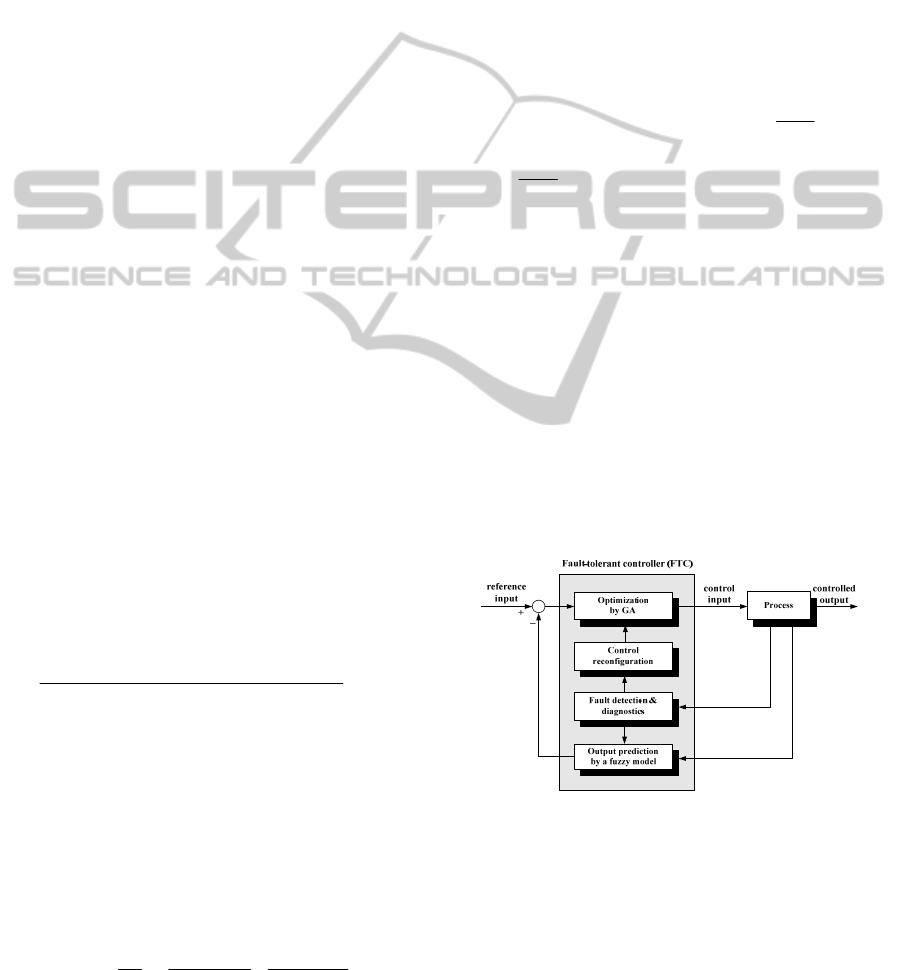
as soon as faults develop, so that the controllers are
automatically reconfigured and the further
deterioration is prevented.
In this work, a fault detection and diagnostics
algorithm is developed to estimate the input and
output measurements using a fuzzy model based on
the subtractive clustering method and to check the
operability of existing hardware sensors using a
sequential probability ratio rest (SPRT) so that the
FTC can handle the fault situations of the input and
output measurements or partial loss of actuators. In
this work, a fuzzy model is used to estimate the
input and output measurement signals. This fuzzy
model is another fuzzy model which is different
from the fuzzy model that predicts the system output,
which is needed to minimize the control objective
function.
The objective of sensor fault detection and
diagnostics is to diagnose sensor health as soon as
possible with a very small probability of making a
wrong decision. The SPRT uses the residual
(difference between the measured value and the
estimated value,
ˆ
() ()yt yt−
). Normally the residual
signals are randomly distributed, so they are nearly
uncorrelated and have a Gaussian distribution
function
(, , )
it i i
Pm
σ
, where
t
is the residual
signal at time instant
t
, and
i
m and
i
are the mean
and the standard deviation under hypothesis
i
,
respectively. The sensor degradation or fault can be
stated in terms of a change in the mean
m
or a
change in the variance
2
. Therefore, the SPRT
detects sensor health by sensing the alteration of the
probability distribution. If a set of samples,
i
,
1, 2, ,ik= L , is collected with a density function
describing each sample in the set, an overall
likelihood ratio is given by
11 1 12 1 13 1 1 1
01 0 02 0 03 0 0 0
(|)(|)(|) (|)
(|)(|)(|) (|)
k
k
k
PHPHPHPH
HP HP H P H
εεε ε
γ
εεε ε
⋅⋅⋅⋅⋅
=
⋅⋅⋅⋅⋅
(8)
where
0
represents a hypothesis that the sensor is
normal and
1
represents a hypothesis that the
sensor is degraded.
By taking the logarithm of the above equation
and replacing the probability density functions in
terms of residuals, means and variances, the log
likelihood ratio can be written as the following
recurrent form:
22
00 1
1
22
1
01
()()
ln
22
kk
kk
mm
σε ε
λλ
σ
σσ
−
⎛⎞
−−
=+ + −
⎜⎟
⎝⎠
(9)
This ratio is used for deriving the sensor drift
detection algorithm. For a normal sensor, the log
likelihood ratio would decrease and eventually reach
a specified bound
, a smaller value than zero.
When the ratio reaches this bound, the decision is
made that the sensor is normal, and then the ratio is
reinitialized by setting it equal to zero. For a
degraded sensor, the ratio would increase and
eventually reach a specified bound
, a larger value
than zero. When the ratio is equal to
, the decision
is made that the sensor is degraded. The specified
bounds
A
and
are important in determining the
sensor faults. The decision boundaries
and
are
chosen by a false alarm probability
and a missed
alarm probability
;
ln
1
A
β
=
−
⎛⎞
⎜⎟
⎝⎠
and
1
lnB
α
−
=
⎛⎞
⎜⎟
⎝⎠
.
The input signal is the control drum angle to
regulate the reactivity and the output signal to be
controlled is the TE power. Also, to handle the sensor
faults, the input and output signals of the control
system are estimated by using a fuzzy model for
signal estimation from the measurements of the SP-
100 reactor system. If the input or output sensors are
normal, the measured values are used to predict the
future control system output. But if they are
determined to be degraded or faulty, the faulty sensors
are isolated and the estimated sensor signals instead
of the measured values are used to predict the future
system output. The schematic block diagram of the
proposed FTC is illustrated in Figure 1.
Figure 1: Block diagram of the proposed FTC for an SP-
100 space reactor.
4 APPLICATION TO THE SP-100
SPACE REACTOR
The reactor system of the SP-100 space reactor is
made up of a reactor core, a primary heat transport
ICINCO2012-9thInternationalConferenceonInformaticsinControl,AutomationandRobotics
454