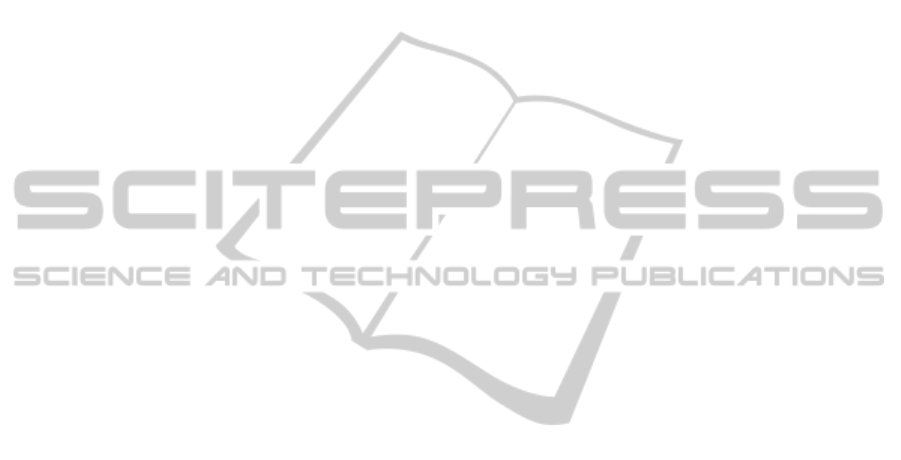
respect to the spinning eccentric flywheel which can
tilt both about X- and Y-axes and whose center of
mass can translate along X-, Y- and Z-axes. The
flywheel, which is assumed as a rigid body, is
connected to the induction motor by a flexible
coupling. The spinning speed of the flywheel is
governed by the induction motor. The intelligent
disc, which is also a rigid body, is equipped beneath
the flywheel with a nominal gap. The universal joint
is employed as the pivot of the intelligent disc such
that the intelligent disc can conduct 3-DOFs
rotations, i.e., yaw, pitch and spin. All the centroids
of the induction motor, the flywheel, the intelligent
disc and the universal joint are aligned vertically
before the flywheel starts to spin. In addition, the
flywheel is eccentric so that the tilting about X- and
Y- axes occurs. Four identical HMAs are located
ninety degrees apart under the intelligent disc to
control its posture. Each individual HMA unit
consists of a Permanent Magnet (PM) and an
Electromagnet (EM) to cooperate to generate a
resultant magnetic force to adjust the posture of the
intelligent disc, as shown in Fig. 2. It is noted that
the merits of employing HMAs, in which the same
wire is wound around the same pair, not only reduce
the number of power amplifiers but also
considerably enhance the system stiffness of the
SGRM. Significantly, adequate system stiffness can
improve the bandwidth such that superior transient
performance and servo capability of gap retaining by
the intelligent disc can be, to some extent, ensured.
On the other hand, four gap sensors, two for the
flywheel and the others for intelligent disc, are used
to acquire the real-time data of tilting of the flywheel
and the intelligent disc.
The dynamics of the SGRM can be divided into
two parts. One is the flywheel system, which consists
of the flywheel itself and the flexible coupling. The
other is the Intelligent Posture Tracking System
(IPTS), which consists of the intelligent disc and the
HMAs. The posture of the flywheel, in fact, is the
target of tracking by the intelligent disc. Therefore,
for the purpose of posture tracking, the dynamics of
the flywheel system has to be modeled on the base of
the displacements in X- and Y-axes.
The reference frames of the flywheel are shown
in Fig. 3. The coordinate
},,{ ZYX denotes the
inertial reference frame and
},,{ CBA the frame
attached on the flywheel.
S is the centroid of the
flywheel,
P the center of mass of the flywheel, e
the eccentricity and
the argument of the eccentric
mass.
f
γ
,
f
β
and
are the yaw angle, pitch angle
and spin angle of the flywheel about X-, Y- and Z-
axes respectively. Since the vertically translational
stiffness of the flexible coupling is relatively high,
the translational displacement of the flywheel in Z-
axis direction is relatively insignificant and can be
neglected. The superscript “f ” is referred to the
flywheel.
f
m is the mass of the flywheel.
f
R
I and
f
P
I are the transverse mass moment of inertia and
the polar mass moment of inertia of the flywheel
respectively.
φ
&
=Ω is the rotational speed of the
flywheel.
θξ
sine
f
= and
θη
cose
f
= are the
projections of the eccentricity onto A- and B-axes
respectively. By Lagrange’s method, the equations
of motion of the flywheel can be obtained as
follows:
f
f
P
f
f
R
II
γβ
&
&&
Ω=
(1a)
f
f
P
f
f
R
II
βγ
&
&&
Ω−= (1b)
tmtmvm
ffffff
ΩΩ+ΩΩ= cossin
22
ζη
&&
(1c)
tmtmwm
ffffff
ΩΩ−ΩΩ= sincos
22
ζη
&&
(1d)
Because the dynamics of the flywheel system is
directly influenced by the flexible coupling, the
dynamics of the flexible coupling is analyzed by
Timoshenko beam theory and modeled by Finite
Element Method (FEM). A finite element of the
flexible coupling is shown in Fig. 4. An element of
the flexible coupling consists of two nodes. Each
node has four DOFs. The translational
displacements of an element of the flexible coupling
can be described as
),( tsw and ),( tsv in X- and Y-
axes directions respectively and the rotational
displacements are
),( ts
and ),( ts
respectively.
The displacements of an element of the flexible
coupling can be constructed as follows:
)()(
),(
),(
ts
tsv
tsw
T
e
qΨ=
⎥
⎦
⎤
⎢
⎣
⎡
(2a)
)()(
),(
),(
ts
ts
ts
T
e
qΦ=
⎥
⎦
⎤
⎢
⎣
⎡
β
γ
(2b)
where the superscript “
” denotes transpose
operator.
is the axial position along an element, t
the time instant and
],,,[
821
qqq
e
L=q the element
displacement vector of the flexible coupling.
Ψ and
Φ are the mode shape functions.
Eventually, the equations of motion of the flywheel
system with flexible coupling can be constructed by
combining Eq. (1) with Eq. (2) as follows:
tt
cs
Ω+Ω=+Ω++ cossin)( hhqKqGqNΜ
&&&
(3)
where
M , N , G and K are the translational mass
Contact-freeMagneticClutchAppliedforFlywheelCellSystem
369