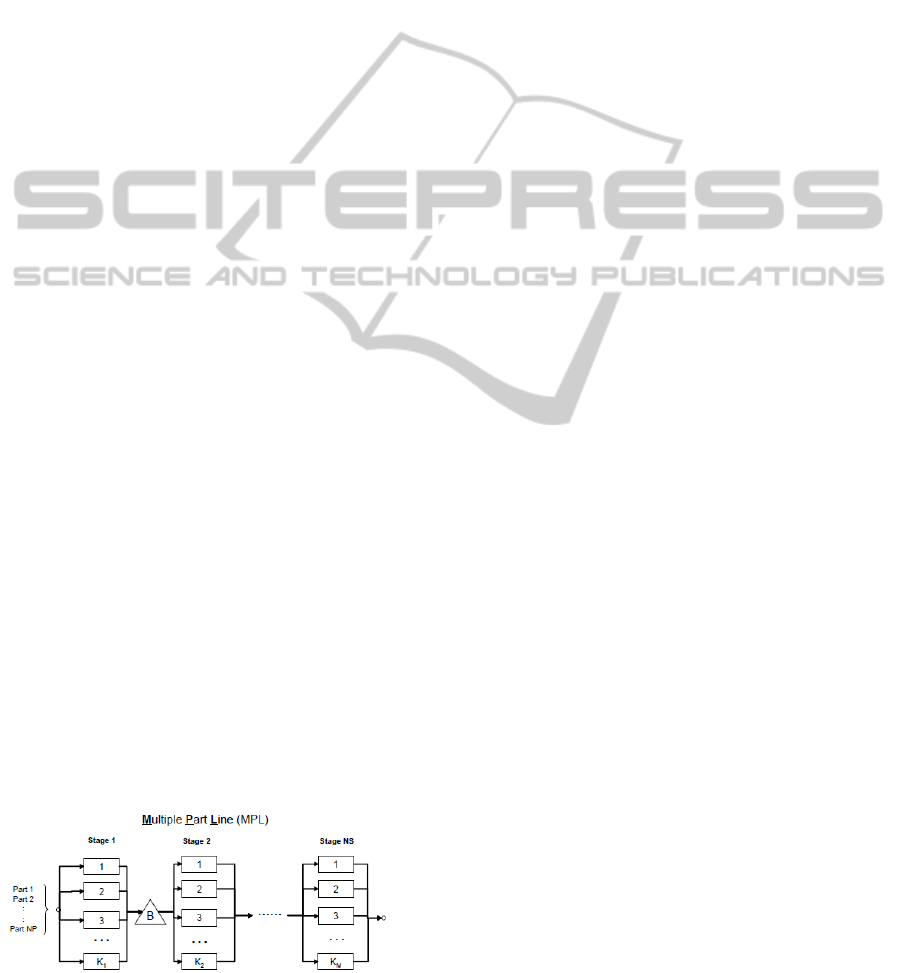
family. The first stage in the method is a calculation
of the number of machines required to complete an
operation. The number of machines N, may be
arranged in a variety of different configurations. The
minimum number of stages in a configuration is
limited to the number of machine setups required to
produce the part family. Koren’s method requires
the manual population of a space of potential
configurations. The selection of an optimal
configuration then proceeds by eliminating those
configurations that cannot meet the required
production rate. Consideration is also given to
system throughput with machine reliability less than
100%, investment cost, scalability and floor space.
Koren and Shpitalni presented a manual method of
enumerating and evaluating candidate RMS
configurations. The number of configurations that N
machines may assume, grows factorially with the
number N. This method therefore requires
substantial amounts of time and human effort to
enumerate and evaluate different configurations.
The use of the Analytic Hierarchy Process,
(AHP), was proposed by (Abdi, 2005) for the design
of a suitable RMS. The AHP was originally
developed by Thomas L. Saaty and the details of this
algorithm may be found in (Saaty, 2008). The AHP
requires a set of design alternatives and a set of
design criteria as inputs to the algorithm. Abdi listed
reconfigurability, cost, quality and reliability as the
design objectives. The implementation presented by
Abdi required the manual enumeration of possible
RMS design configurations. This method, like
(Koren and Shpitalni, 2010), is unappealing due to
the time required to enumerate and rank various
configurations.
The use of a Genetic Algorithm to design a
Multiple Part Line (MPL) for RMSs was proposed
by (Tang et al., 2003). Tang defined a MPL as a line
that consists of several serial stages with a finite size
buffer between every two stages. Each stage consists
of identical machines in parallel that perform the
same set of tasks. The problem formulation
restricted the MPL to the production of a given part
family. It was assumed that the number of stages in
the MPL is predetermined by the designer and each
Figure 1: Illustration of a Parallel MPL (Tang et al., 2003).
part visits every stage in the MPL. The objective of
the optimisation was therefore, to allocate machines
to the various stages of the MPL from a given
library of available machines. Limitations in this GA
implementation include the specification that the
RMS layout assumed a form as depicted in Figure 1.
3 PARALLEL DEVS
SIMULATION
The use of computer simulation for the design of
RMSs has been largely overlooked. This research
pursues the use of simulation for manufacturing
system design within an automated framework. The
Parallel Discrete Event System (Parallel DEVS)
specification has been chosen as the formalism for
the simulator. DEVS was selected because the
formalism is hybrid, i.e capable of modelling both
discrete event and discrete time systems. The
formalism is also modular and hierarchical thus
making it suitable for creating manufacturing system
models that can be generated and modified
automatically during the execution of a genetic
algorithm. The Parallel DEVS variation of the
original DEVS formalism was introduced (Chow
and Zeigler, 1994). A Parallel DEVS model consists
of Atomic Models that are networked to form
coupled models. An Atomic DEVS model M is an 8-
tuple defined by:
Where:
X: is a set of input events;
Y: is a set of output events;
S: is a set of sequential states;
δ
ext
: Q × X
b
→ S, is an external transition function;
where Q = {(s,te)|s
S, 0≤te≤ta(s)} is the total state
set of M and te is the time elapsed since the last the
last event;
δ
int
: S → S, an internal transition function;
δ
con
: S × X
b
→ S, is the confluent transition function;
λ: S → Y
b
, is an output function;
ta: S → Real, is the time advance function.
Atomic DEVS models have been used to model the
elementary components of a manufacturing system
such as buffers, machines, assembly stations, human
labourers, robots and material transport systems.
Atomic models are stored in a manufacturing
resource/ equipment library:
Atomic models from this library are selected to
create candidate design solutions for a
ICINCO 2012 - 9th International Conference on Informatics in Control, Automation and Robotics
154