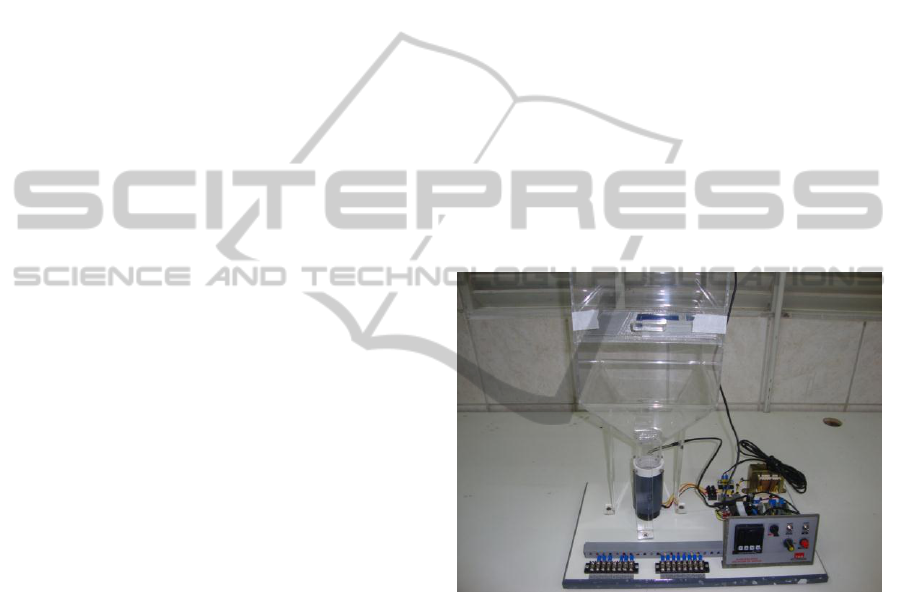
(1985). A possibility is the union of an adaptive
scheme, as the Model Reference Adaptive Control
(MRAC), which determines the desired closed loop
performance, with the nonlinear control technique,
called Variable Structure Systems (VSS), based on
the relay theory (Utkin, 1978). This technique was
named Variable Structure Model Reference
Adaptive Control (VS-MRAC) (Hsu and Costa,
1989) and it guarantees a fast and non oscillatory
transient. Robustness to external disturbances and
unmodeled dynamics was also achieved. Although,
originally, its control signal was switched and with
high frequency, further works were concerned about
its smoothness (Hsu, 1997). Oliveira and Araujo
(2008) developed a VS-MRAC version for the
unitary relative degree based on the indirect
approach of the adaptive control, named IVS-
MRAC, without performance losses and that turns
the controller project itself more intuitive, since the
controller parameters are directly related to the plant
model parameters. Its application on an industrial
environment can be seen in Oliveira et al. (2010).
The general case for the IVS-MRAC was presented
in Fernandes et al. (2010) and it was named Shunt
IVS-MRAC (SIVS-MRAC). It introduces a parallel
compensator to the original plant, and, by this
strategy, the entire system (plant + shunt
compensator) becomes of unitary relative degree,
thus allowing the use of the original IVS-MRAC in
series with a PI controller. In this work, the SIVS-
MRAC is applied (through simulations) on the
temperature control of a mathematical model
obtained from an educational drying grains
prototype. Simulation results in adverse conditions
of external disturbances and parameter variation are
presented and compared to the results of a PID,
tuned to behave as good as possible.
2 PID AND IVS-MRAC
CONTROLLERS
The PID controller provides a control signal to be
applied on the plant from the combination of three
actions, namely, the proportional, integrative and
derivative. Therefore, the project consists in
choosing three tuning parameters: the proportional
gain
, the integral time
and the derivative time
. To adjust these parameters, many methods may
be used, all based on an available model for the plant
and performance requirements, such as settle time or
overshoot. The SIVS-MRAC project makes the
assumption that the plant model has known and
limited uncertainties and it uses switched adaptive
laws which act on these same uncertainties
(Fernandes et al., 2010). A complete theoretical
description and the stability analysis may be found
in Oliveira and Araujo (2008), being the main
objective of this work the computer simulation of
the SIVS-MRAC, when applied to the temperature
control of a drying system.
3 MATERIALS AND METHODS
The drying grains system used in this work (Figure
1) is compound by a garner, a heater and a fan which
blows the air through the garner, where exists a
screened drawer, like a strainer, in which the grains
are deposited, characterizing a fixed-bed drying. The
temperature adjustment is made by an industrial PID
controller, being the temperature on the input and on
the top of the garner obtained from two Pt100
sensors.
Figure 1: Educational kit for drying grains control.
The air flow control is made by a potentiometer, that
acts on the PWM signal generator. The PID output
signal is applied on a Solid State Relay (SSR),
which, by its turn, acts on the electrical resistance of
the heater. Using the graphical method of step
response to get the mathematical model that better
describes the practical system, the air flow was fixed
in 10% and the system was modelled by a first order
transfer function with delay (1), with K=55, T=27
and L=6. For simulation purposes, the delay was
added to (1) and the Pade’s approximation for
exponentials was used in (1), generating
(2).
ICINCO 2012 - 9th International Conference on Informatics in Control, Automation and Robotics
562