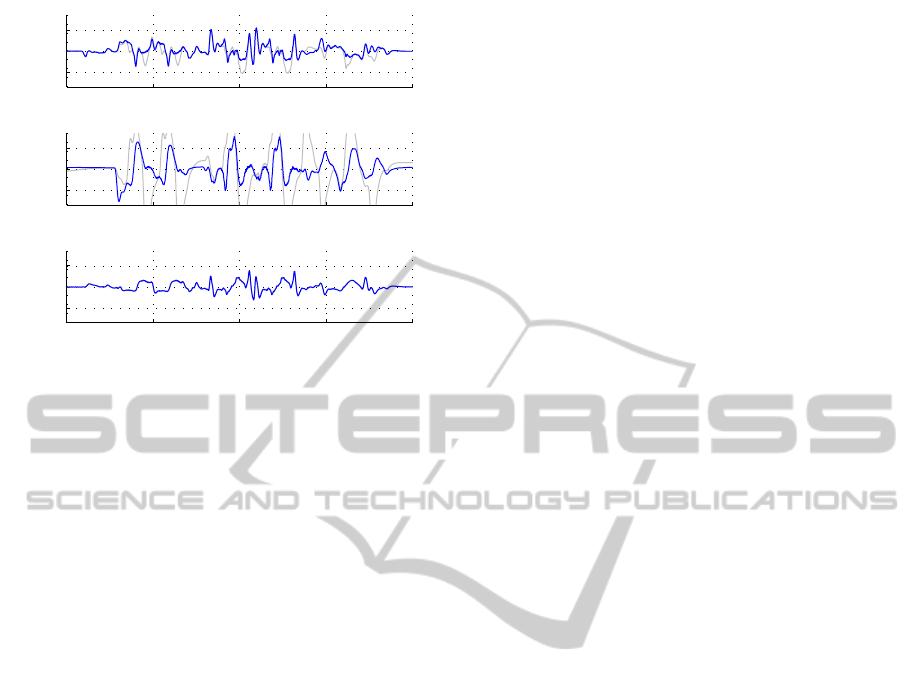
t in s
z− z
d
in mm
y− y
d
in mm
x− x
d
in mm
0 10
20 30 40
0 10 20 30 40
0 10 20 30 40
−10
0
10
−10
0
10
−10
0
10
Figure 8: Tracking errors during the fast ISO 9283 test with
(regular line) and without (light line) hysteresis compensa-
tion in the first joint.
grator part and the hysteresis compensator as well as
devise models for the other joints. Furthermore, us-
ing the compensator in a disturbance force observer
would be an interesting scenario.
ACKNOWLEDGEMENTS
This work was supported by the Austrian Center
of Competence in Mechatronics (ACCM) and the
ODEUO project, an experiment funded in the context
of the European Clearing House for Open Robotics
Development (ECHORD) project.
REFERENCES
Aschemann, H. and Schindele, D. (2008). Sliding-mode
control of a high-speed linear axis driven by pneu-
matic muscle actuators. Industrial Electronics, IEEE
Transactions on, 55(11):3855–3864.
Boblan, I. (2009). Modellbildung und Regelung eines flu-
idischen Muskelpaares. PhD thesis, Technical Univer-
sity Berlin.
Chou, C.-P. and Hannaford, B. (1994). Static and dynamic
characteristics of McKibben pneumatic artificial mus-
cles. In Robotics and Automation, 1994. Proceedings.,
1994 IEEE International Conference on, volume 1,
pages 281–286.
Davis, S. and Caldwell, D. G. (2006). Braid effects on con-
tractile range and friction modeling in pneumatic mus-
cle actuators. The International Journal of Robotics
Research, 25(4):359–369.
Ferreau, H., Bock, H., and Diehl, M. (2008). An online ac-
tive set strategy to overcome the limitations of explicit
MPC. International Journal of Robust and Nonlinear
Control, 18(8):816–830.
Hill, A. V. (1938). The heat of shortening and the dy-
namic constants of muscle. Proceedings of the Royal
Society of London. Series B, Biological Sciences,
126(843):136–195.
Kerscher, T., Albiez, J., Z¨ollner, J., and Dillmann, R.
(2006). Evaluation of the dynamic model of fluidic
muscles using quick-release. First IEEE / RAS-EMBS
International Conference on Biomedical Robotics and
Biomechatronics.
Klute, G. K., Czerniecki, J. M., and Hannaford, B. (2002).
Artificial muscles: Actuators for biorobotic sys-
tems. The International Journal of Robotics Research,
21(4):295–309.
Krichel, S., Sawodny, O., and Hildebrandt, A. (2010).
Tracking control of a pneumatic muscle actuator us-
ing one servovalve. In American Control Conference
(ACC), 2010, pages 4385–4390.
Kuhnen, K. (2003). Modeling, identification and compen-
sation of complex hysteretic nonlinearities: A modi-
fied Prandtl-Ishlinskii approach. European Journal of
Control, 9:407–418.
Minh, T., Tjahjowidodo, T., Ramon, H., and Van Brussel,
H. (2009). Control of a pneumatic artificial mus-
cle (PAM) with model-based hysteresis compensa-
tion. In Advanced Intelligent Mechatronics, 2009.
AIM 2009. IEEE/ASME International Conference on,
pages 1082–1087.
Minh, T. V., Kamers, B., Tjahjowidodo, T., Ramon, H.,
and Van Brussel, H. (2010). Modeling torque-
angle hysteresis in a pneumatic muscle manipula-
tor. In Advanced Intelligent Mechatronics (AIM),
2010 IEEE/ASME International Conference on, pages
1122–1127.
Minh, T. V., Tjahjowidodo, T., Ramon, H., and Van Brussel,
H. (2011). A new approach to modeling hysteresis in
a pneumatic artificial muscle using the Maxwell-slip
model. Mechatronics, IEEE/ASME Transactions on,
16(1):177–186.
Reynolds, D. B., Repperger, D. W., Phillips, C. A., and
Bandry, G. (2003). Modeling the dynamic character-
istics of pneumatic muscle. Annals of Biomedical En-
gineering, 31:310–317.
Tondu, B. and Lopez, P. (2000). Modeling and control of
McKibben artificial muscle robot actuators. Control
Systems, IEEE, 20(2):15–38.
Tondu, B. and Zagal, S. (2006). McKibben artificial mus-
cle can be in accordance with the Hill skeletal muscle
model. In Biomedical Robotics and Biomechatronics,
2006. BioRob 2006. The First IEEE/RAS-EMBS Inter-
national Conference on, pages 714–720.
Van Damme, M. (2009). Towards Safe Control of a Com-
pliant Manipulator Powered by Pneumatic Muscles.
PhD thesis, Vrije Universiteit Brussel.
EvaluationofaJointHysteresisModelinaRobotActuatedbyPneumaticMuscles
235