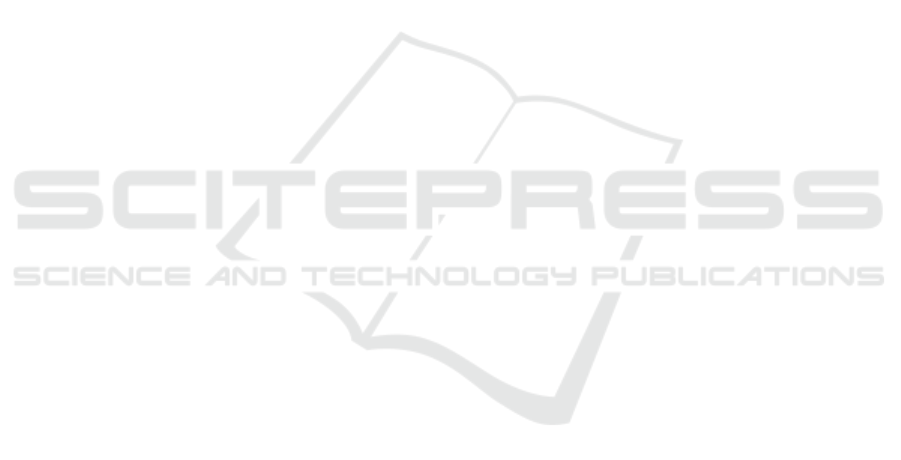
Mechatronic System Optimization based on Surrogate Models
Application to an Electric Vehicle
Moncef Hammadi, Jean-Yves Choley, Olivia Penas and Alain Riviere
LISMMA, SUPMECA-PARIS, 3 Rue Fernand Hainaut, 93400 Saint-Ouen, France
Keywords:
Mechatronic Design, Optimization, Surrogate Models, Modelica, Electric Vehicle.
Abstract:
Preliminary optimization of mechatronic systems is an extremely important step in the development process of
multi-disciplinary products. However, long computing time in optimization based on multi-domain modelling
tools need to be reduced. Surrogate model technique comes up as a solution for decreasing time computing in
multi-disciplinary optimization. In this paper, an electric vehicle has been optimized by combining Modelica
modelling language with surrogate model technique. Modelica has been used to model the electric vehicle
and surrogate model technique has been used to optimize the electric motor and the transmission gear ratio.
Results show that combining surrogate model technique with Modelica reduces significantly computing time
without much decrease in accuracy.
1 INTRODUCTION
Mechatronic Systems (MS) are interdisciplinary
products with a synergistic spatial and functional in-
tegration of mechanical, electronic and software sub-
systems (Craig, 2009).
The great challenge in mechatronic design lies in
optimizing a complete system with various physical
phenomena related to interacting heterogeneous sub-
systems.
Several multi-domain modelling tools such as
Bond-Graphs, VHDL-AMS, Matlab/Simulink and
Modelica are used for preliminary design of MS.
For instance, Modelica (Elmqvist et al., 1998)
combines object-oriented concepts with multi-port
methods for modelling and simulation of physical
systems. It includes a declarative mathematical de-
scription of models and provides a graphical mod-
elling approach. Multi-domain model library of
lumped parameter elements can be created and added
to the default Modelica library for future use. The
end results of Modelica modelling is a system of
differential-algebraic equations (DAE) that represents
the complete mechatronic system. So that, Modelica
is considered as an ideal tool for preliminary design
of MS. However, optimizing a mechatronic system
based on DAE is computationally expensive, due to
the considerable number of simulation evaluations.
For this reason, substituting DAE system with sur-
rogate models, using statistical methods, is one way
of alleviating this burden. The polynomial Response
Surface Method (RSM) (Box and Wilson, 1951) is
commonly considered as the first surrogate modelling
technique. It uses a polynomial formulation to ap-
proximate anexact function. Other techniques such as
Kriging (Krige, 1951) and Artificial Neural Networks
(ANNs) of Radial Basis Functions (RBF) (Hardy,
1971), (Hopfield, 1982) and (Powel, 1985) are also
used to model complex relationships between inputs
and outputs. Surrogate models are also known as
metamodels (Blanning, 1975).
In this paper, both RMS and ANNs of RBF sur-
rogate models have been generated from a Modelica
model of an Electric Vehicle (EV). After their val-
idation and comparison of their accuracy, the ANN
of RBF surrogate model has been chosen to optimize
the electric motor and the gear ratio of the EV. The
optimization based on the surrogate model has been
comparedwith an optimization based on the Modelica
model. Results found are compared with a real case of
an electric vehicle developed by general motors(GM
EV1). Results show an interesting reduction in com-
puting time of optimization without significantly af-
fecting the accuracy.
2 SURROGATE MODELLING
RSM and ANNs of RBF have been used in this study
due to their high accuracy and ease of use. The prin-
11
Hammadi M., Choley J., Penas O. and Riviere A..
Mechatronic System Optimization based on Surrogate Models - Application to an Electric Vehicle.
DOI: 10.5220/0004011900110016
In Proceedings of the 2nd International Conference on Simulation and Modeling Methodologies, Technologies and Applications (SIMULTECH-2012),
pages 11-16
ISBN: 978-989-8565-20-4
Copyright
c
2012 SCITEPRESS (Science and Technology Publications, Lda.)