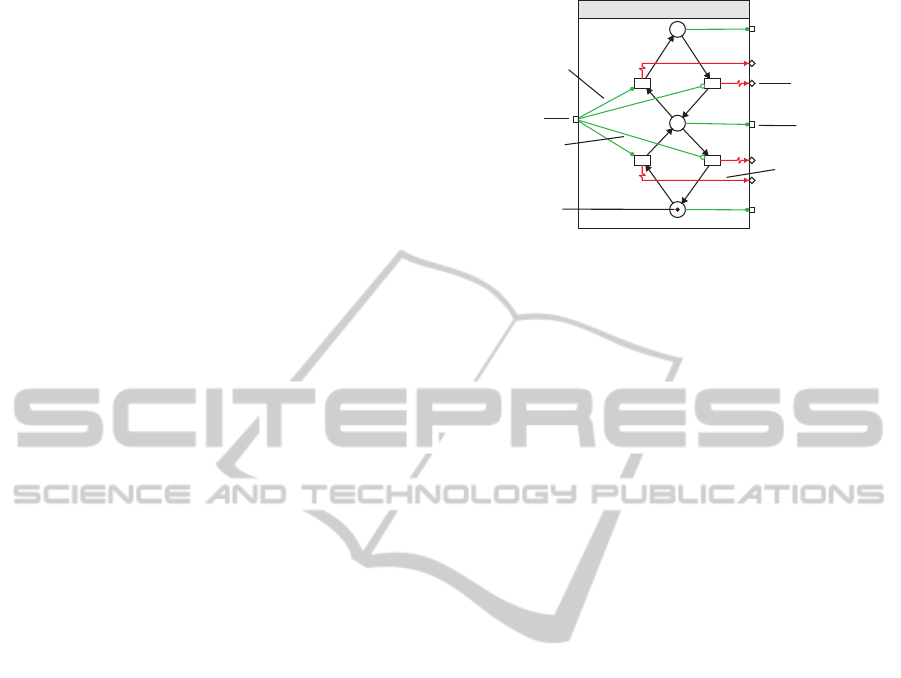
properties called siphons and mixed integer program-
ming.
Iordache and Antsaklis gave a survey (Iordache
and Antsaklis, 2006) over Supervision based on Place
Invariants (SBPI). There, also structrual properties of
PN, namely place invariants, are used to generate a
supervisor.
Another structure-based approach was introduced
by Missal and Hanisch, (Missal and Hanisch, 2008a)
and (Missal and Hanisch, 2008b). They analyze the
pre-regions of forbidden states in plant model’s state
space, to synthesize distributed control. This work
takes advantage of a modular modelling formalism,
the so-called Net Condition/Event Systems (NCES),
which have extensions of PN as building blocks.
To reduce complexity during supervisor synthesis,
different techniques are used, amongst others, model
reduction (Uzam and Wonham, 2006), model abstrac-
tion (Feng et al., 2009) or utilization of model struc-
ture properties and mathematical model representa-
tion (Iordache and Antsaklis, 2006).
The approach presented in this contribution is
about synthesizing distributed controllers on shop-
floor level. It extends commonly used specifications
in terms of states by specifications of desired recur-
ring process behavior. A lossless abstraction of the
plant model structure is generated. This so-called
Transition Invariants Graph (TIG) is utilized to ex-
tract admissible (in the sense of the specification)
causal dependencies from the plant model. Based on
both kinds of specifications and the extracted causal
dependencies, an admissible subspace of the whole
reachable state space is computed. The boundaries
of this subspace are the starting points for determin-
ing a controller model. Hence, the controller model
is determined for meaningful behavior regarding the
specifications. The reduction of complexity is in the
partial computation of the state space, which is there-
fore called partial reachability analysis.
This contribution is structured as follows. Section
2 introduces the used modular modeling formalism.
The steps of the process control synthesis procedure
are presented in Section 3. An example is presented
in Section 4, followed by the conclusions.
2 MODELING
For DES and specification modeling,
S
NCES are used,
a 1-bounded (and therefore called safe) subclass of
Net Condition/Event Systems, which were introduced
in (Hanisch and Rausch, 1995). The crucial advan-
tage of
S
NCES is the modular model structure. Rec-
ommendations for a well-formed modular plant mod-
NameofModule
p51
p52
t62
t63
t64
t65
p50
eventarc
initialmarking
conditionarc
inhibitor arc
conditioninput
conditionouput
eventouput
Figure 2: Example of a safe Net Condition/Event System ba-
sic module.
eling with
S
NCES are given in (Missal and Hanisch,
2008a).
S
NCES allow to model the behavior of
plant components encapsulated in reusable modules.
Modules are interconnected via signal arcs. Thus,
S
NCES offer a natural way to model even large-scale
systems, regarding their composition of basic compo-
nents and groups of components.
2.1 The
S
NCES Model
Two kinds of modules are defined within
S
NCES. The
first kind are basic modules. They are supposed for
modeling basic plant components (e.g. cylinders, sen-
sors, etc). The second kind are composite modules,
which are composed of basic modules and/or other
composite modules. Figure 2 shows a basic module,
which is also part of the example in Section 4. It rep-
resents the behavior of a cylinder. Figure 3 shows ex-
emplarily a composite module, which is composed of
basic modules. Amongst others, it contains the basic
module depicted in Figure 2. The composite module
represents the component group for a cylinder, con-
sisting of the basic plant components actuator, cylin-
der and end positions sensors.
For more formal details about
S
NCES see
(Hanisch and Rausch, 1995), (Pinzon et al., 2004) and
(Missal and Hanisch, 2008a). Some fundamental def-
initions are given in the following.
Definition 1. A basic module M
B
is a tuple:
S
NCEM = {P,T, F,CN,EN,C
in
,
E
in
,C
out
,E
out
,CI
arc
,EI
arc
,CO
arc
,EO
arc
,em,m
0
}
where: P, T, F are (common to PN) sets of places,
transitions and ordinary arcs,
CN ⊆ P × T , EN ⊆ T × T
are the sets of condition and event signals,
C
in
, E
in
, E
out
, C
out
are the sets of signal in-/outputs,
CI
arc
⊆ C
in
× T , EI
arc
⊆ E
in
× T
are the sets of condition and event input arcs,
PECCS 2012 - International Conference on Pervasive and Embedded Computing and Communication Systems
344