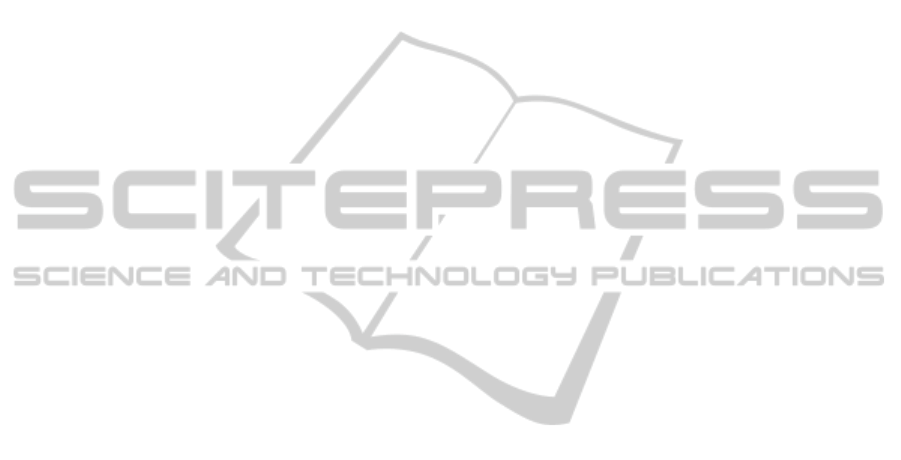
wastewater pumping station in northern Gaza. The
resultant model provides a practical tool for
examining the system control under different running
conditions, such as pump failure and changing flow
rates. This simulation model assists in adjusting the
control reference points and parameters to cope with
regular and undesired situations. The simulated
control algorithm is widely used in pumping stations
and it is believed that it works to minimize
maintenance and running costs by minimizing the
number of running pumps and limiting the number of
their restarts for a certain inlet rate.
At the present phase, the ponds of the old
treatment plant serve as a buffer for the wastewater
before being pumped via the NTPS to the new
treatment plant. This buffering stage will not be
available by the completion of the project as the old
plant will be removed and incoming wastewater is
planned to be transmitted directly to the new
treatment plant. Only one small size pond will be left
for collecting emergency overflows at the pumping
station. As a result, the real challenge of the control
problem is not the present phase where a fixed daily
amount of wastewater needed to be transported. In the
final phase, the pump station must handle
instantaneous variation of the wastewater flow.
Accidental overflow will result in an additional re-
pumping cost and undesired environmental
consequences. Therefore, an estimate of the daily
diurnal flow pattern is necessary to examine the plant
controller under daily variation of wastewater flow.
In a future work, we plan to model the daily
diurnal flow pattern and formulate a quantitative
performance measures for running the system. This
will enable us to develop a criterion for optimal
control of pumping stations. We will employ
simulations over long time horizons to respect
special conditions found in Gaza but also many
other developing areas. For example, frequent
failure in the main electric power supply is common
in Gaza city nowadays and requires intensive
operator supervision. Moreover, power produced by
the standby generators is much more expensive than
the power of the main supply. This is a point
normally not considered in deriving the control laws.
Models implementing functions to derive the total
cost of operation similar to models presented in
(Felgner et al., 2011) combined with predictive –
simulation based – hybrid control schemes as in
(Sonntag et al., 2009) are expected to be of great
value under these conditions.
ACKNOWLEDGEMENTS
The authors would like to express their gratitude to
Alexander von Humboldt Foundation for supporting
this work.
REFERENCES
Abdelati, M., Rabah, F., 2007. A Framework for Building
a SCADA System for Beit Lahia Wastewater Pumping
Station, The Islamic University Journal, Natural
Studies and Engineering Series, Vol.15, No. 2, pp
235-245, ISSN 1726-6807.
Abdelati, M., Felgner, F., Frey, G., 2011. Modeling,
simulation and control of a water recovery and
irrigation system, Proceedings of the 8th International
Conference on Informatics in Control, Automation and
Robotics. Noordwijkerhout, The Netherlands.
Astrom, K., Hagglund, T., 1995. PID Controllers: Theory,
Design, and Tuning, North Carolina, Instrument
Society of America, 2nd edition.
Brater, E., King, H., Lindell, J., 1996. Handbook of
Hydraulics, Mc Graw Hill, New York, 7th Edition.
Dynasim AB, 2010. Dymola Dynamic Modeling
Laboratory User Manual. Sweden.
Elmqvist, H., Tummescheit, H., Otter, M., 2003. Object-
Oriented Modeling of Thermo-Fluid Systems,
Proceedings of the 3rd International Modelica
Conference, Linköping.
Felgner, F., Exel, L., Frey, G., 2011. Component-oriented
ORC plant modeling for efficient system design and
profitability prediction. Proceedings of the IEEE/IES
International Conference on Clean Electrical Power
(ICCEP 2011), Ischia , Italy, pp. 196-203.
Jensen, J., 2003. Dynamic Modeling of Thermo-Fluid
Systems with focus on evaporators for refrigeration.
Ph.D. Thesis, Department of Mechanical Engineering,
Technical University of Denmark.
Link K., Steuer H., and Butterlin A., 2009. Deficiencies of
Modelica and its simulation environments for large
fluid systems, Proceedings 7th Modelica Conference,
Como, Italy.
Palestinian Water Authority, 2004. Bidding Documents for
the Construction of Terminal Pumping Station,
NGEST project management unit, Gaza.
Sonntag, C., Kölling, M., Engell, S., 2009. Sensitivity-
based Predictive Control of a Large-scale Supermarket
Refrigeration System. Int. Symp. on Advanced Control
of Chemical Processes (ADCHEM), Istanbul/Turkey,
pp.354-359.
Tiller M., 2004. Introduction to Physical Modeling with
Modelica, Kluwer Academic Publishers.
Massachusetts, 2
nd
Edition.
Werner M. et al., 2006. North Gaza Emergency Sewage
Treatment Plant Project - Environmental Assessment
Study, Engineering and Management Consulting
Center.
ICINCO2012-9thInternationalConferenceonInformaticsinControl,AutomationandRobotics
384