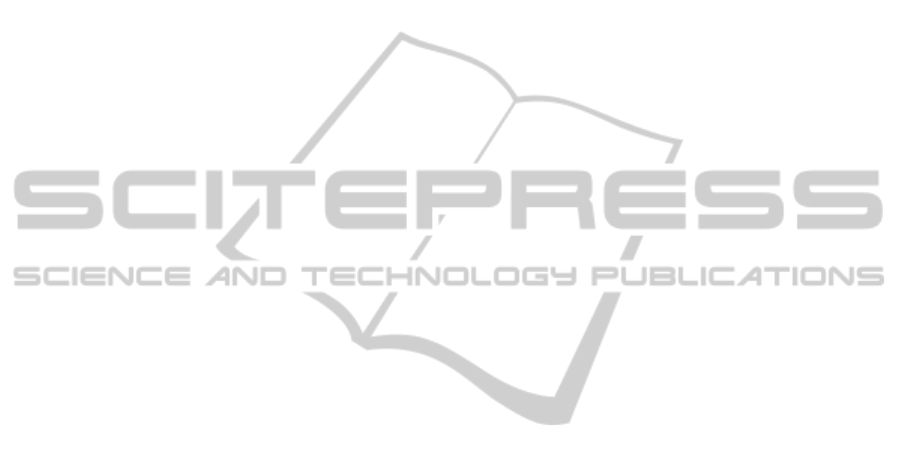
any productive process. All equipments are
commanded via the CLP.
2.2 Manual Mode
In order to characterize the manual mode, only is
needed to have selected on the HMI or in the SOS
(system operating station), the operation from
CABIN or CONTROL ROOM and, additionally,
have been selected the MANUAL mode. The
signaling will be through MANUAL OPERATING
ROOM or MANUAL CABIN written on the
operating screen.
The reclaiming will be under the command of
the operator through the usage of the levers at the
console. In this mode also the security and process
interlocks are respected, disallowing start them out
of sequence.
The translation movement will not revert
automatically and, the material reclaiming can be
done in any area of the stock yar d as long as the
operator detects it available.
The equipments will be commanded individually
via CLP, as long as the yard’s conveyor belt is on
(Start Conveyor of Spear and Start Bucket Wheel)
2.3 Semi-Automatic Mode
In this operating mode, the operator establish the
parameters of the process such as initial and final
landmark, set point for the reclaiming flow rate and
the time or distance for advancing and the angles for
the reversal of spear rotation.
Initially, through the rotation lever, the
movement is commanded and reversal points are
marked. The marked points are memorized and after
this marking, every time the rotation angle reaches
these points, there is a reversion of this movement.
Through the operating console it is possible to reset
the information of reversal points previously
defined, allowing a new preset for adjustment of the
reversal point.
In this mode, the backing movement and spear
descent for changing the reclaiming stand are done
manually, being necessary reinitiate de reclaiming
process, marking new reversal points for the spear
rotation.
The rotation speed is controlled through a PID
control loop and the time for the translation step is
determined by the operator as well as may be
adjusted automatically by a logic developed on the
CLP.
In order to preserve the flow measurement
without the interference of the material’s impact that
is being reclaimed to the spear conveyor belt, the
scale is mounted a reasonable distance from the
bucket wheel, generally in the middle of the spear’s
conveyor belt. This distance of the scale to the
bucket wheel causes an average delay of 10 seconds
and for this reason the flow measured by the scale is
not used as process variable.
3 STANDARD LOGIC FOR FLOW
OPTIMIZATION
The standard logic for flow optimization existing on
TMPM was developed aiming the control of the
following variables:
Rotation speed
Translation step
3.1 Rotation Speed Control
3.1.1 Mathematic Data Modeling
Due to the high elevated delay of the bucket wheel
in relation to the process scale according to figure 2,
which prevents the deployment of a flow control, it
was necessary develop a mathematic model to
estimate the reclaiming flow and eliminate this
delay, known as Dead Time (Smith, 1957; Astrom et
al., 1994; Hagglund, 1992).
Initially was analyzed the correlation of the flow
with the following process variables:
Current or pressure of the bucket wheel.
Current of the rotation engine.
Rotation speed
It was noted the existence of a high correlation
between the reclaiming flow and the current or
pressure of the bucket wheel and low correlation in
regards to the current and speed of the rotation. So,
only the current or pressure of the bucket wheel was
used for estimating the reclaiming flow.
In order to represent mathematically the
estimated reclaiming flow it was used the ARX
linear model which concepts are well demonstrated
in Aguirre (2007) and the extended minimum square
method (Aguirre, 2000) to estimate the parameters.
In order to determine the order of the model the auto
values analysis model, created by Lopes et al.
(2010), was utilized.
ICINCO 2012 - 9th International Conference on Informatics in Control, Automation and Robotics
426