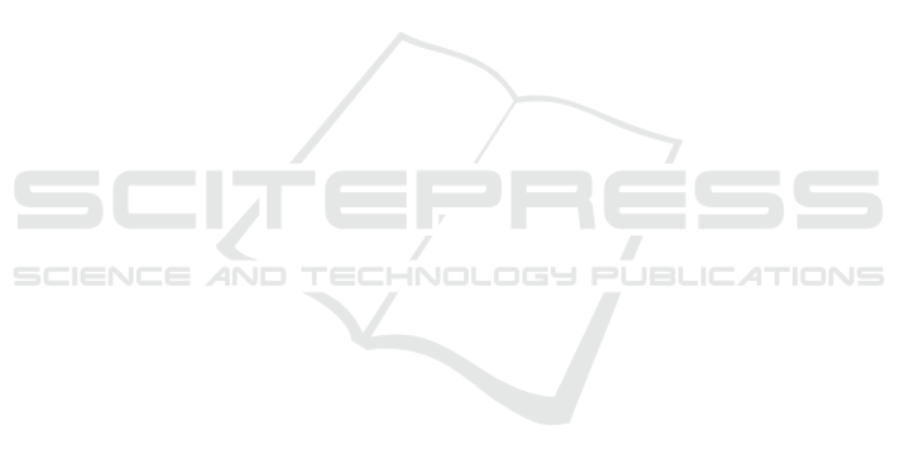
Simulation of Backflow in Automotive Body Assemblies
Jaedeuk Yun
1
, Sunghoon Lee
1
, Jianhui Fu
1
, Jungwoon Lee
1
, Yoongho Jung
1
and Sungbae Park
2
1
School of Mechanical Eng., Pusan National Univ., Busan, 609-735, South Korea
2
Body Manufacturing Eng. Team #3, Hyundai Motor Company, Ulsan, 683-791, South Korea
Keywords: Drainage, Backflow, Octree, Voxel, Gap, CAD.
Abstract: The many parts required for aircraft and automotive development are developed by functional or sectional
design groups for efficiency. Interferences and gaps can be found when the parts and subassemblies from
those design groups are to be assembled. When rainwater enters the spaces between parts and there is not
sufficient drainage, the rainwater within the structure can backflow to gaps or unexpected outlets, which
may cause severe problems of part corrosion and electric shock. We have developed a method and a
program to simulate backflow of rainwater within spaces between automotive parts; the method can find
unexpected outlets and gaps. The developed program can simulate not only simple liquid flows, but also
division and joining of flows with multiple channels. The developed method can also be applied to aircraft
and ship design.
1 INTRODUCTION
Large assemblies such as automobiles, aircraft and
ships have the common characteristic of requiring
huge numbers of parts to be assembled. For such
large assemblies, most developing companies
accelerate the design processes with many design
engineers working concurrently. Concurrent design
with functional or sectional design groups may
reduce development time, but it may cause many
problems of interferences and gaps between parts
that are designed by different designers or design
groups. In particular, gaps between parts can cause
fatal problems of inflow to cabins or other spaces.
Most parts for passenger cars are made of thin
plates to reduce the vehicle weight, and there are
empty spaces between thin parts that are provided to
increase the car body stiffness. If there are gaps
between exterior parts of the car body, rainwater and
water from puddles on roadways can enter the cabin
directly or move through the empty spaces between
body parts. Even though design engineers include
appropriate drainage paths, if the drainage is too
small for fast discharge of the inflow, water may fill
the spaces. This situation may cause corrosion of
interior parts or fatal problems of electric shock and
malfunction if the water enters the electric system.
To check for such problems at the design stage,
designers check gaps between parts in suspect
regions with cross-sectional drawings that are
generated from the assembly model. However, it is
almost impossible for design engineers to check the
gaps of complicated three-dimensional flow paths
with two-dimensional sectional drawings.
To resolve this kind of problem, previous
methods such as searching empty spaces of the
assembly, simulation of fluids (Premoze et al., 2003;
Foster and Metaxas, 1996; Losasso et al., 2004;
Ramaswamy and Kawahara, 1987; Harlow and
Welch, 1965) and mold flow analysis (Broyer et al.,
1975) can be considered. However, those methods
are not adequate for the present purpose, which
requires searching for gaps between parts of
complicated shape and simulating the backflow of
water in the gaps to check whether the backflow
path reaches unwanted places.
We propose a method of searching space
between thin parts of complex shape with free
surfaces automatically to simulate backflow in the
searched space. With the simulation program we
have developed, designers can check the path and
outlet positions of backflows in the design stage, and
can handle the problem of inflow into the cabin by
improving their design before manufacturing.
351
Yun J., Lee S., Fu J., Lee J., Jung Y. and Park S..
Simulation of Backflow in Automotive Body Assemblies.
DOI: 10.5220/0003981903510356
In Proceedings of the 2nd International Conference on Simulation and Modeling Methodologies, Technologies and Applications (SIMULTECH-2012),
pages 351-356
ISBN: 978-989-8565-20-4
Copyright
c
2012 SCITEPRESS (Science and Technology Publications, Lda.)