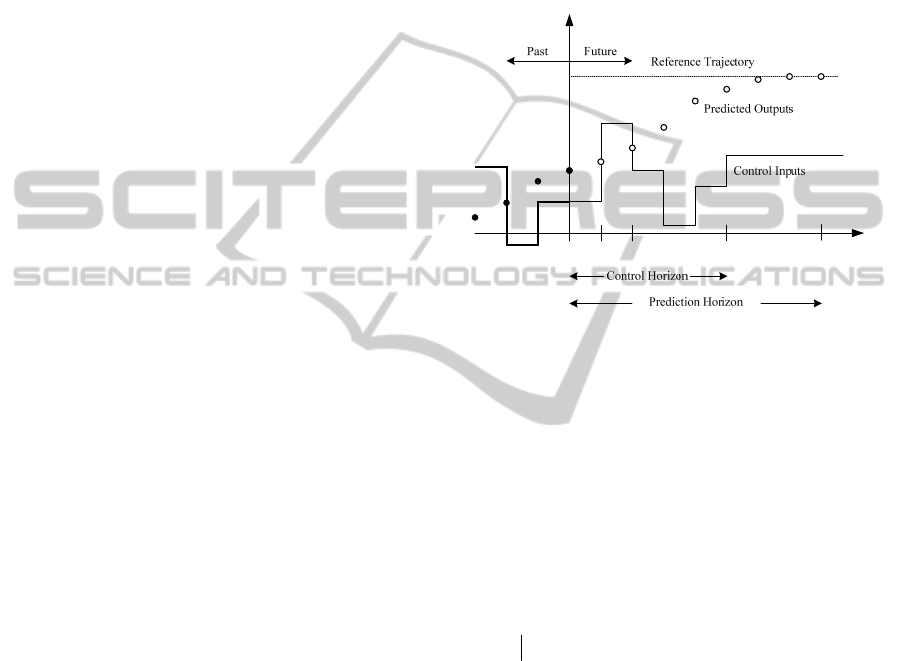
2 LOAD-FOLLOWING
OPERATION
Load following operation of a nuclear power plant
means the operation mode that reactor power
follows the load variation of the turbine. Daily load
following operation, frequency control operation,
and contingency power change operation belong to
the category of the load following operations. Daily
load following operation means that reactor power is
retained for a period of time as a constant rate of
change by up to 50%, and then return to 100%
power as a constant speed. However, the frequency
control operation of nuclear power plants causes the
frequent movement of control rods because of the
volatility of an ever-changing power system.
Therefore, the purpose of controller development
was set up to design the controller capable of daily
load following operation. Reactor power fluctuation
can be achieved by regulating the parameters that
cause the change of core reactivity. Core reactivity is
affected by changes of the boron concentration, fuel
and coolant temperature, xenon and samarium
concentration in the core.
Xenon and samarium concentrations are
excluded from the direct target which can be
controlled because it cannot be measured directly
during reactor operation, and fuel consumption rate
and fuel temperature are already determined in the
time of fuel loading. Control rod movement can be
used as a control factor for immediate reactor power
changes because it impacts on the reactor within a
few seconds, and the change of boron concentration
in the coolant should be used essentially to control
the surplus reactivity since it is affected to the
reactor within few minutes. Coolant temperature can
be used as a control factor which reduces the use of
control rods and boron.
3 DESIGN OF MODEL
PREDICTIVE CONTROLLER
The average coolant temperature and reactor power
distribution should be controlled at the same time for
load following operation. The MPC controller is
introduced for the automatically load following
operation of an APR+ reactor. It uses a control
method that can perform optimal control with the
predictive calculations. Through this study, an MPC
controller will be designed so that it can control the
average coolant temperature and power distribution
at the same time.
3.1 Basic Principle of MPC
MPC method can calculate control input of the
constant horizon by solving the optimization
problems about finite future time steps in the current
time, and actually implement solely the first optimal
input as a control input. As shown in the Figure 1,
new output is measured at the next time step, and
control horizon moves one step forward, and these
calculations are repeated.
t
1t
tM+
tP+
LL
ˆ
(|)
tkt+
()ut k
w
Figure 1: Concept of the Model Predictive Control.
The purpose of using a new measured value at
each time step is to compensate the model
inaccuracy or unmeasured disturbance. The basic
elements of MPC contain a specific model
(prediction model) for predicting the process output
of a point in the future, an objective functions and its
optimization.
Using this prediction model, outputs for the
prediction horizon
P ,
ˆ
[( |), 1,2, , ]tktk P+=y
L
are predicted, and these outputs depend on the past
input, output and future input (control signal),
[( ), 1,2, , ]tktk M+=u L
.
A series of optimal control signal is calculated by
optimizing a given objective function to let the
output follow the target output as fast as possible. In
case the objective function is quadratic form, and the
model is linear, and constraint does not exist, the
control input can be derived analytically. However
the actual control input in most of the processor
is obtained numerically. At this time, the optimal
control input is obtained in a range which satisfies
the constraints by including the constraint which will
be applied to the system to the
algorithm. Among the optimized control signals, the
first input
(/)ttu is sent only to the process input.
And the remaining control input signals are
meaningless because
(1)t
y
was already known in
Load-followingControlofAPR+NuclearReactors
447